Outbuild is online scheduling software to work together on connected project schedules and look-aheads, enabling everyone to move faster.
Key Takeaways
Table of contents
- Rework: The Profit Poison of the Construction World
- Poor Communication = Rework On the Way
- 4 Elements of a Quality Control Plan Based on Good Communication
- Tech as an Indispensable Tool in Construction Quality Control
- Integrated Planning and Scheduling Software: Modern QC’s Silver Bullet
- Ongoing Quality Control Measures on Construction Sites—Going Digital
- A Digital Approach to Ongoing Quality Control Challenges and Best Practices
- The Takeaway: Digitized Quality = Solidified Success
Learn why good QC is fundamental to success, the reason behind its common tendency to fail, and how to fix it fast.
On a summer day in 1981, poor construction quality control (QC) saw what was possibly its darkest moment.
Two skywalks in the Hyatt Regency Hotel in Kansas City, Missouri, collapsed onto a crowded atrium. The impact killed 114 people and injured over 200†.
Afterward, investigations turned up a series of avoidable errors, including faulty design calculations and just plain poor oversight.
What had appeared to be a minor change in the skywalk’s suspension system had doubled the load on a critical connection, causing the collapse.
It was one of the deadliest structural failures in U.S. history and a harsh reminder of how catastrophic the consequences of bad QC can be.
With its interplay of design, materials, and workmanship, construction project complexity demands a serious take.
More often though, bad QC doesn’t kill people—it destroys profits.
And while that might not be as dark, it can still mean the difference between a company handing out layoffs and shutting its doors versus handing out promotions and expanding its headquarters.
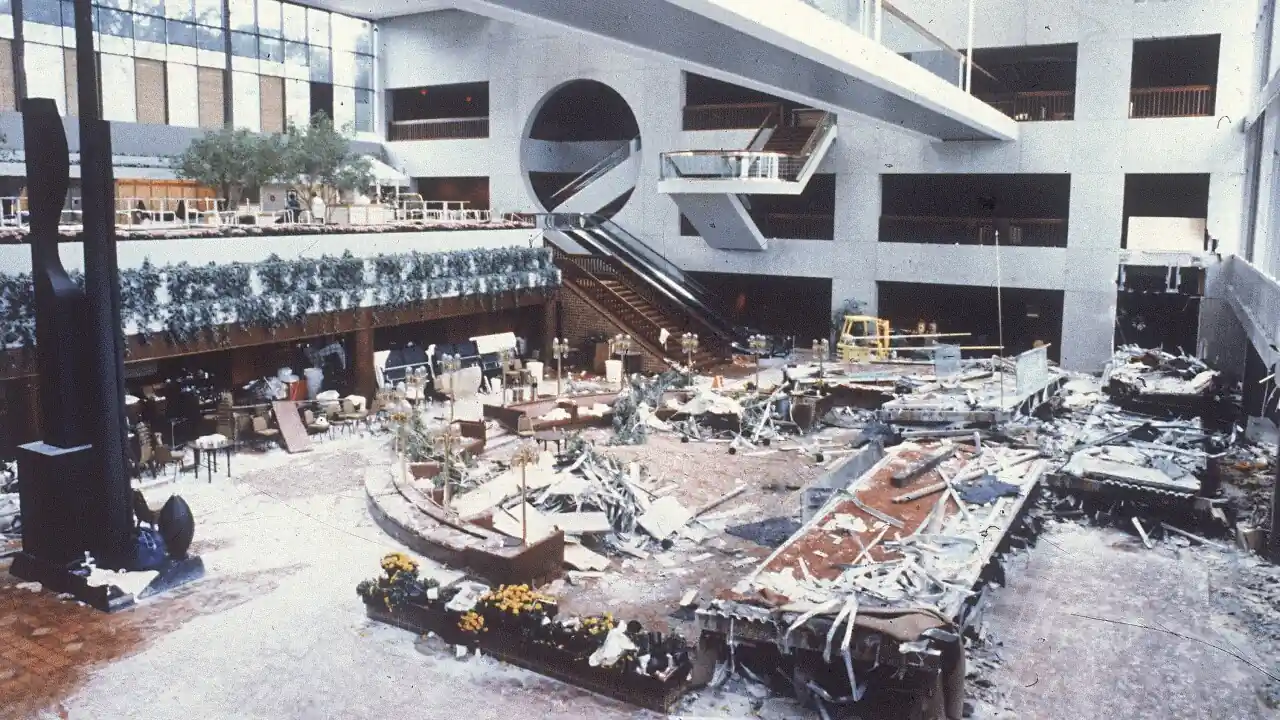
When it comes to quality control construction industry lingo, “rework” is probably the most dreaded of all words.
Rework means pouring tons of time, money, and effort into a project only to see a big chunk of its profits go down the drain due to preventable mistakes.
Rework is ultra-costly, ultra-time-consuming, and, unfortunately, the most common consequence of bad QC and what makes it so bad for the bottom line.
To get a feel for how common this dreaded problem is, consider this: studies show that rework accounts for about 30% of the total work done on construction sites. That’s a serious chunk.
The only surefire safeguard against this huge problem is good quality control in construction project management.
As a straightforward, farseeing approach, quality control confirms that every aspect of the project, from materials to workmanship, adheres to the required standards.
With such a clear solution available to everyone, why is rework so common? The answer is simple: poor communication.
The secondary cause of a construction quality control failure can be a missed design calculation, as in the case of the Hyatt Skywalk. It could also be things like a scope that skipped a step in development or an outdated documentation process. The possibilities are endless.
Whatever the secondary cause, the primary cause of bad QC and its resulting failures is most often poor communication. In fact, one recent report showed miscommunication as a major contributor to rework in 48% of cases.
And we all know exactly what it looks like…
- Conflicting Info. Two layouts of the same project are floating around, and one has a design discrepancy. If there’s poor communication between the two teams working with these separate layouts, it means one thing: rework will happen.
If there’s good communication, the conflicting information will be brought to light and addressed. (It’s worth noting that, with a culture of good communication, the separate layouts probably would never exist in the first place.). - Procurement Issues. The same applies to supply delays or client changes to the project scope. If everyone on the team knows about the changes or issues, there’s no monkey wrench in the works. The whole crew operates as a cohesive unit based on the same information.
- Planning Errors. This one is really simple. With good communication, potential trouble like poor scope definition or insufficient front-end planning never makes it far enough down the pipeline to cause profit problems.
- Outdated Documentation Systems. Take missing and inaccurate documentation, season it with a touch of disorganization, and you’ve got a recipe for rework. Modern documentation systems support real-time communication to avoid these issues.
So, if poor communication is the problem, good communication is the obvious solution. Here’s what that looks like on the ground…
Good communication is the bedrock of successful quality control in construction industry projects. There are several types of quality control in construction, but any solid QC plan will include the following interconnected elements:
#1 - Clear Standards and Specs
Ambiguity is the enemy of communication—and quality. When the rules are all over the place, and the specs are anyplace, crews are bound to flounder.
On the flip side, when there’s a clear, shared set of standards and specifications, everyone on the project has a “true north.” There’s a shared direction and guide that leads your projects toward profitability.
#2 - Regular Inspections
According to research, projects with consistent inspection protocols have significantly lower failure rates. And it makes sense: if profitability is a project’s lifeblood, regular quality inspections are its routine health checkups.
During these inspections, the PM or inspector compares the project to the pre-established standards and specs (element #1). If any element fails the test, the team can address and correct the problem before it gets out of control.
Then, toward the end of the inspection sequence, the punch list process kicks in to finalize the granular elements.
#3 - Corrective Action Procedures
With established standards and specs in place (element #1), QC pros can design detailed action plans for addressing and correcting anything that’s determined to miss the mark during routine inspections (element #2).
For example, imagine there’s a foundation pour where an inspection reveals that the concrete mix doesn't’ meet the specified strength. As a result, the corrective action procedure kicks in.
The team halts the pour, adjusts the mix to meet the standards, and conducts a follow-up inspection before resuming work.
#4 - Planning and Documentation
As mentioned, planning and documentation are the communication-glue that holds the fabric of QC together.
- They give you a framework for and allow you to record and communicate standards and specs (element #1)
- They allow you to capture every aspect of an inspection (element #2)
- And they allow you to record corrective actions (element #3) for future use
More importantly, effective planning and documentation enable real-time communication across your team, keeping everyone on the same page and providing a trail of accountability and transparency.
And this is where the importance of technology comes into the picture.
Technology is reshaping how we approach construction quality control and monitoring, introducing a wave of tools that improve processes and accuracy.
Today, aerial inspection drones give QCs a bird's-eye view of construction sites, quickly pinpointing potential problems like structural defects or material discrepancies.
Building Information Modeling (BIM) allows stakeholders to create a digital twin of a project for clash detection and virtual walk-throughs before construction even begins.
Sensor technology embedded in structures can monitor real-time data like temperature, humidity, and vibrations and alert teams to problems before they become major disasters.
These amazing advances are taking QC and public safety to a whole new level.
However, the fastest aerial drones and most sensitive sensors are only useful if excellent communication and planning are in place to disseminate and implement the information and improvements they provide.
That’s why the real power of modern construction QC lies in technology that supports communication, documentation, planning, and scheduling.
The construction world is teeming with tech systems, but there are two major problems:
- The majority of these systems are decentralized and patchy
- No one in the field wants to use them
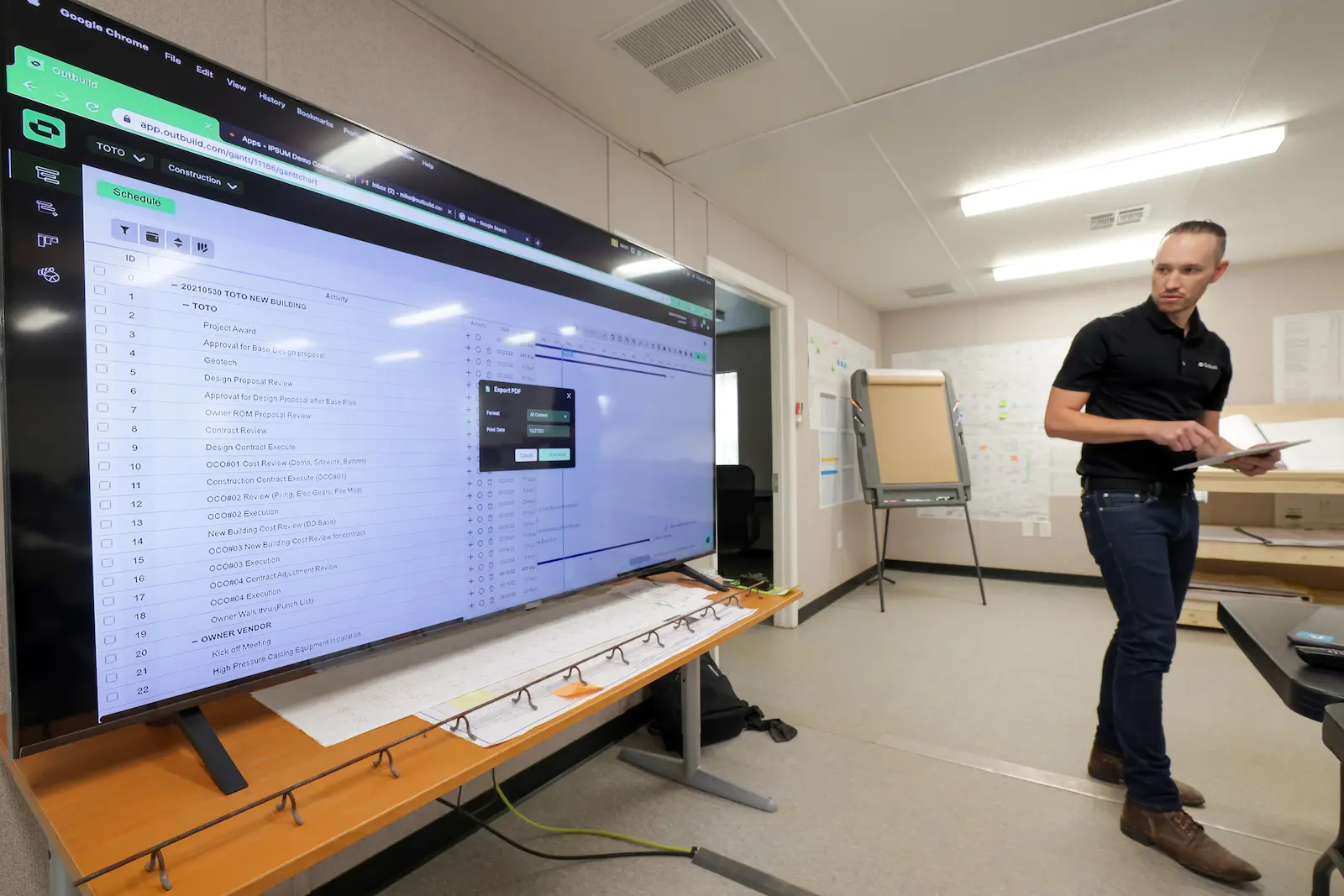
Getting crews on board with software systems is one of the biggest problems project managers face in the field. And it's no wonder. The systems are not only hard to understand but also ineffective.
For example, Idaho-based McAlvain Companies Inc. had teams trying to manage their schedules using separate systems, which created communication gaps, increased risks, and more work.
QC efforts were there, but communication was so disconnected and the system so confusing it might as well have been analog.
Once they implemented Outbuild’s centralized and integrated scheduling and planning system alongside Procore, McAlvain saw a massive increase in team opt-in and massive improvements in quality and profits.
As a Last Planner System® (LPS) software, Outbuild digitizes the construction quality control process by connecting the master schedule with lookahead plans, and then supporting real-time documentation and collaboration across the organization.
With the software, project teams can identify, communicate, and address potential concerns before they become major mistakes, saving time, money, and resources. It completely eliminates the communication gaps that often plague construction projects.
This smooth flow of information keeps everyone working from the most current plans, reducing the chance of rework, and improving attitudes toward opt-in.
Quality control is an ongoing process integrated into every stage of the building process. Following are the three main ongoing QC protocols and how they can be supported digitally:
- Material testing evaluates the physical and chemical properties of construction materials against a set of standards (e.g., concrete compression and steel tensile testing).
You can gather test results and enter them into Outbuild's reporting and analytics system where they’re then tracked, integrated into the project schedule, and distributed project-wide.
This way, you can guarantee materials meet quality standards before they’re used on the site, preventing delays and rework. - Workmanship inspections assess the quality and accuracy of construction work (e.g., wall alignment or electrical system installation inspections).
Outbuild’s collaborative schedule creation and management tools help you coordinate these inspections by integrating them into the project timeline. Then crews know when inspections are scheduled and completed.
With the software’s real-time updates feature, you can communicate inspection results immediately, allowing for quick fixes. - Testing and commissioning processes verify the performance of building systems and components up against design specifications and functional requirements (e.g., functional performance testing and system balancing).
With Outbuild's lookahead planning function, you can break down the commissioning process into manageable tasks. Then, its real-time reporting feature can help you monitor task progress.
Transitioning to digitized construction quality control can improve your team’s efficiency and effectiveness like nothing else. But with day-to-day QC comes day-to-day challenges.
Again, by taking the digital approach, you can address common challenges and adopt best practices much more smoothly.
Below, we’ll give you a quick rundown of the most common challenges in ongoing QC. We’ll also explain how you and your team can tackle these challenges by taking a digital approach to best practices with Outbuild.
Time Constraints
Quality control during construction processes takes time, which is why pressure to meet deadlines is a major culprit in compromised quality. Pull planning, a lean construction method, is one of the best approaches to alleviating time constraints, creating a more predictable workflow, and eliminating that pressure.
Outbuild is a pull planning powerhouse. Its scheduling and lookahead planning features make it super simple to break down complex schedules into manageable tasks, making it easy to meet deadlines without sacrificing quality.
Irregular and Unstructured Inspections
Regular, predictable inspections, just like routine maintenance for a car, can identify and address minor issues before they escalate into profit-killing problems.
As we mentioned, Outbuild integrates inspection schedules into the master project timeline, then lets you communicate inspection results team-wide. So you can make certain that inspections (and their results) are never overlooked.
When it comes to conducting construction site quality control inspections, it can be tough to figure out how to structure things. Outbuild’s customizable task views and checklist features are the perfect solution.
Checklists are incredibly easy to customize to specific tasks or project phases, and you can rest assured that nothing is overlooked.
Cost Constraints
Extensive QC measures can be perceived as an unwelcome expense. However, the evidence is clear: investing in QC upfront reduces project costs by minimizing rework.
Outbuild’s analytics and reporting tools help track the cost benefits of digital quality control measures, demonstrating the value of upfront investments in QC.
Communication Gaps and Missed Documentation
We’ve already said it, but it really can’t be said too much: poor communication is a quality killer and profit drain.
Outbuild is the ultimate construction communication tool and collaboration hub. Instead of wasting time with phone tag, text messages, and unanswered email, your team gets a virtual, real-time meeting room where they’re surrounded by data that matters.
That data is thanks to features like Percent Plan Complete (PPC), Percent Roadblock Removed (PRR), and S-Curve analysis, that generate real-time insights into project performance.
These insights empower you and your team to make informed decisions that drive higher quality and way more profitable project outcomes.
Even better, all this data is rounded up into detailed digital docs stored safe and sound in the cloud for future reference and continuous improvement.
Using digitized quality control tools like Outbuild transforms the construction process, addressing challenges while promoting best practices.
Real-time progress tracking, collaborative scheduling, and detailed documentation help manage time constraints, conduct regular inspections, and maintain cost-effectiveness. These digital solutions reduce communication gaps and support thorough inspections with customizable checklists, leading to fewer errors and rework.
Reflecting on the 1981 Hyatt Regency skywalk collapse highlights the importance of quality control. The disaster, caused by avoidable errors and poor oversight, resulted in tragic loss of life and serves as a stark reminder of the stakes involved.
As we all know, poor QC kills way more profits than it does people, leading to layoffs and even company closures. By adopting advanced digital tools, the construction industry can prevent these kinds of tragedies and financial setbacks.
The digital approach enhances safety and supports business growth and stability, ultimately leading to a more efficient and successful construction industry.
Ready to change the way you build? Try Outbuild's construction scheduling software and experience the benefits firsthand. Give Outbuild a totally free test run today!
Frequently Asked Questions
Related Articles
Ready to see Outbuild?
Join hundreds of contractors from 10+ countries that are saving money by scheduling better