Outbuild is online scheduling software to work together on connected project schedules and look-aheads, enabling everyone to move faster.
Key Takeaways
Table of contents
- Understanding the Basics of Six Sigma in Construction
- Key Principles of Six Sigma Methodology
- Benefits of Implementing Six Sigma in Construction Projects
- Tools and Techniques for Six Sigma in the Construction Industry
- Overcoming Challenges in Adopting Six Sigma Practices
- Measuring Success: Metrics for Six Sigma in Construction
- Training and Certification for Six Sigma Professionals
- Integrating Lean Principles with Six Sigma for Optimal Results
Whether overbuying materials, problems with installations, or dealing with defective parts, we've all dealt with issues impacting our project's bottom line. A perfect project isn't possible, but there are major steps we can take to reduce defects and increase efficiency. That's where Six Sigma Construction comes in.
Six Sigma Construction is a data-driven methodology that gets its name from the Greek letter Sigma which represents one standard deviation from the norm (i.e. a bell curve). Six Sigma means that this process helps you create outputs that are within six standard deviations of the mean. To put it another way, let's say you bought a million screws for a large-scale project. With Six Sigma quality, only 3 to 4 of those million screws would be defective. Six Sigma means doing things as close to perfect as you can get.
Six Sigma construction is based on a few core concepts that make it possible to streamline and improve every aspect of a project.
First, Six Sigma construction embraces data-driven decision-making. It takes every aspect of the construction process and breaks it down into statistics so you can spot where there are problems and inefficiencies. Second, Six Sigma prioritizes customer satisfaction, which means you need a good way to get accurate data on how your customers feel about your services.
Third, it leans into continuous process improvement. Projects change, economics change, and the workforce changes. Because of that, the improvement process is ongoing because the changing environment means new problems are coming up all the time.
Finally, Six Sigma construction empowers employees to solve problems they see on the ground. It's not a rigid hierarchy but instead encourages employees to improve processes when they see a problem.
There is quite a bit of overlap between Sigma 6 construction and principles of lean Construction. We'll touch on how they work together later, but the main difference is that where Sigma Six is a step-by-step process to make construction as efficient as possible, lean construction is more a set of ideals.
Putting Six Sigma Construction into practice is a tall order. Thankfully, five key principles work together to build a functional methodology – a road map to implementing this data-driven approach.
Five steps: define, measure, analyze, improve, and control (DMAIC) make up the Six Sigma methodology. These principles can be tricky to visualize on a conceptual level so let's attach them to a hypothetical Six Sigma construction project example.
You've just gotten a contract for a commercial construction complex in a suburban area outside a growing city in the midwestern U.S. One large store with three other small shops connected in the same strip mall. Let's see how the application of Six Sigma in the construction industry applies to our construction project.
1. Define
In this first phase, you talk to your customers and figure out exactly what they want out of this strip mall. How do they want the square footage divided? What's the timeline? What sort of plumbing and electrical hookups do they need? What problems are they anticipating? In our in-depth conversations, we discovered that the grocery store needs a lot of electrical hookups for refrigeration and that the whole project is at an intersection plagued with terrible traffic during rush hour. That means that we're dealing with potential delays in material deliveries at certain times of day and we need extensive electrical work in the larger retailer.
2. Measure
Once we figure out what we're working on, we need to determine how to gather data that is measurable as the project goes on. That means we need to look for key performance indicators like delivery times, the cost of materials, and project scheduling. We can collect this data by tracking delivery times, monitoring project schedule adherence with construction software, and documenting reasons for delays and cost overruns. So, once our project's rolling along we find that rush hour is extending longer than we thought and there's a shortage of high-voltage electrical components we need for the grocery store.
3. Analyze
This is where we take the data we've collected and figure out the root causes of the problem. You can use tools like a Fishbone diagram to visualize the problems and potential solutions in the project. In our example, we see that our window to avoid rush hour is small, and our current electrical supplier is having supply chain issues. Possible solutions may include scheduling deliveries late at night and seeking out alternative sources for obscure electrical components.
4. Improve
This is where you start to see the benefits of Sigma Six construction. You take the action steps proposed in your analysis and start implementing them. So you schedule those deliveries for 3:00 a.m. to avoid rush hour. You scour the internet for vendors selling those obscure electrical components. Do those changes help? Answering that brings us to the final step.
5. Control
Here, you look at the changes you've just made and see if they are effective. That means you're going to be doing some monitoring of performance like you did in step three. If the changes are helping, you standardize the process and develop new standard operating procedures for obtaining components and delivery schedules on this project. Keep in mind that it's possible the changes didn't help. Maybe scheduling a delivery for 3:00 a.m. was so costly in paying personnel overtime that it made the time saved not worth it. That's why it's important to implement a feedback loop as part of this final step.
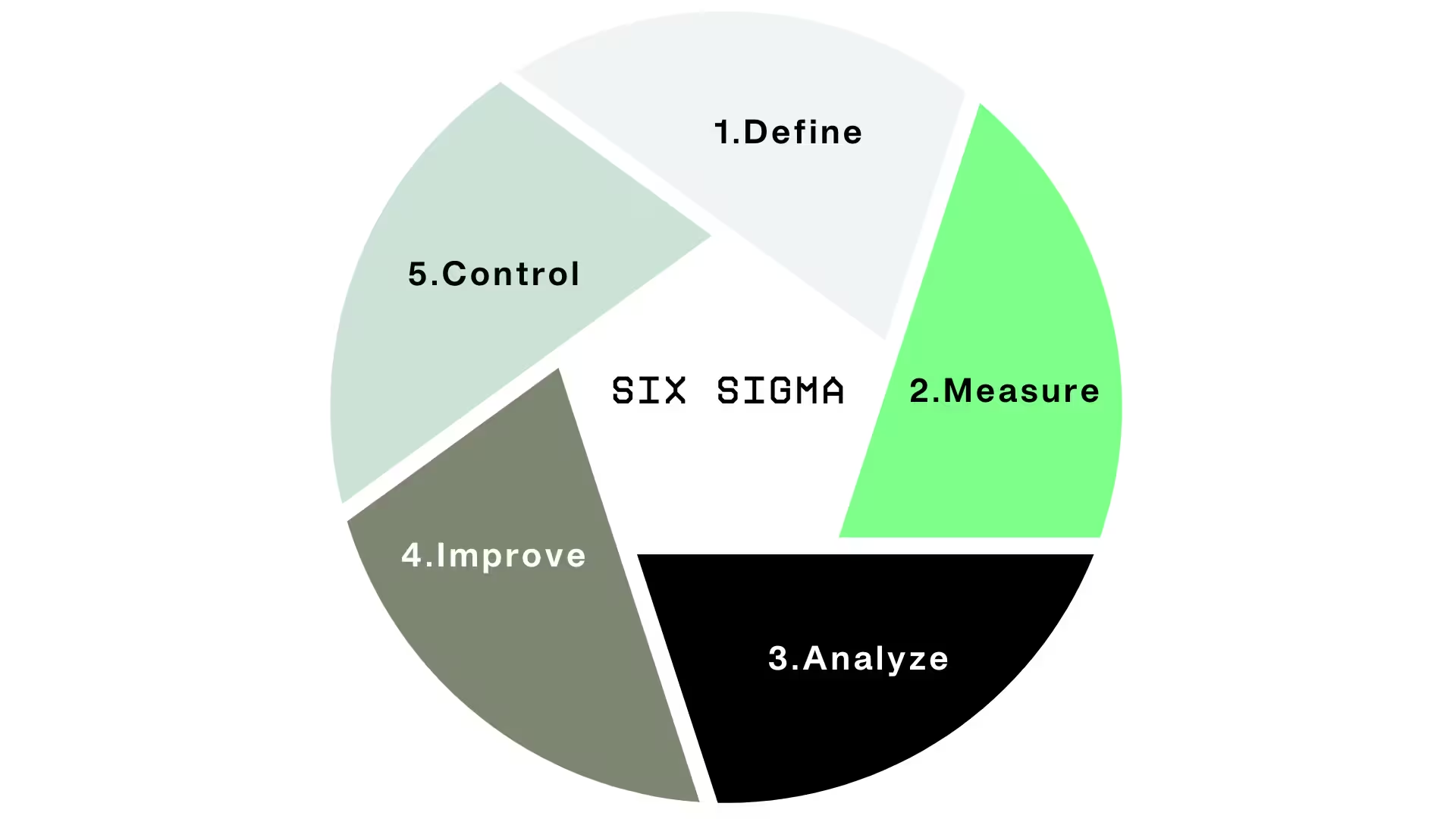
6 Sigma Construction improves almost every aspect of a project's implementation. Studies have shown that in a fairly short time, a project can expect to see cost reduction, service delivery time reduction, an increase in the volume of work performed, and a decrease in design cost.
Six Sigma’s feedback loop approach means you have multiple opportunities to catch mistakes which goes a long way in improving the quality of work. For example, if framers were using subpar lumber, if you miss that on the first pass through the analysis measuring step, you'd have many other opportunities to catch it. Along the same lines, you can expect enhanced safety in that you are more likely to catch hazardous practices earlier in the project.
Without accurate data, Six Sigma construction just won't work. That's why you need tools designed to plan and monitor your project's schedule and progress to collect top-quality data easily.
Then, once you break down the data you've collected, you need to visualize problems and prioritize solutions. Statistical tools like histograms, Pareto charts, box plots, and correlation analysis help you visualize data and identify trends and patterns. With this information, you can spot problems and start formulating solutions.
Integral techniques for implementing Six Sigma Construction include the DMAIC cycle that we've already talked about, along with tools like a Quality Function Deployment (QFD) that takes customers' needs and translates them into technical specifications for the project.
Six Sigma Construction represents a radical shift in how most construction companies do business. Like any major change, Six Sigma in the construction industry presents some significant challenges. Let's take a look at how we can deal with them.
Cultural Resistance to Change
Getting buy-in from your crew is essential in implementing Six Sigma construction. You can do this by communicating the benefits of this method and proving it by running a few small pilot projects to show how effective Six Sigma Construction is. Another hurdle is the lack of training and education, so it's essential to provide employees with ways to build their knowledge in this kind of construction.
Data Collection
Since successful Six Sigma construction relies entirely on accurate data, getting that data is a major challenge. Simplify the process as much as you can through user-friendly data collection tools and rely on data validation to ensure accurate information. You can also work to provide training to employees on how to use statistical analysis tools.
Making the Change Permanent
Even with successful Six Sigma implementation, there is often the temptation to fall back into old habits. That's why it's so important for crews to understand that Six Sigma is a methodology that applies to all your projects. You can encourage this by celebrating wins and recognizing the successful adoption of the process. Regular reviews also go a long way in assessing progress and seeing areas for improvement. Committed leadership is another integral part of making sure your company understands you're trying to make a permanent change.
There are two key metrics in measuring the success of Six Sigma projects: primary metrics and secondary metrics.
Primary metrics are the main focus of the project. So in our earlier example, that would be building the shopping center to the specifications of the customers and leaving them happy at the end of the project.
Secondary metrics on the other hand are important, but only so long as they don't interfere with the primary metric. So, for example, we might try to get building materials for the shopping center at a discounted cost so long as they are still high quality. If it jeopardizes customer satisfaction or getting the project done at all, then we ignore the secondary metrics in favor of the primary.
Six Sigma is a complicated process, so it's no surprise that companies look for experienced people to implement these processes. That's why multiple certification bodies provide training and certification in Six Sigma practices to maintain quality. Certification bodies include the American Society for Quality, the International Association for Six Sigma certification, and Six Sigma Online.
The certification levels adopt the language of martial arts training, categorizing training levels by belt rankings. A yellow belt signifies a basic understanding of Six Sigma Concepts and tools, a green belt means you can solve problems, and a black belt shows you have advanced knowledge of Six Sigma methodologies and can lead project changes. A master black belt means you are an expert and can successfully coach others.
Major areas of training include statistical tools and data collection, lean principles of construction, Six Sigma methodologies, project management, and leadership and communication skills.
Lean construction’s core principles of waste reduction, continuous improvement, and respect for people overlap a lot with Six Sigma Construction. This makes Lean Six Sigma in construction a natural progression of the methodology we’ve covered. Lean Sigma construction also means combining lean construction tools with the Six Sigma strategy – which usually leads to excellent results.
For example, look-ahead planning in lean construction can help you in the defining phase of Six Sigma by giving you a head start so you have measurement tools in place when the project begins. Depending on the issues you're having, just-in-time delivery presents a great solution during the improvement phase.
If you're ready to tackle Six Sigma Construction, step into the world of agile methodologies and discover how platforms like Outbuild can revolutionize your processes. Book a demo today or try Outbuild free for 14 days to experience the difference firsthand!
Frequently Asked Questions
Related Articles
Ready to see Outbuild?
Join hundreds of contractors from 10+ countries that are saving money by scheduling better