Outbuild is online scheduling software to work together on connected project schedules and look-aheads, enabling everyone to move faster.
Key Takeaways
There isn’t an industry around that wouldn’t benefit from improved productivity. The difference between construction and other sectors, however, is that construction desperately needs productivity improvement just to catch up with the rest of the world’s leading industries.
Unfortunately, the construction industry is slower to receive and implement technology. Other industries have been improving productivity by implementing new principles, software programs, and equipment for years.
Construction isn’t keeping up.
But things aren’t too far gone to get better. In this guide, we’ll discuss the challenges the industry faces as well as answer how to improve construction productivity problems with 6 key strategies.
Table of Contents
- Understanding the Current State of Construction Productivity
- 1. Identifying Key Challenges and Bottlenecks in the Construction Process
- 2. The Benefits of Effective Scheduling and Planning in Construction Projects
- 3. Streamlining Communication and Collaboration Among Construction Teams
- 4. Leveraging Technology and Innovation to Boost Construction Efficiency
- 5. Enhancing Workforce Skills and Training to Drive Productivity Gains
- 6. Implementing Lean Construction Principles for Enhanced Productivity
- Make Productivity a Focus in 2025
Construction productivity should be a chief concern for all businesses in the industry. How much a company can achieve within a given time frame will typically have a direct correlation with how much profit that company can make. But currently, the industry isn’t as productive as it should be.
Before we look at the 6 strategies on how to improve productivity in the construction industry, let’s consider the current state. A McKinsey report highlighted that construction, as an industry, has averaged only 1% growth over the past 20 years. Meanwhile, the total world economy has grown by 2.8%, and manufacturing (one of the industries most closely compared to construction) has grown by 3.6%.
Continuing on this path will only lead to further regression. Clearly, the industry needs to take a serious look at its production practices and how they can improve. In fact, if the industry could match the world economy standard of 2.8%, some experts believe it would increase the total construction spending by $1.6 trillion.
It’s not sufficient to simply state that construction firms need to be more productive. To do so, we have to take a look at the issues that the industry faces so we can identify where things go wrong. The following are some of the key challenges and bottlenecks that construction projects have to manage, which ultimately slow productivity.
- Supply chain management issues: Obtaining materials during times of supply chain disruption can feel impossible. When manufacturers struggle to get the raw materials they need to produce their products, load them onto shipping vehicles, and get them on their dealers’ shelves, contractors struggle and productivity levels drop.
- Materials ordering: Building materials management isn’t just a supply chain challenge. Keeping up to date with the amount of construction materials the job site needs can slip by the wayside. When the crew runs out of materials, the job stalls and productivity plummets.
- Workforce experience: Finding experienced construction workers who want to work in the industry is becoming more and more difficult. As of early February 2025, a news release from Associated Builders and Contractors stated that the workforce gap has topped 500,000.
- Safety and injuries: Construction is an inherently dangerous industry. When employees get hurt, the crew runs short, making it harder to get more done with fewer people.
- Weather: Managing weather is always a challenge. A day or two of storms could set the project back the number of days the storm took place plus additional days to restore the job site back to working order. The result, naturally, is wasted time.
- Management: Management teams know what they’re doing, but they often struggle to communicate and convey that information to those working for them. This creates a significant communication gap and prevents everyone from being on the same page.
- Ownership: Owners can be challenging in their own right. They can hold up a construction project while they make a decision, push for an unrealistic goal, or argue over contracts. These folks don’t always have construction experience, often making them difficult to work for and slowing productivity.
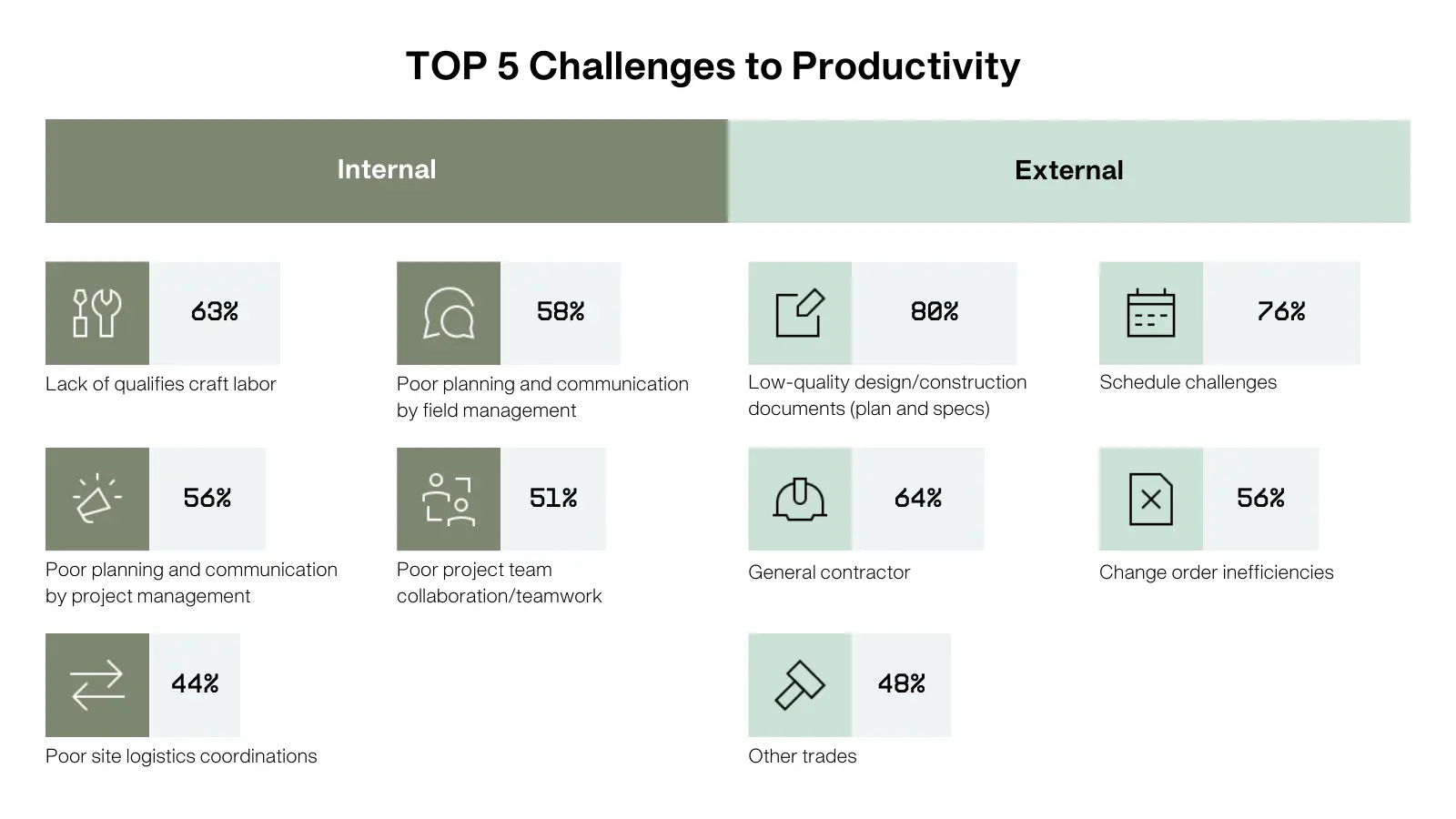
Effective scheduling is one of the most critical answers for how to improve productivity on a construction site. The project schedule is quite literally the roadmap that takes the project to completion. Having a dialed-but-flexible schedule allows projects to absorb delays as best as possible with minimal impact on the overall timeline.
First, let’s take into account the natural progression of a project. Obviously, certain stages have to be completed before further work can be completed. Having a software program like Outbuild that can list and link activities into an easily understood schedule allows project management staff to identify areas for improving productivity and use Critical Path scheduling.
Next, let’s consider delays. With legacy scheduling tools, the user has to shift schedules carefully, making sure every affected task is adjusted. This is tedious work and highly prone to error. Miss one or two tasks and productivity plummets.
With advanced construction scheduling software like Outbuild, project managers can easily shift the schedule by inputting the delay and attributing it to a task. If the delay then impacts other stages related to that task, the scheduling software will accurately shift the timeline. This won’t do anything to avoid the original delay, but it does allow the crew to be as productive as possible while they’re on-site with less time wasted.
Furthermore, the integration of look-ahead planning into the project scheduling process is instrumental in elevating productivity levels. Conducted in short bursts of three to six weeks, look-ahead planning allows for a detailed assessment of upcoming resource needs, including materials, labor, and equipment.
This proactive approach ensures that all necessary components are in place before they are required, thereby reducing idle time and minimizing the risk of project stalls due to unforeseen resource shortages. By aligning project teams with future needs, look-ahead planning acts as a bridge between immediate tasks and long-term project goals, facilitating a seamless transition between project phases and maximizing on-site efficiency.

Poor communication often causes ripple effects across a construction project and wrecks productivity. Companies that don’t share information effectively find their projects delayed, their budgets overrun, and their profit margins destroyed. Office staff, project management, and job site staff need to be able to communicate challenges, delays, or changes in a timely manner to be as productive as possible.
Great communication and proper planning improves productivity in many ways. For one, it avoids mistakes and rework. If there are new drawings or information to work from, site crews need to have it. Second, if the management needs to pull resources from one job to another, project managers on both projects need to know so they can schedule accordingly. There are few things worse than expecting to have a critical piece of equipment only to find out it’s on another job.
One of the best ways to improve communication is to rely on construction management software. These programs allow employees to design custom workflows, share information quickly, and even work through issues together, looking at the same data in remote locations. Better yet, when this software is cloud-based, any changes made at any point in the project plan are instantly accessible from anywhere in the world, in real time.
Today’s world runs on data. Having as much accurate information as possible before making a critical decision leads to better results. Most construction players haven’t always kept an eye on data points and KPIs, but for those that have, studies show that using project management software and data analytics improves project predictability by 20% and reduce costs by 15%.
Using tech and data together has never been easier, thanks to the technological advancements we’ve seen with software, cloud-based documentation, and even AI. All of these tools make collecting, organizing, and reviewing data easier and faster—two things that significantly boost productivity.
Also, BIM software is becoming more important. Building information modeling software creates digital representations of construction projects, significantly improving the planning process and ultimately improving construction productivity. Owners can see their buildings in a virtual space, hastening approvals and changes. Designers can work with tighter tolerances, improving accuracy while also identifying potential conflicts. Finally, teams can develop better schedules based on the model.
Construction should harness other innovative technologies as well. Wearable tech such as AR improves reporting and plan comprehension. Robotics can lessen the taxing nature of construction, as can wearable exoskeletons that reduce fatigue and injuries and improve worker capabilities.
One of the best answers to the question of how to improve labor productivity in the construction industry is investing in workforce development. Making sure that team members receive the training they need to be more efficient will improve productivity tremendously. In fact, the National Bureau of Economic Research found that a 10% increase in workforce training translates to a 7% productivity boost. Extrapolate that 7% over time and a business can see significant gains in profitability.
Companies should develop detailed training protocols and programs with milestones that employees need to reach. This can be in terms of the tools and skills they need to do their jobs on-site or with the technology that the business runs on. Training will reduce errors, improve efficiency, empower employees, improve morale, and increase overall productivity.
Safety training is also critical for improving productivity. Research shows that 10% of construction employees experience an injury each year. This means time off from the job, reduced morale, and poor productivity.
In fact, research by the University of Warwick shows that happy workers are 12% more productive. This drives home the importance of keeping workers safe and morale up. Ensuring that employees know how to work safely in their particular trade as well as around the rest of the job site can significantly reduce injuries and lead to improved productivity.
Lean building practices are rooted in productivity and improvement. These principles allow construction companies to identify their customers’ exact needs, set realistic goals and create an efficient yet comprehensive method to deliver them.
Among other pillars, lean principles believe in collaboration, smart materials management, and waste reduction:
- All of the project participants on a project work together to develop a realistic schedule and plan.
- Focusing on Just-in-Time construction ordering ensures all of the necessary resources (people, materials, and equipment) are on-site exactly when needed, reducing downtime and underproduction.
- Reducing waste due to overproduction, waiting, unnecessary transportation of goods and equipment, excess inventory, and underutilized talent ensures projects run as productively as possible.
There are other aspects of Lean principles that increase effectiveness, but these are the three most important answers to the question of how to increase productivity in construction.
Regardless of how a company decides to improve its efficiency, the first step is making it a priority. The tips above will help companies utilize certain technologies, software programs, and principles to make it happen. It all starts with better planning and scheduling, and Outbuild will help reduce scheduling friction and improve accuracy—two great ways to improve productivity all around.
Frequently Asked Questions
Related Articles
Ready to see Outbuild?
Join hundreds of contractors from 10+ countries that are saving money by scheduling better