Outbuild is online scheduling software to work together on connected project schedules and look-aheads, enabling everyone to move faster.
Key Takeaways
Table of contents
- What is Construction Project Execution?
- What is Project Execution Plan in Construction?
- How to Execute a Construction Project Step-by-Step
- What’s Inside a Construction Project Execution Plan?
You’ve nailed the planning—now it’s go time. So how do you make sure your construction project actually runs smoothly? Construction project execution can be the make-or-break stage of your project.
In the exciting moment when crews start bringing the vision to life, how can you ensure your project goes smoothly? How do you keep the team on schedule? How do you make sure it is built with quality?
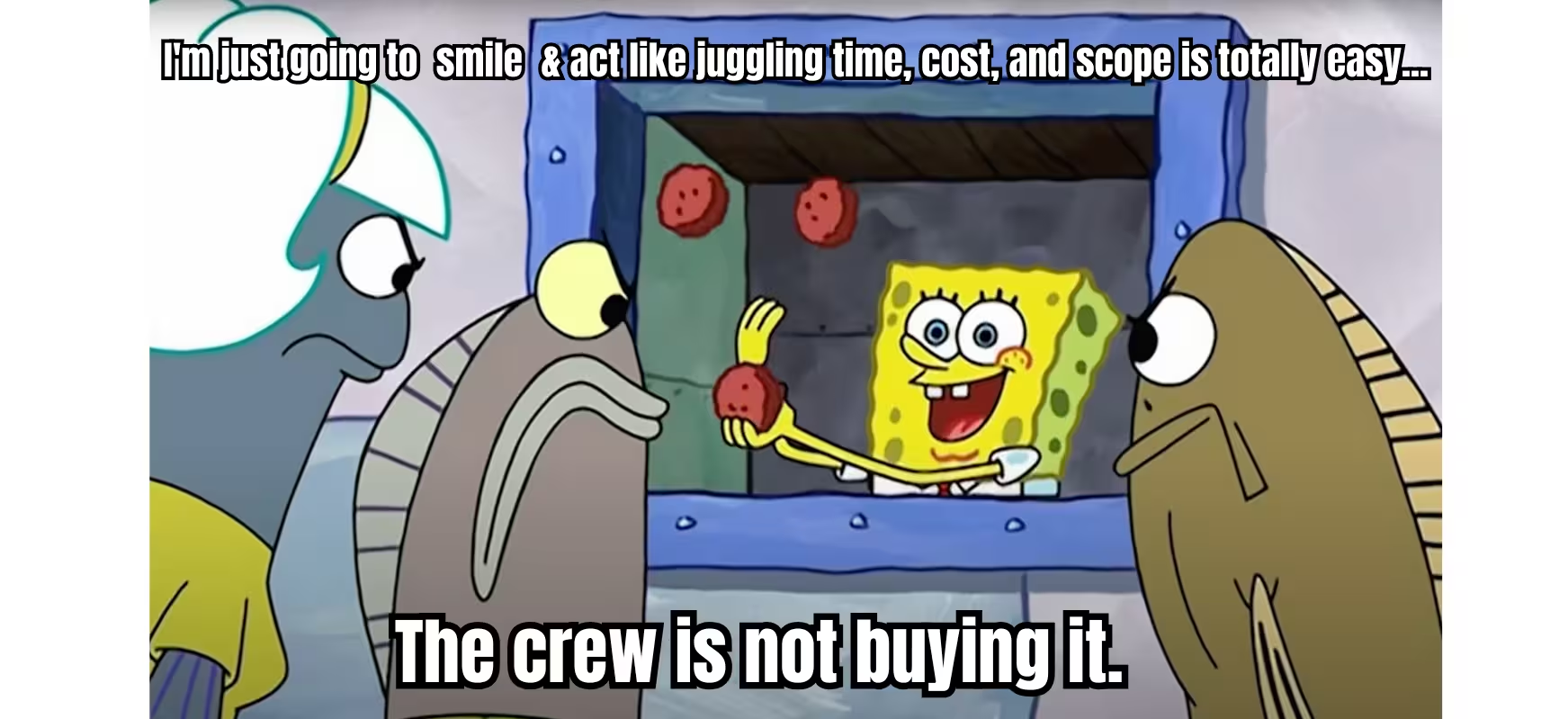
This guide unpacks everything you need to know about construction project execution.
Ok, so, what is project execution in construction? It is the boots-on-the-ground phase of your project.
Execution marks the transition from concept to reality in the construction Industry. It involves implementing approved project plans and designs, mobilizing resources, and managing on-site activities.
This phase connects your pre-construction work to project completion. It comes after the planning phase, feasibility studies, and initial cost estimates.
Turning Plans into a Physical Structure
During execution, every detail—from site preparation to roofing and landscaping—is set in motion. For example, coordinating specific tasks such as electrical and plumbing installations to ensure alignment with overall project goals.
The Most Critical Phase for Your Budget and Timeline
The execution phase is often the most resource-intensive and time-sensitive part of the project lifecycle. Errors, delays, or mismanagement here can escalate costs and drag timelines, impacting the overall success of your project.
This is because of the domino effect. A single delay, such as a late delivery of steel beams, doesn’t just push back the steel erection. It also delays the roofers and electricians. The electricians need to run conduit on the structure.
The masons are waiting to build the exterior walls. Each delay creates a ripple effect, pushing back subsequent tasks and extending the project timeline.
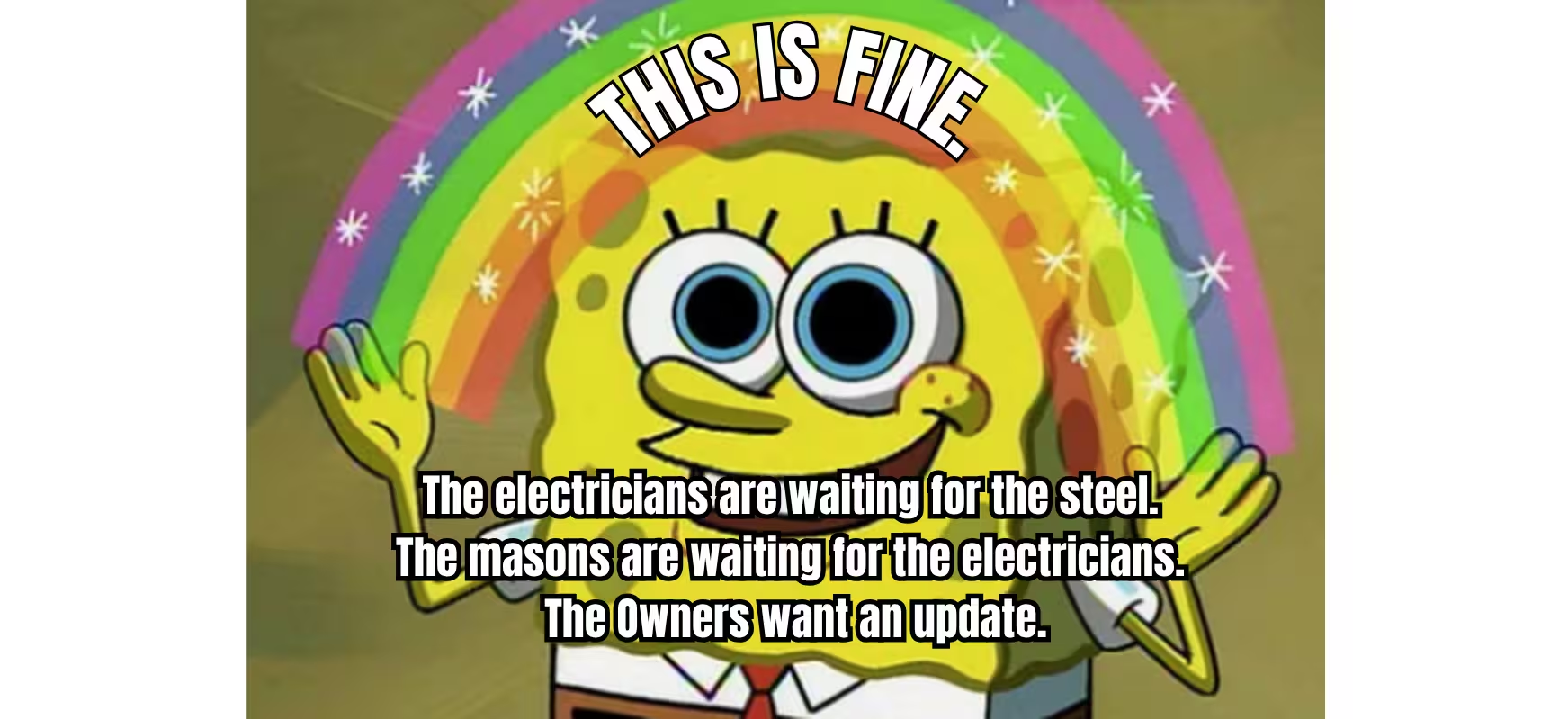
Furthermore, mistakes made during execution are expensive to fix. Tearing down a new wall because someone installed the plumbing in the wrong place wastes materials. It also wastes labor and time. This rework can shatter a budget and destroy a project schedule, making effective execution paramount.
So, what’s the Core of Success? Your Construction Project Execution Plan (PEP)
A Construction Project Execution Plan (PEP) outlines the tasks, timelines, roles, and resources necessary to turn designs into reality. Think of it as your guidebook that keeps your team aligned and your project on track.
More than just a static document, a well-drafted PEP is a living guide that evolves with the project. It promotes accountability by clearly stating who is responsible for each task. This removes confusion and lowers the risk of missing important tasks. When everyone on the team understands the plan, they can work more cohesively toward the same end goal.
Step 1: Mobilize Your Team and Resources
Assemble your complete workforce, confirm specialty contractors, and finalize material procurement. Make sure each team member knows their role, the project schedule, and important project deliverables for a strong start.
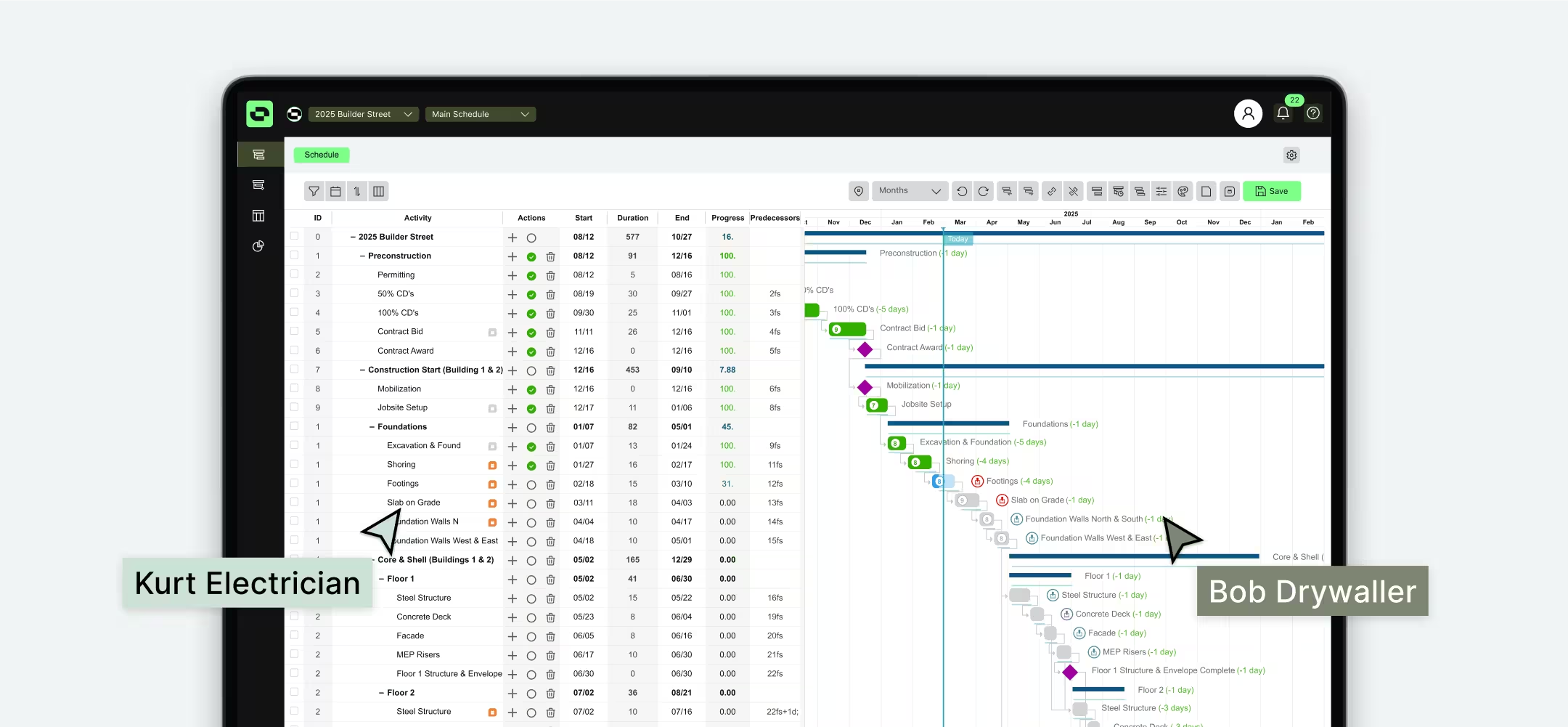
A formal pre-construction meeting often initiates this step. You will review the PEP, talk about the schedule, and set clear expectations. The team should also discuss material lead times.
For example, if custom windows have a 12-week lead time, you must order them far in advance to ensure they arrive when needed. Getting this step right helps to keep the project on track, long-term. This also sets expectations of being proactive for the project.
Step 2: Establish Site Logistics and Safety Protocols
Prepare the physical job site by setting up temporary amenities, access points, and storage areas. Create and share the safety plan for the site. Ensure that all staff receive training on the rules before starting work. Experts highly advise using software such as HammerTech to manage safety, people, and permits in real-time.
Safety isn't just a binder on a shelf; it is the most important element on a jobsite. Everyone's top priority is to make sure crews return home safely at the end of the day.
People conduct this in many ways, including daily safety briefings or "toolbox talks." Everyone must wear the personal protective equipment (PPE) before entering the site. (Bonus points if your team has inclusive PPE!)
A well-organized site ensures safety and efficiency and should include a site logistics plan that contains the following:
- where materials are kept
- where heavy equipment is
- how vehicles and workers will move on site
- location of trailer, restrooms, fence and designated break areas
- any regulatory information required by the local jurisdiction
- parking areas for crews
Step 3: Direct and Supervise On-Site Operations
Begin the physical construction activities according to the master schedule. Provide effective on-site supervision to coordinate tasks, manage subcontractors, and ensure daily operations align with the project goals.
The superintendent is the onsite leader. They are the main problem-solvers on the ground. They handle immediate issues and ensure that subcontractor teams work together. This helps them avoid competing for space or resources.
Among many tasks, they hold daily meetings to prepare the site for the work they will do. For example, they'll make sure that the area is clear for the concrete trucks to arrive and that the crew is ready to pour.
Step 4: Track Progress Against the Schedule
Monitor progress by comparing completed work against the project timeline. Use lookaheads plans and weekly plans to manage tasks. This helps you spot delays and keep the project on track.
This involves more than just checking boxes. It means understanding the critical path—the sequence of tasks that determines the project's total duration. Any delay on a critical path activity will delay the entire project.
Teams often use two- or three-week lookahead schedules to get a detailed, short-term view of what's coming. Lookaheads are most optimal when connected to the schedule.
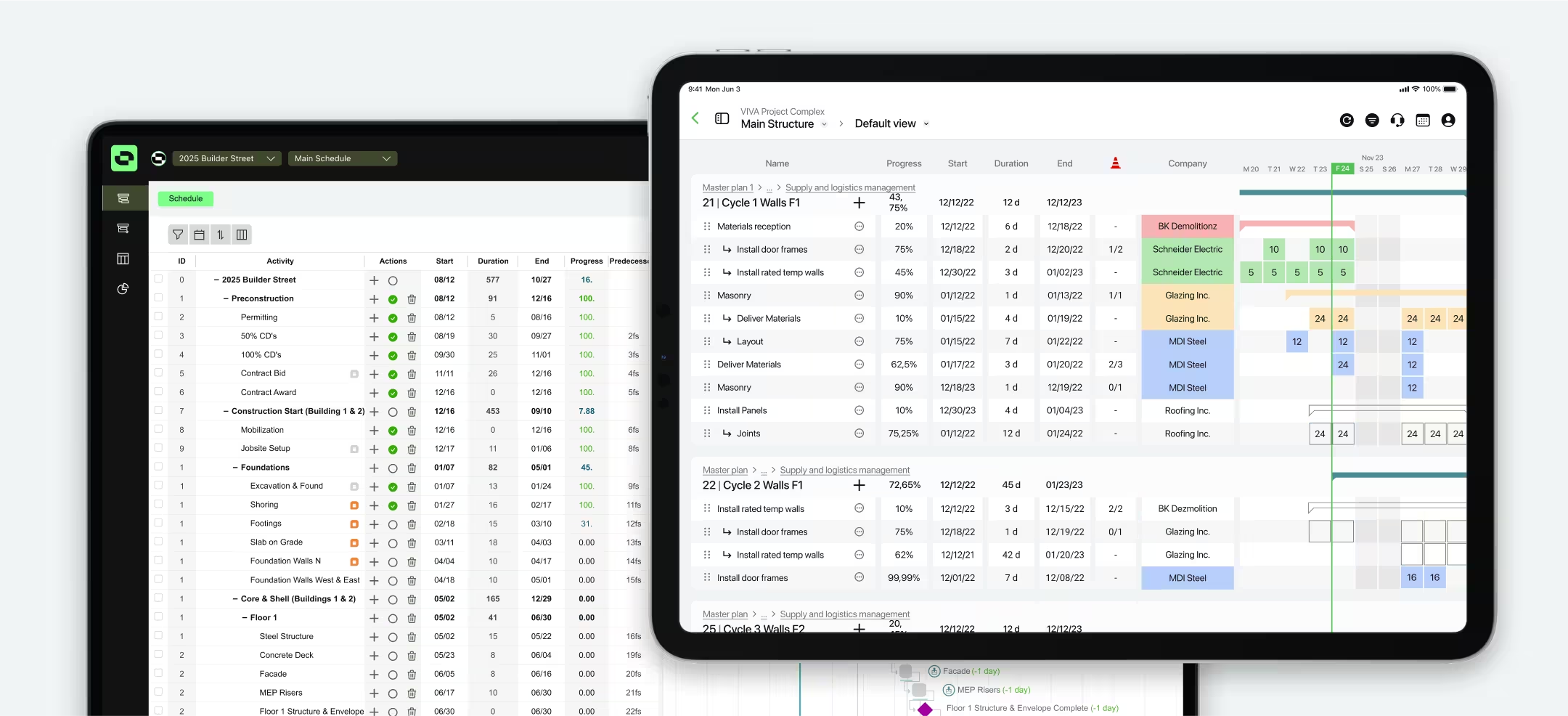
Step 5: Manage Budget and Material Procurement
Actively track all project expenses against the budget to prevent cost overruns. Oversee the procurement process by ordering, delivering, and storing materials efficiently to prevent shortages or work stoppages.
Effective budget management means assigning every dollar a job. Teams manage this by using cost codes to categorize expenses (e.g., concrete, labor, equipment rental).
As invoices and purchase orders come in, a team member codes and enters them into a tracking system. This lets the project manager see right away if they are over or under budget in any category.
Did you know that Outbuild simplifies budgeting by connecting cost tracking directly to project progress? Your team can log expenses and compare them to the budget. This gives you real-time financial visibility. It also helps you catch issues before they get worse.
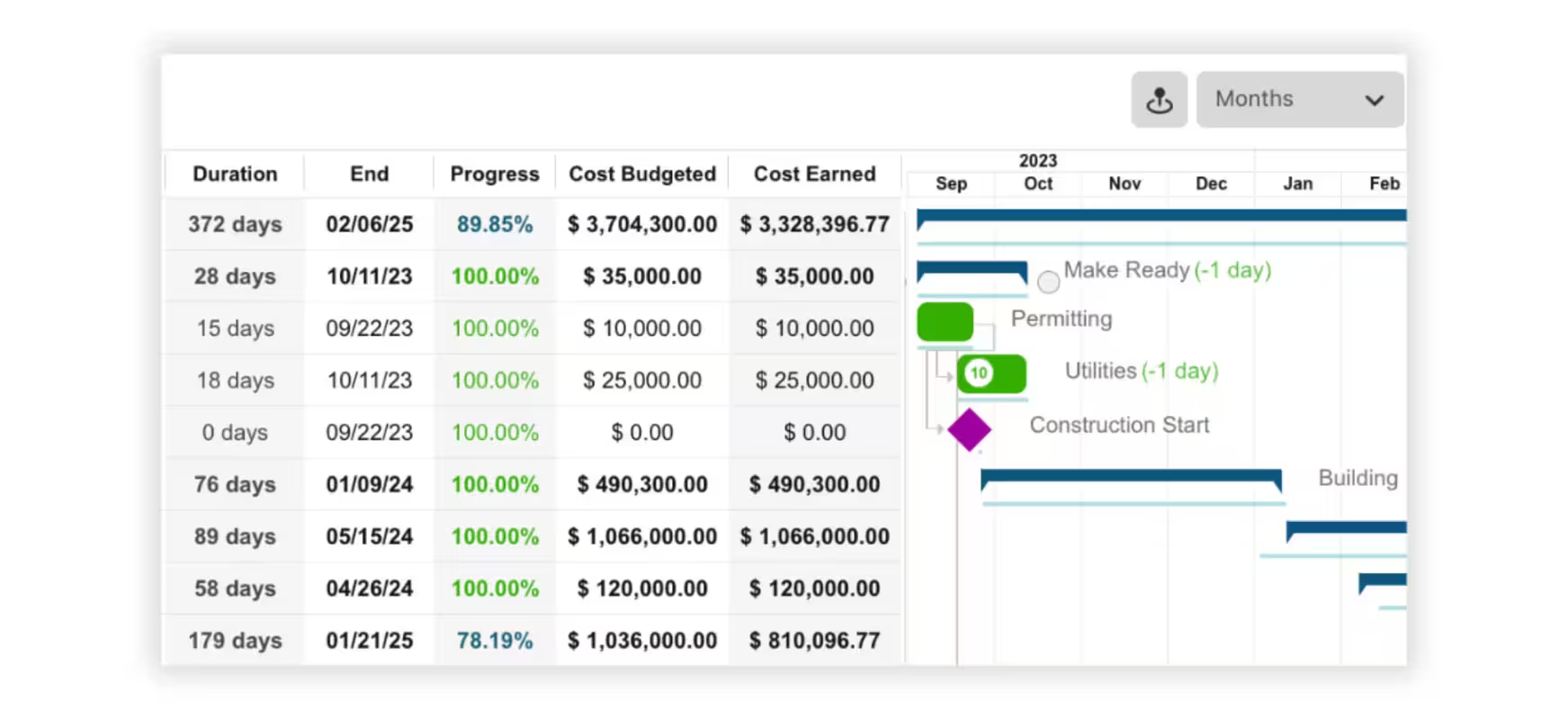
Step 6: Enforce Quality Control and Assurance
Conduct regular inspections and tests to verify that all work meets the specified quality standards and design requirements. Address any deficiencies promptly to maintain the integrity of the final structure.
Quality Assurance (QA) is about preventing defects, while Quality Control (QC) is about identifying them. QA involves processes like pre-qualifying subcontractors and using proven construction methods. QC is the hands-on inspection part.

Step 7: Maintain a Clear Communication Plan
Establish a consistent rhythm for project meetings and progress reports. Keep project stakeholders, including clients, designers, and internal teams, informed of milestones, challenges, and decisions to ensure alignment.
Communication flows in all directions. Regular owner-architect-contractor (OAC) meetings keep the client and design team updated. Weekly subcontractor meetings align all the trades working on site. Daily huddles address immediate needs.
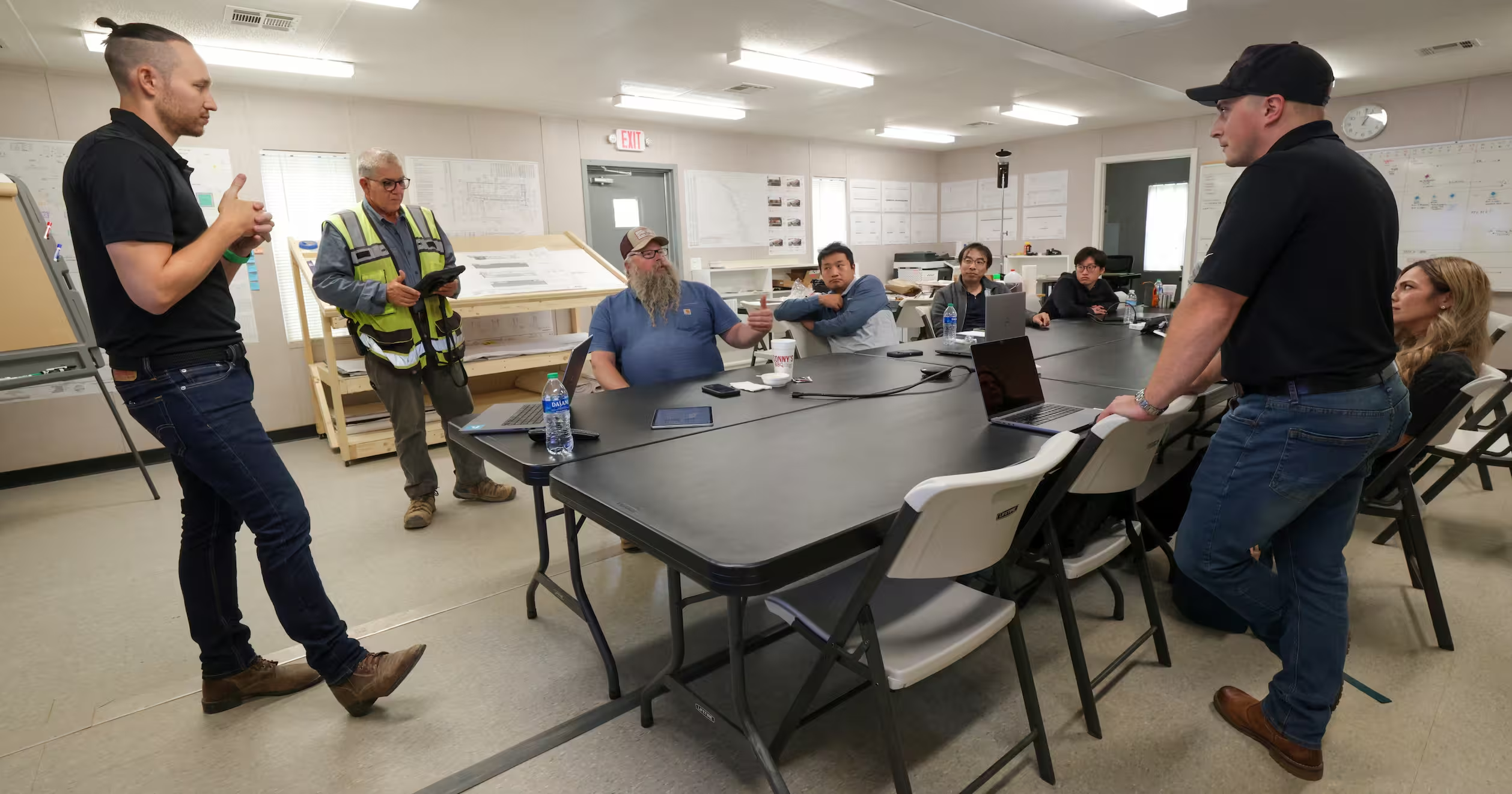
Step 8: Manage Comprehensive Project Documentation
Keep meticulous records of all project activities, including daily logs, meeting minutes, requests for information (RFIs), and financial transactions. Accurate documentation is crucial for accountability, dispute resolution, and future reference.
- A daily log is a diary of the project. It records the weather, the number of workers on site for each trade, the work performed, any issues that arose, etc.
- RFIs in construction are formal questions sent to the design team to clarify a drawing or specification.
- Submittals are documents that the contractor sends to the designer. They confirm that the team will use the right materials and equipment.
%2012.19.53%E2%80%AFp.m..png)
Step 9: Handle Change Orders and Solve Problems
Proactively identify and address unexpected issues and requests for changes. Create a clear process to evaluate, approve, and document change orders. This will help reduce their impact on the schedule and budget.
Change is inevitable in construction. The key is how you manage it. A formal change order process has several steps:
- First, identify the need for a change.
- Next, estimate the cost and time impact.
- Then, send the change proposal to the owner for approval.
- Once approved, create a formal change order document.
Step 10: Conduct Performance Reviews and Capture Lessons Learned
Regularly evaluate project performance for safety, cost, schedule, and quality. At the project's conclusion, compile a "lessons learned" report to improve processes for future projects.
This final step is an investment in the future. After the project is complete, the team should hold a lesson learned meeting. What went well that we should repeat? What went wrong, and why?
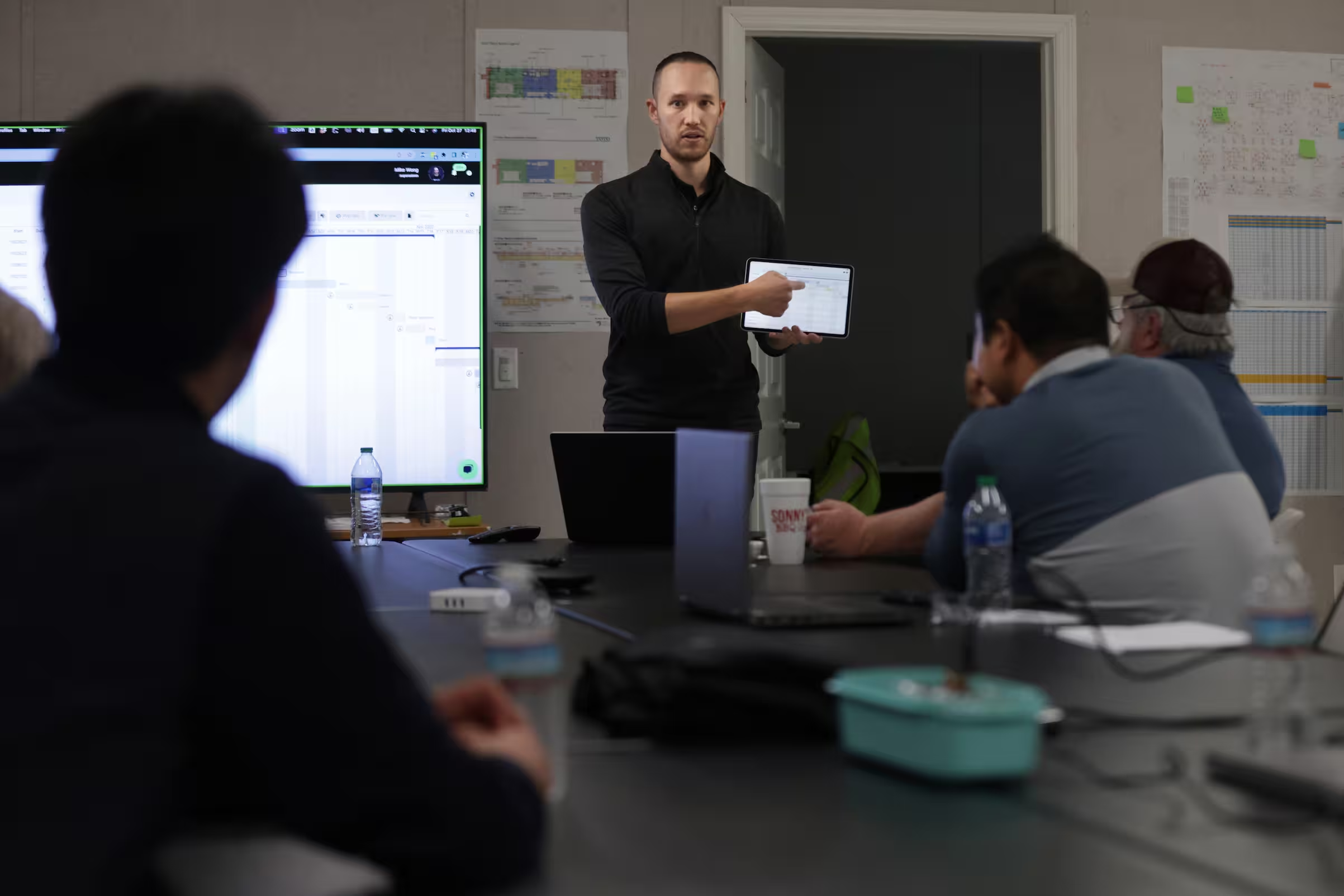
A well-crafted execution plan includes multiple components that act as the foundation of your project’s success.
Are you looking for a construction project execution plan sample? Or, need a construction project execution plan template? This outline covers the key areas.
Project Goals and Scope
Define the overall objectives and scope to set clear benchmarks for success.
Key Roles and Responsibilities
Assign roles like project managers, contractors, and subcontractors. For instance, a Construction Project Executive oversees the entire execution phase from a high level, ensuring alignment across stakeholders.
The construction project executive job description typically involves strategic oversight, financial control, and acting as the main point of contact for the client.
Master Schedule and Key Milestones
Use a detailed schedule to map out tasks, deadlines, and milestones critical to your project timeline. Tools like construction scheduling and planning software make this step seamless.
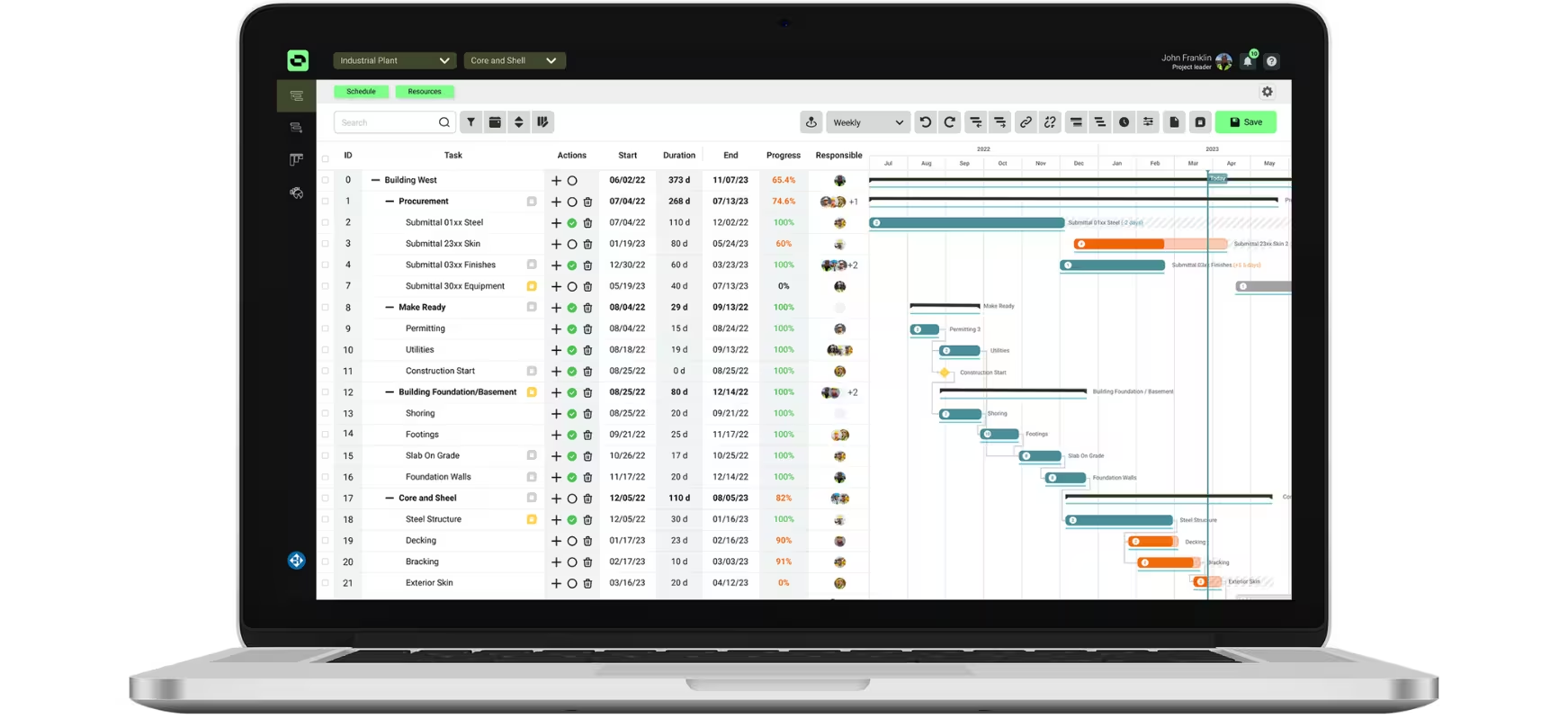
Budget and Cost Management
Outline all financial details to avoid cost overruns. This section should include contingencies for any unforeseen expenses for the project, including labor and materials.
Site Safety and Health Plan
Ensure all safety protocols and health guidelines are clearly documented and enforced.
Quality Control and Assurance
Define standards for quality and procedures for inspections and tests to meet these benchmarks.
Procurement and Materials Management
Track material orders, delivery timelines, and storage requirements, ensuring resources are always available without delay.
Your Next Step to Mastering Construction Execution
Successful project execution boils down to a well-prepared plan, precise management, and continuous monitoring. You can lower risks and achieve your project goals by using tools like construction scheduling and field coordination software.
For even more optimized project execution, explore how Outbuild’s solutions can transform your approach today. Book a demo or start your free trial today. See how Outbuild can help you crush your project execution goals.
Step 1: Mobilize Your Team and Resources
Assemble your complete workforce, confirm specialty contractors, and finalize material procurement. Make sure each team member knows their role, the project schedule, and important project deliverables for a strong start.
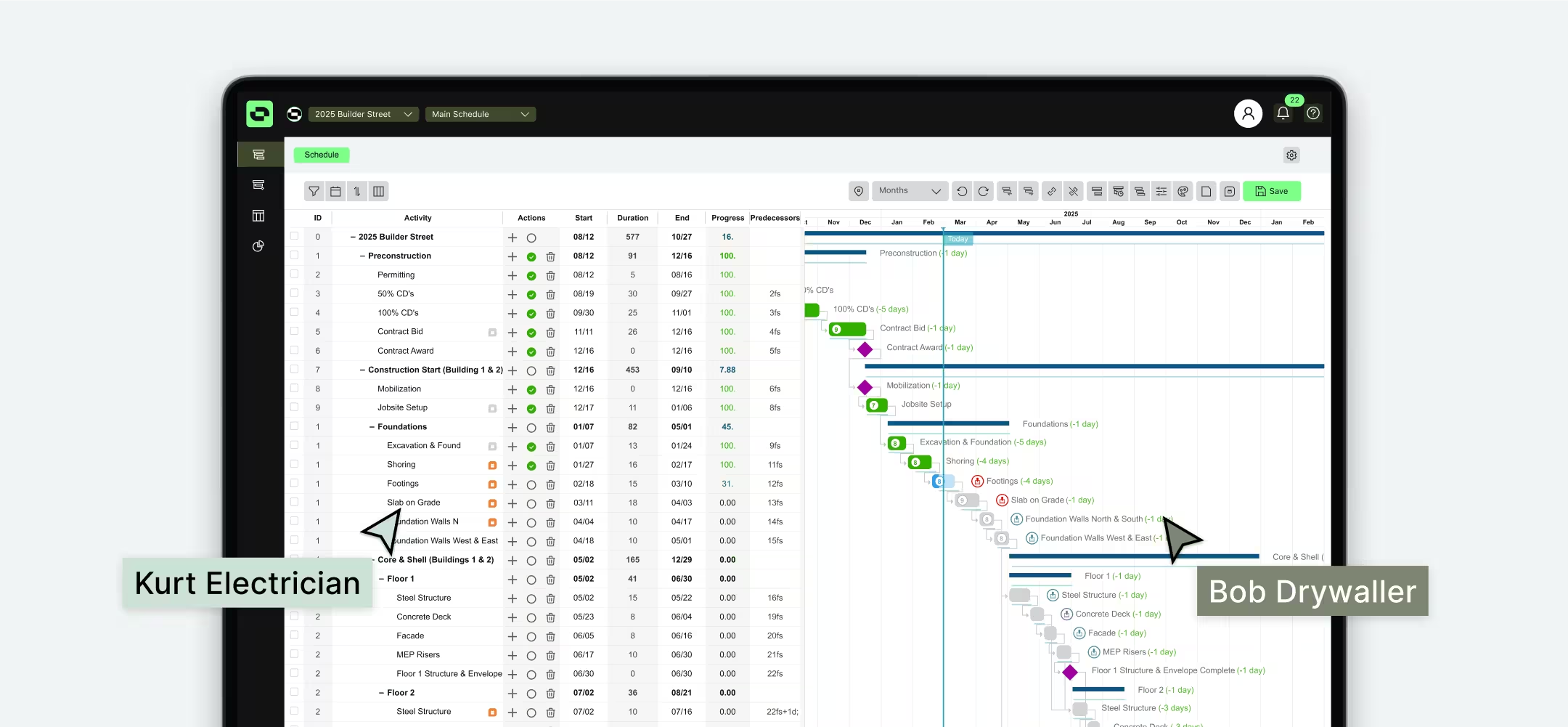
A formal pre-construction meeting often initiates this step. You will review the PEP, talk about the schedule, and set clear expectations. The team should also discuss material lead times.
For example, if custom windows have a 12-week lead time, you must order them far in advance to ensure they arrive when needed. Getting this step right helps to keep the project on track, long-term. This also sets expectations of being proactive for the project.
Step 2: Establish Site Logistics and Safety Protocols
Prepare the physical job site by setting up temporary amenities, access points, and storage areas. Create and share the safety plan for the site. Ensure that all staff receive training on the rules before starting work. Experts highly advise using software such as HammerTech to manage safety, people, and permits in real-time.
Safety isn't just a binder on a shelf; it is the most important element on a jobsite. Everyone's top priority is to make sure crews return home safely at the end of the day.
People conduct this in many ways, including daily safety briefings or "toolbox talks." Everyone must wear the personal protective equipment (PPE) before entering the site. (Bonus points if your team has inclusive PPE!)
A well-organized site ensures safety and efficiency and should include a site logistics plan that contains the following:
- where materials are kept
- where heavy equipment is
- how vehicles and workers will move on site
- location of trailer, restrooms, fence and designated break areas
- any regulatory information required by the local jurisdiction
- parking areas for crews
Step 3: Direct and Supervise On-Site Operations
Begin the physical construction activities according to the master schedule. Provide effective on-site supervision to coordinate tasks, manage subcontractors, and ensure daily operations align with the project goals.
The superintendent is the onsite leader. They are the main problem-solvers on the ground. They handle immediate issues and ensure that subcontractor teams work together. This helps them avoid competing for space or resources.
Among many tasks, they hold daily meetings to prepare the site for the work they will do. For example, they'll make sure that the area is clear for the concrete trucks to arrive and that the crew is ready to pour.
Step 4: Track Progress Against the Schedule
Monitor progress by comparing completed work against the project timeline. Use lookaheads plans and weekly plans to manage tasks. This helps you spot delays and keep the project on track.
This involves more than just checking boxes. It means understanding the critical path—the sequence of tasks that determines the project's total duration. Any delay on a critical path activity will delay the entire project.
Teams often use two- or three-week lookahead schedules to get a detailed, short-term view of what's coming. Lookaheads are most optimal when connected to the schedule.
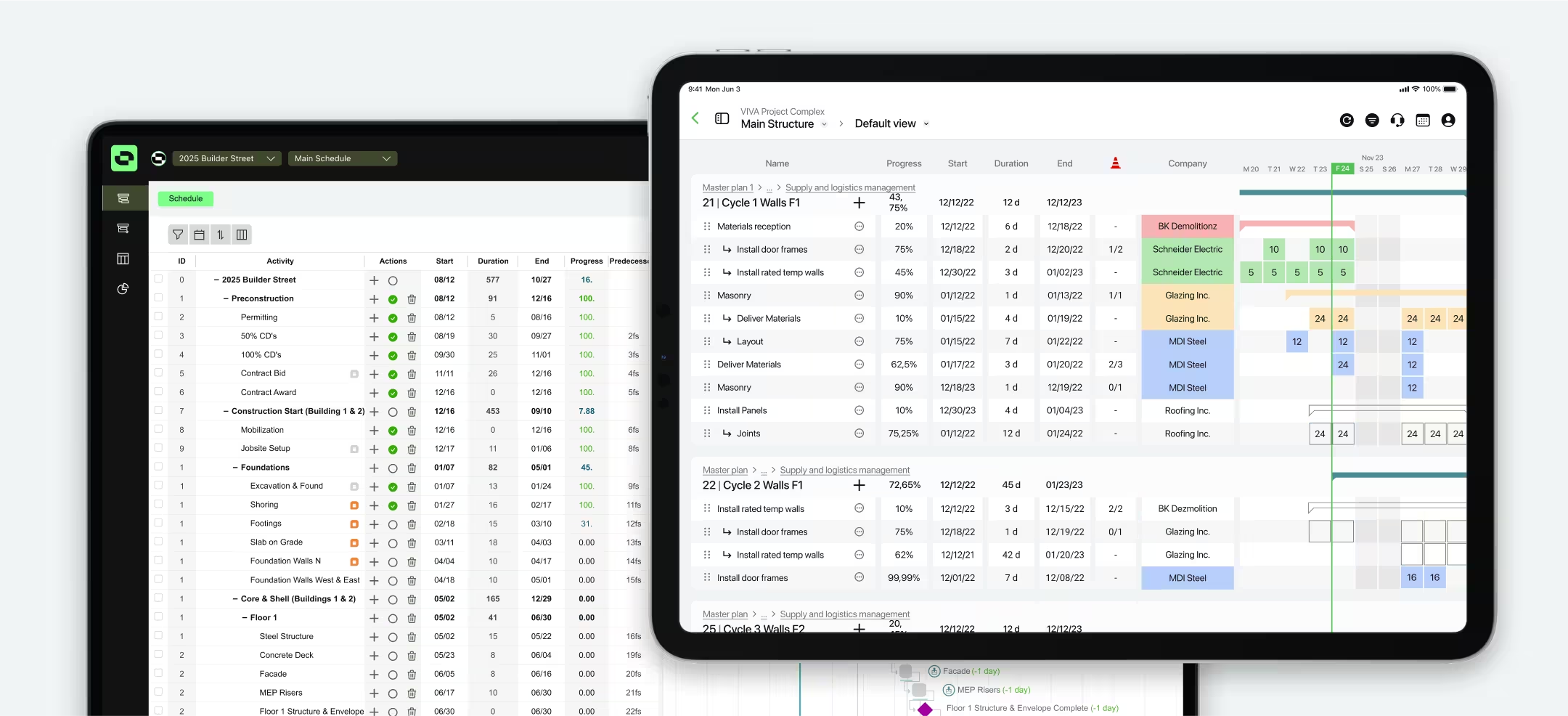
Step 5: Manage Budget and Material Procurement
Actively track all project expenses against the budget to prevent cost overruns. Oversee the procurement process by ordering, delivering, and storing materials efficiently to prevent shortages or work stoppages.
Effective budget management means assigning every dollar a job. Teams manage this by using cost codes to categorize expenses (e.g., concrete, labor, equipment rental).
As invoices and purchase orders come in, a team member codes and enters them into a tracking system. This lets the project manager see right away if they are over or under budget in any category.
Did you know that Outbuild simplifies budgeting by connecting cost tracking directly to project progress? Your team can log expenses and compare them to the budget. This gives you real-time financial visibility. It also helps you catch issues before they get worse.
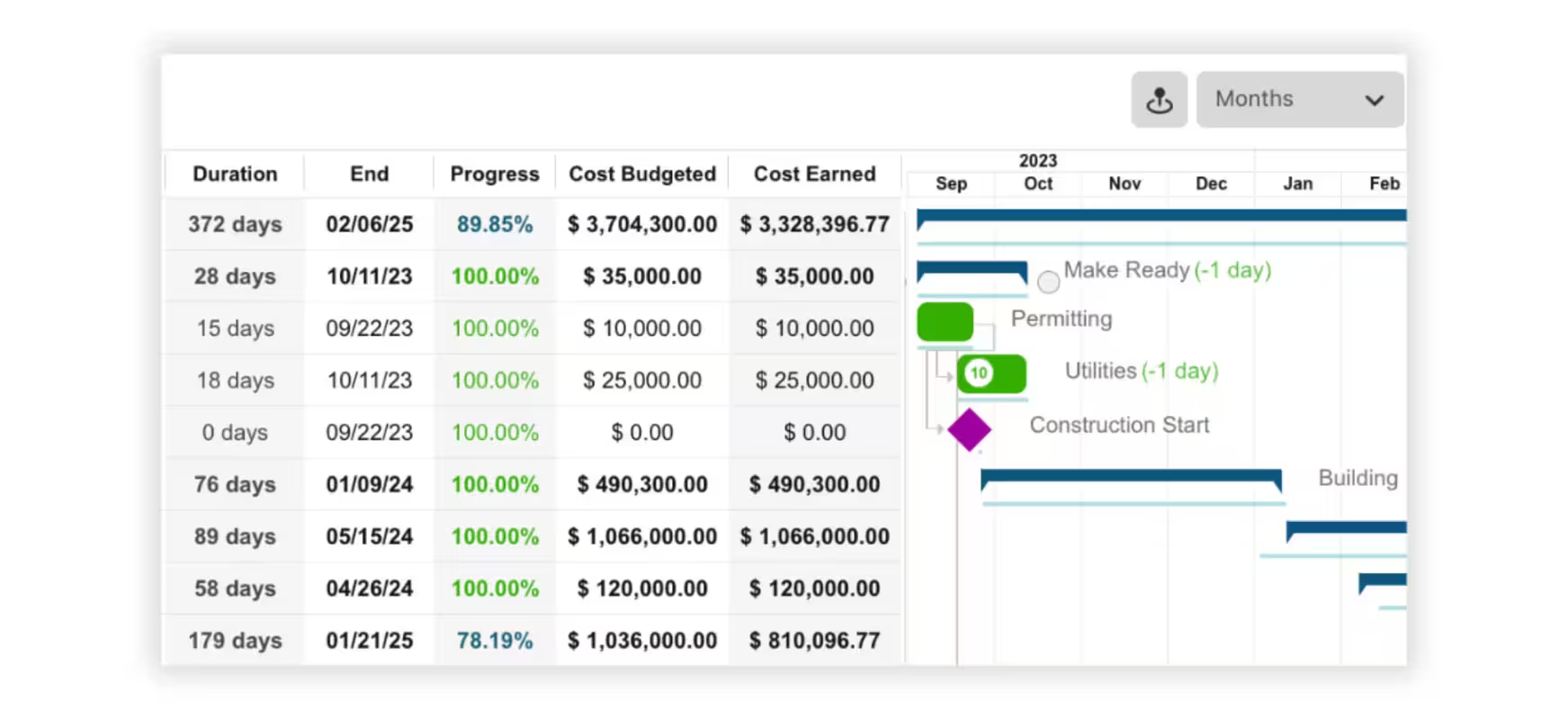
Step 6: Enforce Quality Control and Assurance
Conduct regular inspections and tests to verify that all work meets the specified quality standards and design requirements. Address any deficiencies promptly to maintain the integrity of the final structure.
Quality Assurance (QA) is about preventing defects, while Quality Control (QC) is about identifying them. QA involves processes like pre-qualifying subcontractors and using proven construction methods. QC is the hands-on inspection part.

Step 7: Maintain a Clear Communication Plan
Establish a consistent rhythm for project meetings and progress reports. Keep project stakeholders, including clients, designers, and internal teams, informed of milestones, challenges, and decisions to ensure alignment.
Communication flows in all directions. Regular owner-architect-contractor (OAC) meetings keep the client and design team updated. Weekly subcontractor meetings align all the trades working on site. Daily huddles address immediate needs.
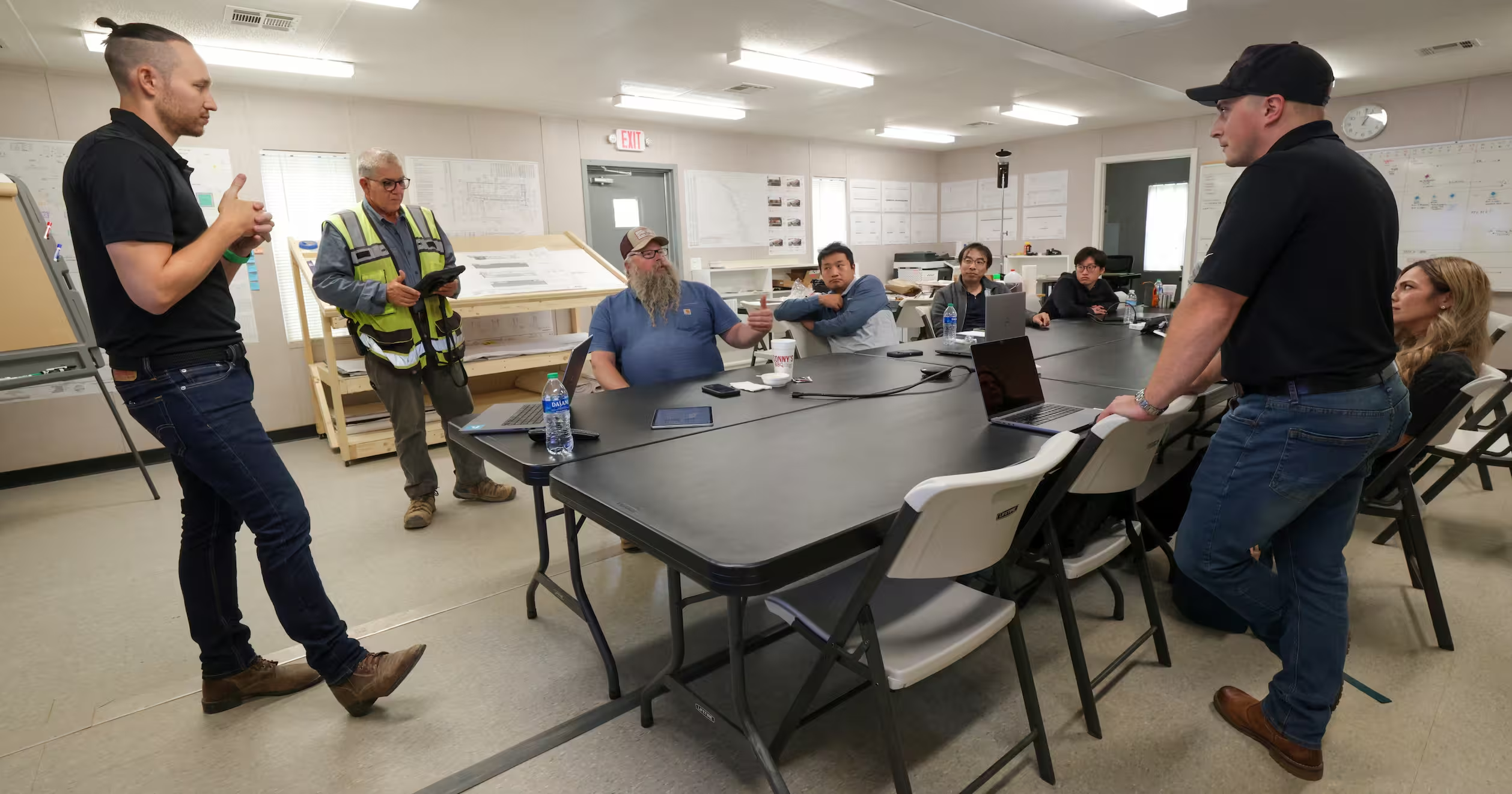
Step 8: Manage Comprehensive Project Documentation
Keep meticulous records of all project activities, including daily logs, meeting minutes, requests for information (RFIs), and financial transactions. Accurate documentation is crucial for accountability, dispute resolution, and future reference.
- A daily log is a diary of the project. It records the weather, the number of workers on site for each trade, the work performed, any issues that arose, etc.
- RFIs in construction are formal questions sent to the design team to clarify a drawing or specification.
- Submittals are documents that the contractor sends to the designer. They confirm that the team will use the right materials and equipment.
%2012.19.53%E2%80%AFp.m..png)
Step 9: Handle Change Orders and Solve Problems
Proactively identify and address unexpected issues and requests for changes. Create a clear process to evaluate, approve, and document change orders. This will help reduce their impact on the schedule and budget.
Change is inevitable in construction. The key is how you manage it. A formal change order process has several steps:
- First, identify the need for a change.
- Next, estimate the cost and time impact.
- Then, send the change proposal to the owner for approval.
- Once approved, create a formal change order document.
Step 10: Conduct Performance Reviews and Capture Lessons Learned
Regularly evaluate project performance for safety, cost, schedule, and quality. At the project's conclusion, compile a "lessons learned" report to improve processes for future projects.
This final step is an investment in the future. After the project is complete, the team should hold a lesson learned meeting. What went well that we should repeat? What went wrong, and why?
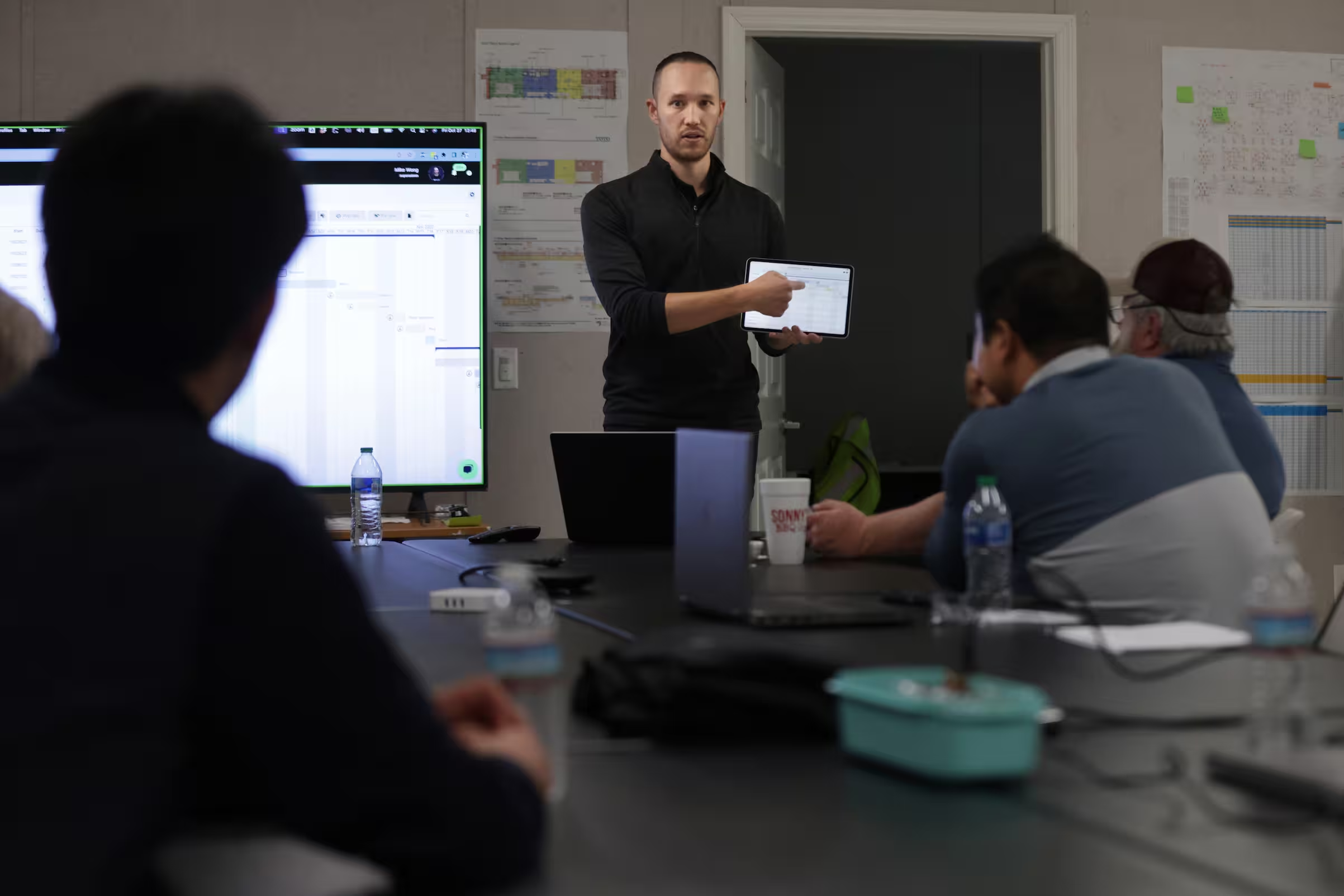
A well-crafted execution plan includes multiple components that act as the foundation of your project’s success.
Are you looking for a construction project execution plan sample? Or, need a construction project execution plan template? This outline covers the key areas.
Project Goals and Scope
Define the overall objectives and scope to set clear benchmarks for success.
Key Roles and Responsibilities
Assign roles like project managers, contractors, and subcontractors. For instance, a Construction Project Executive oversees the entire execution phase from a high level, ensuring alignment across stakeholders.
The construction project executive job description typically involves strategic oversight, financial control, and acting as the main point of contact for the client.
Master Schedule and Key Milestones
Use a detailed schedule to map out tasks, deadlines, and milestones critical to your project timeline. Tools like construction scheduling and planning software make this step seamless.
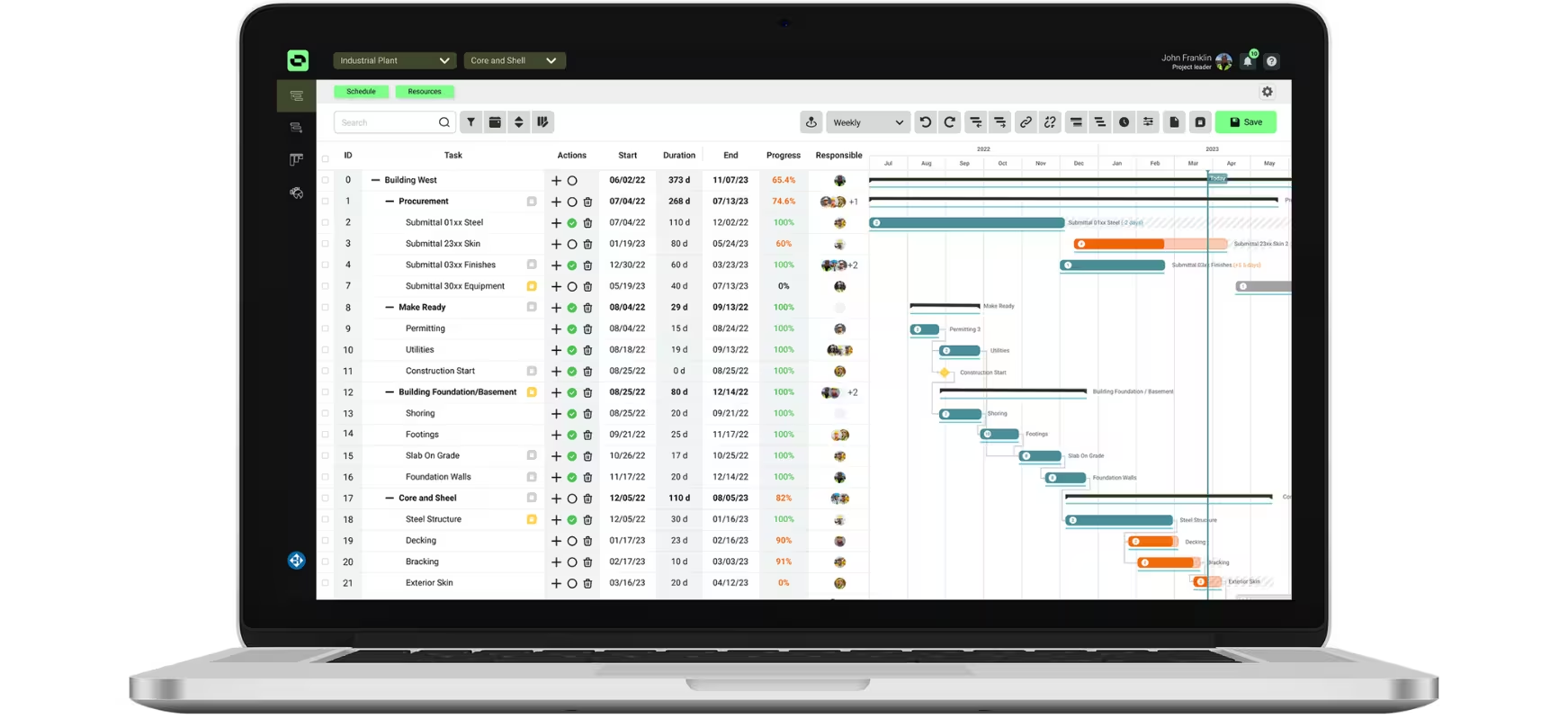
Budget and Cost Management
Outline all financial details to avoid cost overruns. This section should include contingencies for any unforeseen expenses for the project, including labor and materials.
Site Safety and Health Plan
Ensure all safety protocols and health guidelines are clearly documented and enforced.
Quality Control and Assurance
Define standards for quality and procedures for inspections and tests to meet these benchmarks.
Procurement and Materials Management
Track material orders, delivery timelines, and storage requirements, ensuring resources are always available without delay.
Your Next Step to Mastering Construction Execution
Successful project execution boils down to a well-prepared plan, precise management, and continuous monitoring. You can lower risks and achieve your project goals by using tools like construction scheduling and field coordination software.
For even more optimized project execution, explore how Outbuild’s solutions can transform your approach today. Book a demo or start your free trial today. See how Outbuild can help you crush your project execution goals.
Frequently Asked Questions
The Construction Project Executive holds primary responsibility for overseeing and ensuring successful execution while coordinating among stakeholders that are boots on the ground. The Project Manager drives day-to-day planning, budgeting, and communication, while the Superintendent leads on-site operations, ensuring work is executed safely, efficiently, and to spec.
The execution phase of a construction project is when plans turn into action—crews mobilize, materials are delivered, and actual building begins. This phase involves coordinating labor, managing subcontractors, tracking progress against the schedule, and maintaining quality and safety standards. Strong communication and real-time visibility are critical to keeping things on track.
Early identification of potential changes, clear documentation, and swift decision-making are key. Regular monitoring and flexible contingency plans also help.
Platforms like Outbuild’s construction scheduling and planning software ensure smoother workflows by integrating scheduling, resource allocation, and communication.
Related Articles
Ready to see Outbuild?
Join hundreds of contractors from 10+ countries that are saving money by scheduling better