Outbuild is online scheduling software to work together on connected project schedules and look-aheads, enabling everyone to move faster.
Key Takeaways
Table of contents
- What is the Last Planner System (LPS)?
- Key Principles of the Last Planner System
- But, Can We Implement the Last Planner Method?
- Traditional vs Digital Last Planner System Project Management
- Takeaway
In the construction world, the line between ambitious vision and practical reality is easily blurred, leading to massive challenges—and sometimes monumental failures.
We’ve all seen it and know it too well.
Consider the infamous 1990’s "Big Dig," Boston’s Central Artery/Tunnel Project. First imagined in the 1970s to ease congestion, this ambitious project spiraled into a logistical nightmare riddled with poor oversight, mission creep, and slippery accountability.
The result was a 10-year delay in project completion and final costs more than 686% over budget—from $2.8 billion to over $22 billion by 2007.[1]
A similarly horrifying tale is unfolding today with California's High-Speed Rail system, a visionary project intended to connect San Francisco to Los Angeles with high-speed train service.
Since its proposal in 2008, the project has been slogging through unexpected bureaucratic delays, legal challenges, and difficulties in land acquisitions, pushing its cost projections from $33 billion to over $100 billion with no clear end in sight.[2]
Traditional Project Management—a Common Feature in Failure
What do these examples and thousands of others like them have in common? Traditional project management.
The traditional approach carries essential flaws in handling the complexities of modern construction projects, which is precisely where the Last Planner System (LPS) steps in to save the day. LPS offers a structured but flexible approach that’s highly effective at avoiding these kinds of disasters.
Traditional project management imposes a rigid, top-down structure resulting in disconnects between planning and execution. LPS, on the other hand, introduces a collaborative, commitment-based planning system that keeps everyone connected. That’s the key.
By engaging every level of the team in the planning process, LPS naturally aligns your project's vision with its on-the-ground realities. You never have to sidestep the pitfalls of overruns and mismanagement because the pitfalls are never allowed to form.
By now, you might be thinking something like—
LPS sounds like a great plan, but how in the world do we do it?
The answer is simple: Just keep reading this guide.
We’ll examine the structured phases of LPS, its key principles, and how they enhance construction project execution and management. We’ll also discuss the modern shift toward digital LPS and show you how easy it has become to implement the LPS process in your workflow.
By the end, you’ll be chomping at the bit to get your team on board. So, let’s get started!
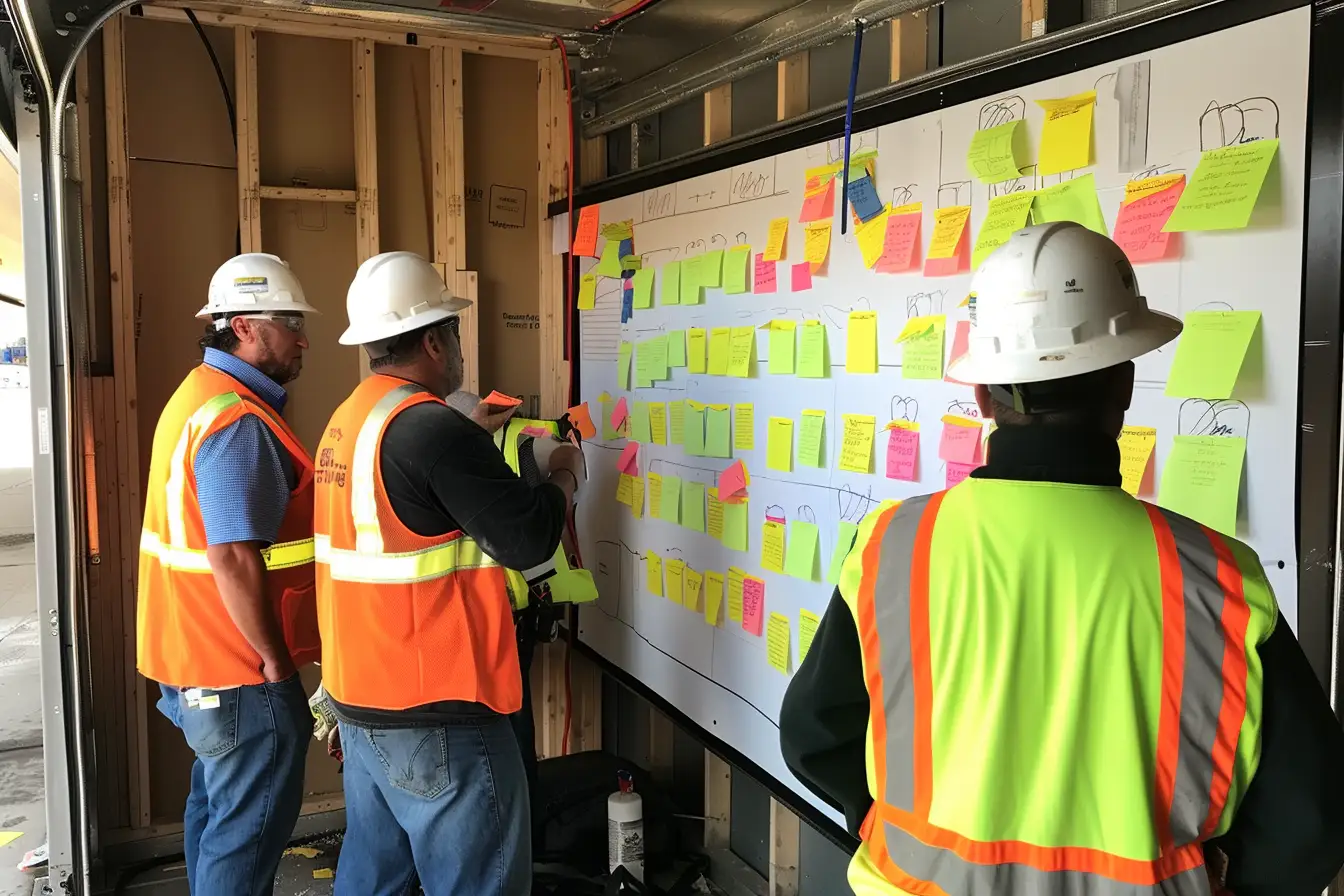
Last Planner System Definition: a Lean Construction planning process centered around collaboration among the last planners of a project.
In LPS, the “last planner” isn’t a single individual but rather a role or function within the construction management process. It refers to all of the team members directly responsible for supervising the workers who carry out the construction work.
Therefore, the last planners can be foremen, superintendents, or anyone else with direct authority over frontline workers. These people are the last link in the planning chain before the actual work happens. They’re crucial to making sure plans are feasible and commitments are fulfilled.
The Last Planner System (LPS) is structured around a series of distinct, interconnected phases that encourage detailed and dynamic project management in the construction sector.
Each of the four LPS phases—called Should, Can, Will, and Did—plays a role in transitioning from broad project strategies to specific, actionable plans that drive cost-effective project execution.
As a systematic approach, each stage is part of a planning cycle designed to enhance efficiency and accountability and enable continuous learning and improvement for the duration of the project.
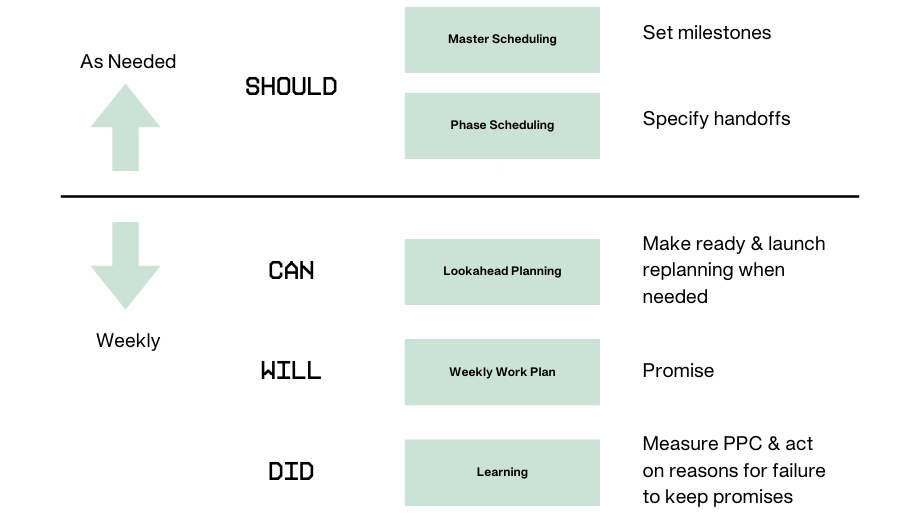
By understanding and implementing each of these phases, you—the construction professional— achieve three beautiful things:
⭐ More reliable project outcomes
⭐ Exponential profit growth
⭐ Exponentially faster productivity
To better understand the four LPS phases, start by imaging each one as part of a question:
What should we do?
What can we do?
What will we do?
What did we do?
Now, we’ll look at how these questions contribute to making LPS an uber-powerful tool for high-revenue construction management.
SHOULD (Master Scheduling and Phase Scheduling)
At the initial Should phase, you outline the project’s broad timeline—what it should look like. This high-level view, or master schedule, sets the stage for more detailed planning.
By establishing a master schedule based on phases, all stakeholders gain a clear overview of strategic milestones and the project’s guiding flow, guaranteeing alignment among stakeholders from the start.
McAlvain Companies Inc. provides a perfect Last Planner System construction example in action. They faced a recurring problem of supervisors managing their schedules using separate, disconnected methods, leading to major communication gaps and delays.
When McAlvain adopted LPS and its master scheduling component it encouraged seamless communication among stakeholders, restoring profitability by eliminating the inefficiencies and delays caused by fragmented scheduling.
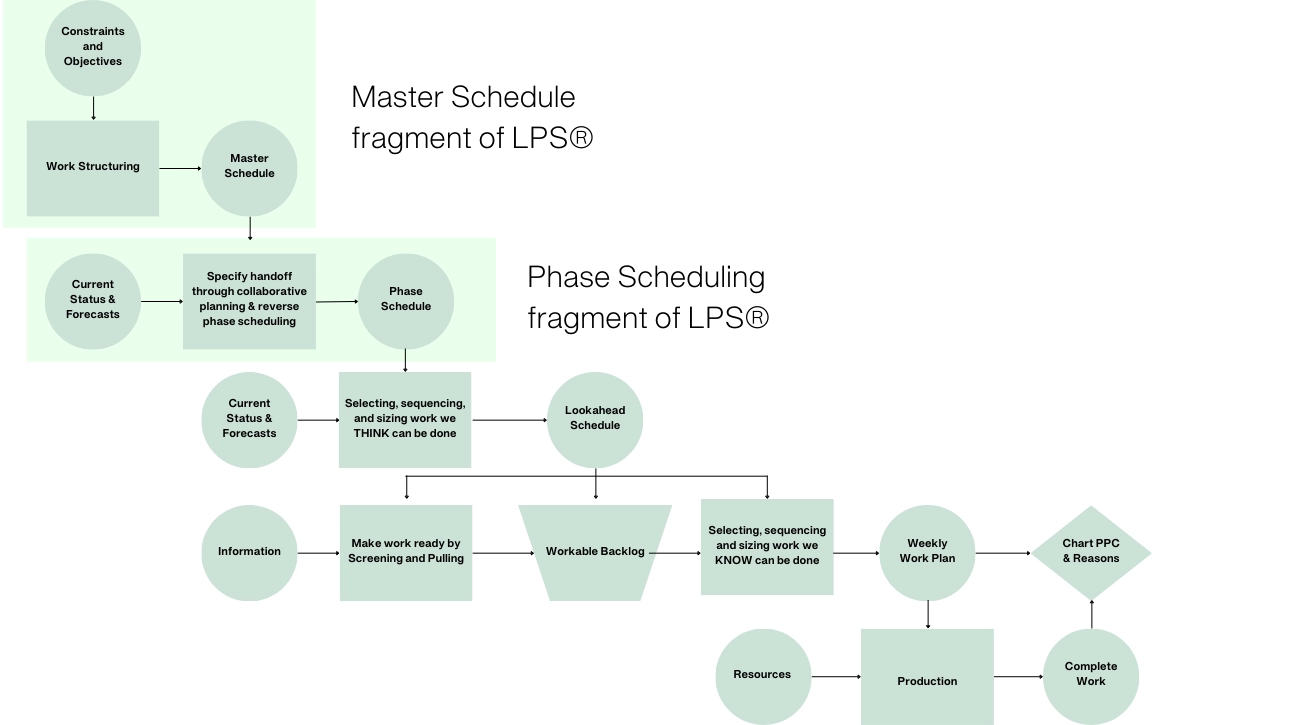
CAN (Lookahead Planning)
In the Can phase, you consider the resources you have and then plot out the possibilities—what the project can look like. This plotting, also called lookahead planning, involves detailed structuring of the next several (often six) weeks to:
- Identify goals the team can accomplish.
- Organize resources to meet those goals without disruptions.
Lookahead sessions are proactive bridges between the master schedule and short-term action steps. They give you space to make room for adjustments based on the analysis of current project realities and by forecasting potential constraints before they happen.
As mentioned earlier, LPS phases are distinct but interconnected. McAlvain’s master schedules provide a great illustration of this overlap.
For instance, the group determines project master schedules during the initial Should phase. Then, they hold lookahead meetings (determined in the Can phase). At those meetings, they touch base on the realities in the field to prevent delays and optimize resource allocation to support the master schedule.
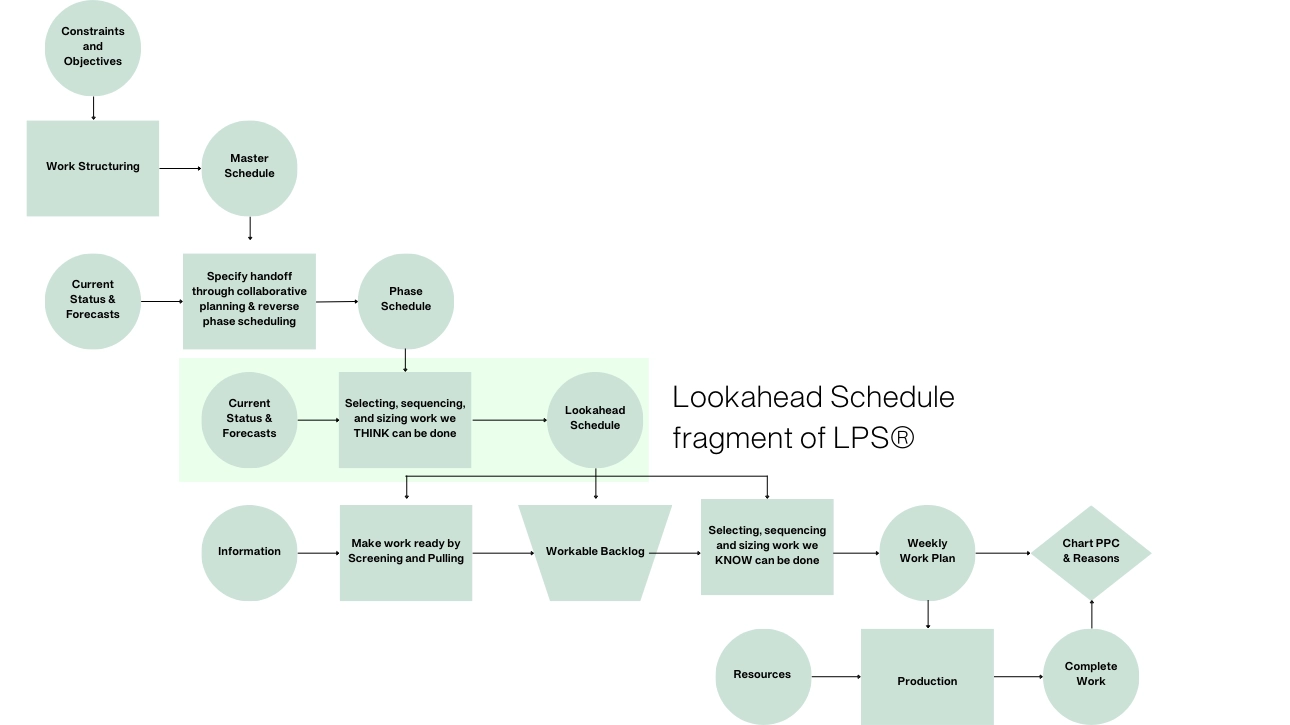
WILL (Weekly Work Planning)
During the Will phase, every individual’s commitments in each lookahead session are translated into a weekly action plan—what the crew will do. This is where you assign specific tasks and crew members make commitments.
At this granular planning level, each week is structured for smooth project progress because every person involved is clear on their immediate responsibilities.
Again, consider McAlvain’s process.
As we discussed, miscommunication was their greatest liability. With the adoption of LPS, team members began participating in weekly work planning, which is designed to enhance accountability and, in turn, maintain project momentum. The improved communication profoundly improved McAlvain’s upside potential.
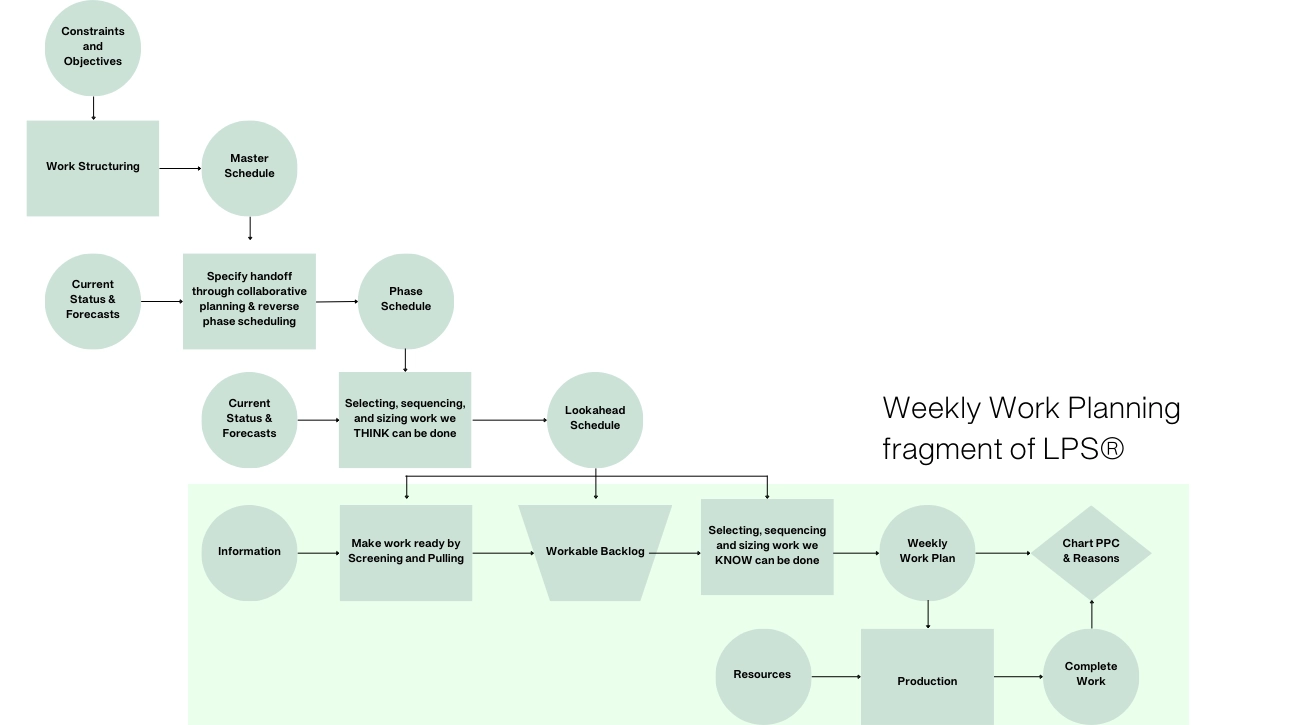
DID (Learning from Analytics)
Once your weekly plan is executed, you enter the stage in the project cycle where you can reflect on what the team did. In this phase, you reference project analytics to:
- Compare what happened with what was planned.
- Learn from the discrepancies.
- Apply lessons learned to future planning cycles.
The reflective phase is crucial for continuous improvement (discussed in greater depth below) because it allows for strategy and process adjustments to better meet future objectives.
In addition to the four phases, LPS is built on several foundational principles that support efficiency, reliability, and collaboration in construction project management.
Each principle addresses multiple aspects of project planning and execution, allowing you to create a responsive and repeatable approach that aligns with the dynamic needs of modern construction projects.
Following is an overview of the three most important of these key principles.
1. Pull Planning
With pull planning, you plan the work—or “pull it backward”—from a set milestone. Your approach is to focus on the end goals and then identify and schedule tasks to support each milestone.
Pull planning calls for the anticipation of needs and obstacles so that teams are prepared and can align resources before problems turn up. With this forward-thinking strategy, every step is purpose-driven and directly contributes to the project's objectives.
For example, Catamount Constructors demonstrates the successful use of the pull planning method. Recently, they adopted the latest planner scheduling and planning software, Outbuild, to manage logistics digitally, eliminating the need for whiteboards and sticky notes (more on this later). The transition to digital has supercharged Catamount Constructors already efficient workflow.
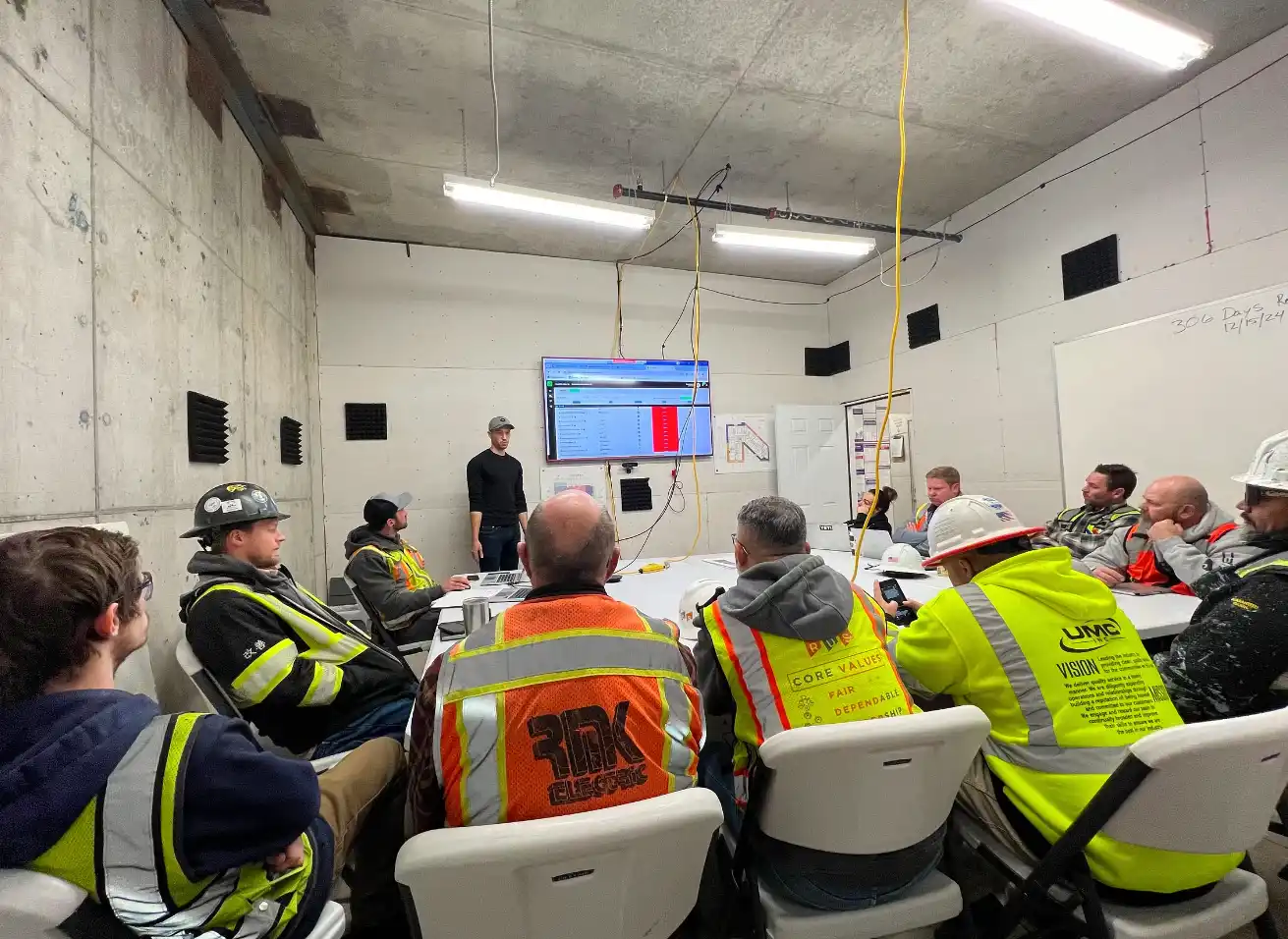
2. Commitment Management
Commitment management is at the heart of LPS methodology. According to the principle, each member commits to deliverables within a timeframe that they help to determine. It’s a crucial principle for fostering a sense of ownership and responsibility among the group.
Commitment management builds accountability and makes commitments realistic and attainable by allowing the crew to set their own timelines. As a collaborative approach, the system strengthens reliability and empowers individuals, leading to consistent outcomes and more profitable projects.
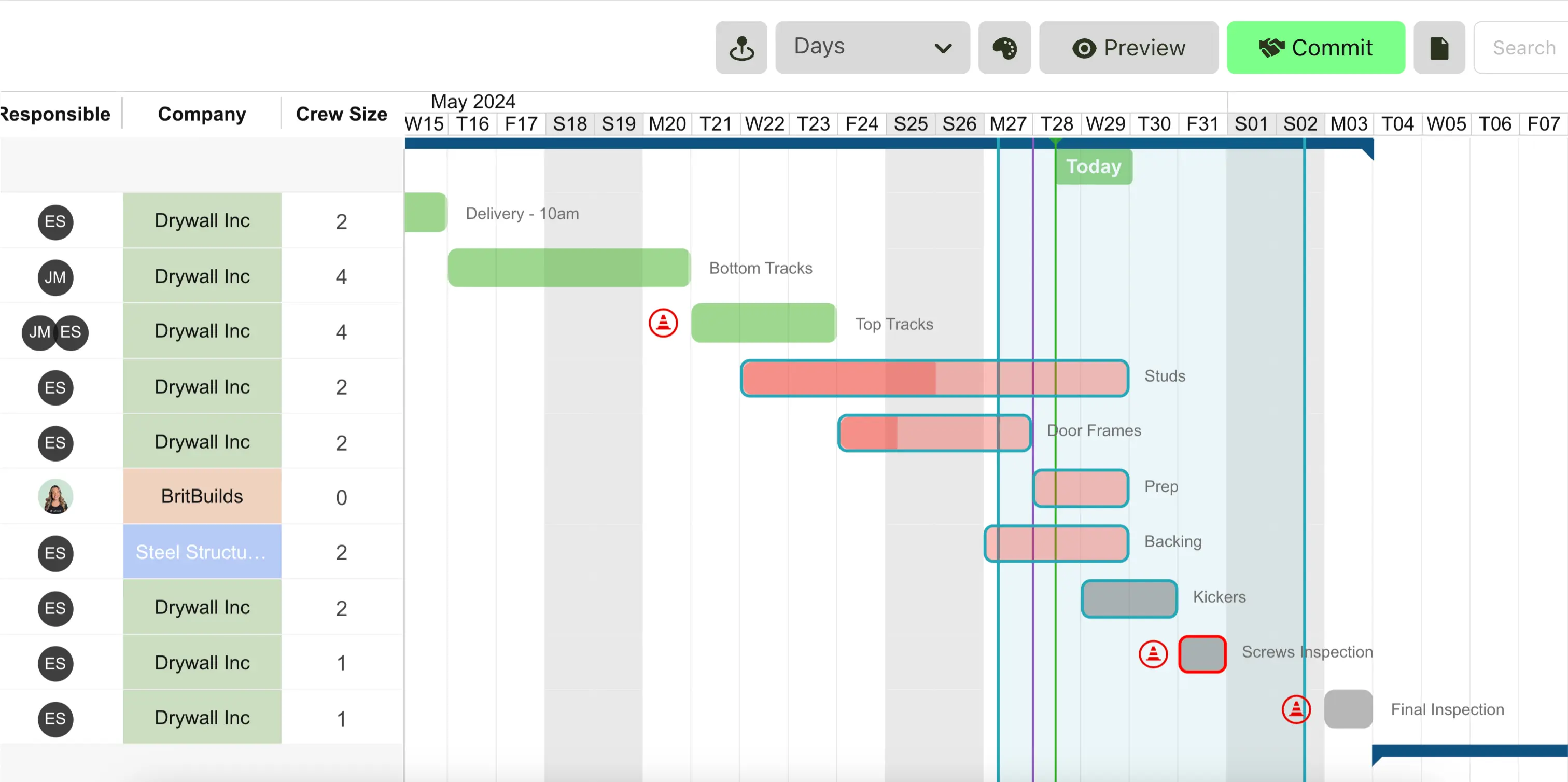
3. Continuous Improvement
Continuous improvement is a major principle in last planner lean construction, which establishes strategies dedicated to the ongoing refinement of processes and outcomes.
During regular reflection and learning sessions, everyone reviews what’s working and what isn’t. In addition to driving ongoing refinement, the sessions are designed to establish a culture of learning and adaptation.
By constantly refining their methods and strategies through continuous improvement, construction teams stay adaptive and responsive to changing project needs and challenges. As a result, crews are proud of what they do and deliver better results.
Granger Construction has been successfully implementing continuous improvement principles within the construction industry for years. Using a systematic continuous improvement strategy called the "Plan-Do-Check-Act" (PDCA) cycle, they identify opportunities for improvement, implement changes, and evaluate the results.
This approach has developed high morale among employees and a culture of learning and adaptation. As a result, Granger consistently meets project milestones under budget and ahead of schedule.
Each of the four LPS principles is important in implementing the Last Planner System, creating a solid framework that supports effective and economical project management in the construction industry.
The answer is a resounding YES!
Any construction organization looking to maximize profits and build morale can (and should) adopt LPS methodology. Once you make the decision to move forward, it just involves a structured but flexible and simple approach:
- Stakeholder Buy-in: Gain the commitment of all project stakeholders to support a collaborative approach.
- Training and Education: Educate everyone on the principles and processes of LPS methodology.
- Tool Integration: Find the right tools for easy scheduling, communication, and documentation.
Overcoming Common Challenges
Implementing LPS isn't without challenges. In construction, the greatest obstacles usually revolve around resistance to change and the complexity of coordinating multiple crews.
However, the following common-sense strategies are highly effective for overcoming resistance:
- Do Comprehensive Training: Make sure everyone understands the benefits and operations of LPS methods.
- Implement Incrementally: Start small with pilot projects to demonstrate the benefits of the approach and build momentum for wider adoption.
- Take a Digital Approach: Use modern tools that streamline collaboration and documentation, and be sure to demonstrate how these tools reduce the learning curve and minimize confusion.
Whether you go the traditional or digital route is a decision you’ll have to make once you’ve opted in. As is evident above, we recommend the digital approach, so let’s look at why.
2 Solutions for Last Planner System Implementation in Construction
Traditionally, the LPS method incorporates hands-on and visual tools. However, advances in technology have enabled us to create the Outbuild last planner software as a digital solution with new efficiencies and capabilities.
Still, whether you decide to go digital or traditional really depends on your needs, resources, and project demands. So, we’ll briefly discuss the differences to help you determine which approach would be best for your needs.
Traditional LPS Implementation
The traditional LPS approach primarily uses physical whiteboards, dry-erase pens, and sticky notes to take the project through the Should, Can, Will, and Did planning cycle.
Everyone gathers around these large boards where the project’s timeline and tasks are visually mapped out with a combination of lines and colored sticky notes. Each color represents a different activity type or project phase, and the notes can be moved and rearranged as the project progresses.
The traditional LPS method is a hands-on approach that gives everyone a big-picture view of the project lifecycle. It provides a forum for daily and weekly planning sessions, during which all participants can physically and directly engage with the plan.
Outbuild’s Digital LPS Implementation
Where the traditional approach relies on physical elements, the digital LPS approach relies on specialized software to take projects through the Should, Can, Will, and Did planning cycle virtually.
The LPS scheduling and planning components and key principles are baked into the platform’s various functions—from master schedules and pull planning to lookaheads, weekly work planning, and analytics.
So, the physical aspects of the LPS process are simply transferred into an organized, virtual environment. All the information and elements are there—the only difference is they’re digitized.
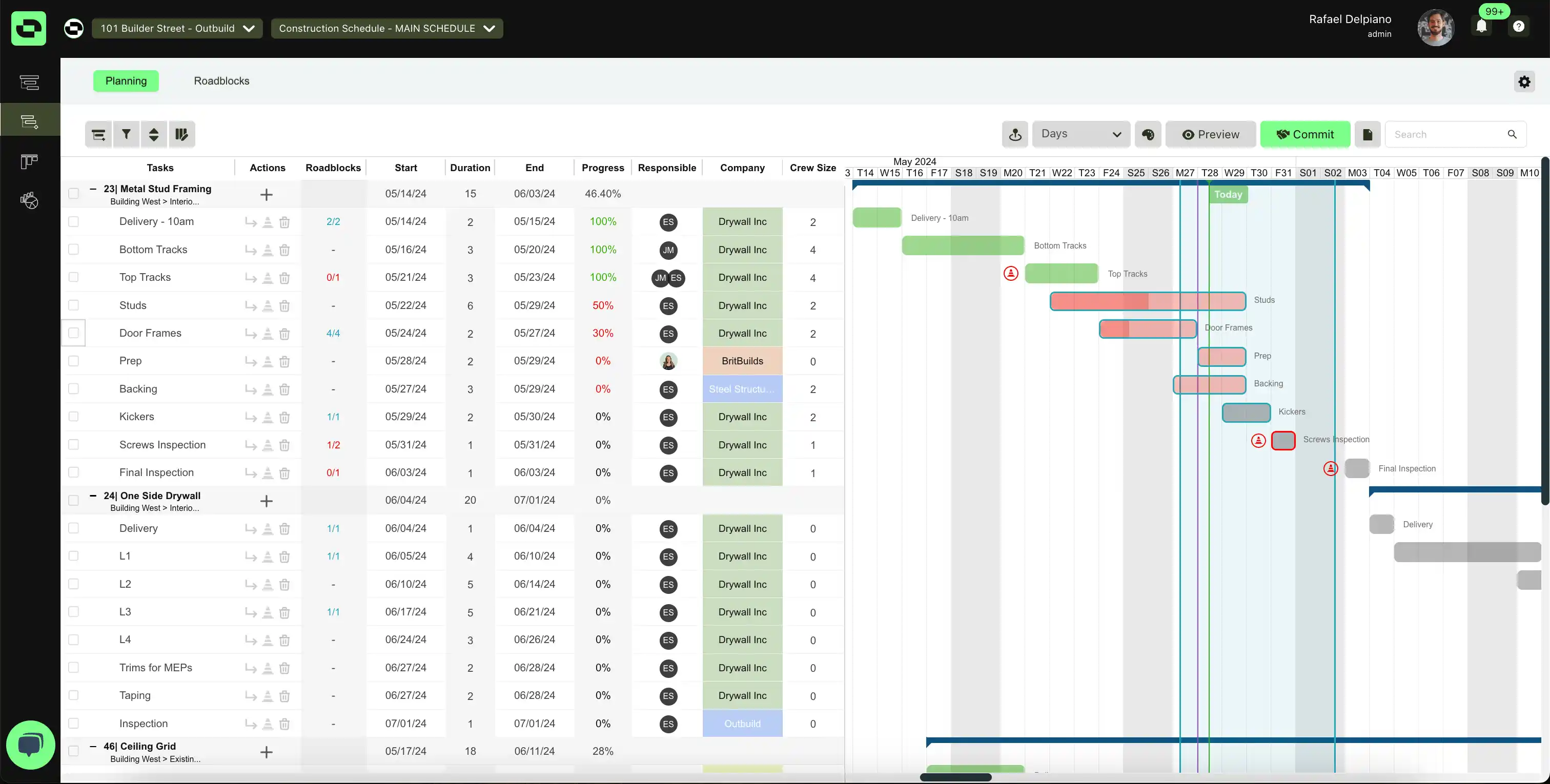
If you begin with the traditional approach and transition to digital, you'll notice that several significant advantages become obvious.
The ability to progress digitally through the Should, Can, Will, and Did planning cycle transforms your project management's efficiency, accuracy, and scalability, catering to the dynamic needs of modern construction.
Efficiency
The digital approach streamlines the scheduling and monitoring processes integral to every last planner technique by significantly reducing the time normally spent on manual updates.
For a digital Last Planner System example scenario, imagine a project manager who’s required to regularly update the schedule for a large-scale development project.
With a digital system, the manager’s changes are automatically posted and available to the organization in real-time. An update that might’ve taken hours to communicate across various teams took mere minutes.
Accuracy
Because real-time updates make data widely available to stakeholders automatically, the errors typically associated with manual inputs are eliminated. Communication and collaboration thrive across the board.
The digital format also has a "snapshot-ability" and historical data preservation function that traditional formats don’t. That is, stakeholders can grab project snapshots at any stage without the risk of data loss.
There are no whiteboards to accidentally erase or sticky notes to fall off and out the door with the breeze.
For instance, consider a complex construction project with frequent scope changes. With the digital LPS approach, you can instantly record these changes, ensuring that each person involved has access to current, error-free data.
There’s no outdated data or the costly mistakes it often causes.
Scalability
Growth potential is another major advantage to the digital last planner process. The traditional approach is easily overwhelmed by increasing complexity and project size, while Outbuild adapts and scales easily.
Again, take California’s multi-phase, multi-year High-Speed Rail project. The digital LPS approach could easily manage its escalating data volumes and complex interactions between numerous project phases and stakeholders without compromising performance or usability.
And, with historical data availability, it could do so seamlessly across space and time.
Adopting the Last Planner System can dramatically improve construction management at its core. It represents a transformative approach focused on collaboration, reliability, and continuous improvement that delivers:
- Increased Efficiency: By ensuring tasks are ready before they begin, the Last Planner System reduces delays and maximizes resource use.
- Improved Communication: Regular and structured meetings equal better communication and collaboration.
- Higher Quality Outcomes: More reliable scheduling leads to projects being completed on time and within budget, enhancing overall quality.
Fortunately, the toughest part of implementation is drumming up company-wide commitment. We say this is “fortunate” because most modern construction crews have toughness and commitment in droves.
So, get started revolutionizing your construction management practices with the Last Planner System. Dive deep into this transformative methodology and get ready to see your projects and your profits skyrocket.
Frequently Asked Questions
Related Articles
Ready to see Outbuild?
Join hundreds of contractors from 10+ countries that are saving money by scheduling better