Outbuild is online scheduling software to work together on connected project schedules and look-aheads, enabling everyone to move faster.
Key Takeaways
Table of contents
- What is Quality Assurance in Construction?
- Building a Construction Quality Assurance Plan
- Essential Steps to Develop a Construction Quality Assurance Plan
- Quality Assurance Procedures in Construction Projects
- Implementing Quality Assurance in Construction Management
- The Role of Technology in Modern Construction QA
- Building a Culture of Quality: Beyond Checklists and Procedures
- Leadership's Role in Quality Assurance
- Real World Examples and Case Studies
In construction, timelines, budgets, and safety are important. But we can't forget about quality assurance – it is also essential. QA in construction helps operations run smoothly and helps avoid repeated setbacks.
In vertical building construction or civil and infrastructure projects, a proactive approach helps prevent errors before they happen.
For Project Managers and Superintendents, the stakes are high. Quality assurance in building construction involves detailed planning and open communication channels.
We hear about quality control and also about quality assurance. Both quality control and assurance in Construction are paramount. But, what's the difference?
Quality control is when a team finds and fixes problems through inspections and tests. In contrast, a good quality assurance framework tries to prevent issues before they happen. It does this by integrating standards from the very beginning.
This proactive approach limits costly rework, keeping schedules tight, and protecting profit margins.
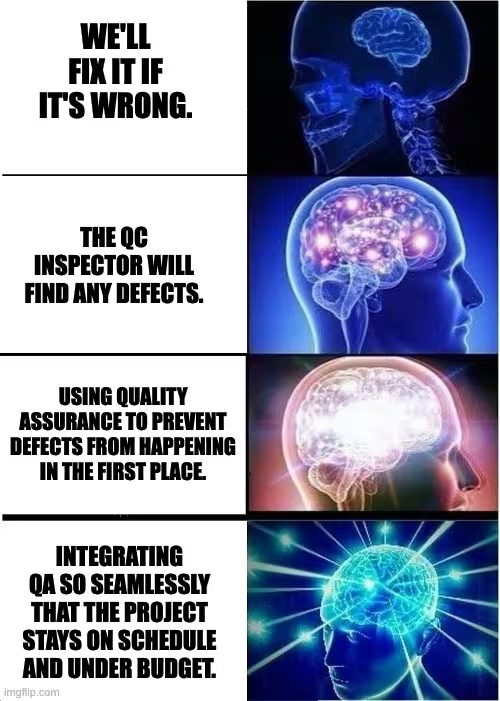
Quality assurance is the proactive, systematic process of ensuring that project deliverables meet or exceed predefined regulations, contractual obligations, and industry standards.
In a construction setting, quality assurance is about establishing guidelines early and then following them consistently. It is important no matter what type of project you are working on. This includes building a high rise or ensuring quality in road construction.
A construction quality assurance plan is a key document for everyone involved. It explains how to meet quality goals from the start of the project until the team finishes it.
This plan is more than a policy statement. It is a clear roadmap that outlines responsibilities, inspection points, and documentation methods.
- Define Project Scope: Clearly outline the responsibilities of the construction team and timeline.
- Set Quality Objectives and Benchmarks: Establish measurable, achievable goals.
- Assign Responsibilities: Detail who oversees QA tasks, from the Project Manager to on-site Superintendents.
- Align Schedule with QA Construction Milestones: Integrate QA checks within your overall construction schedule.
- Document Communication Protocols: Decide how and when you will share updates, changes, or concerns from the construction site.
Incorporate a quality assurance plan into a larger standard operating procedure and then tailor it for the project.
A quality assurance plan for a construction project in the commercial industry is important. For example, it may focus on certifying materials, especially structural steel.
A quality assurance plan for a road construction project would focus on how often to test asphalt. It would also look at subgrade compaction rates and provide clear traffic management guidelines.
A construction quality assurance plan might include a daily sign-off sheet. This sheet confirms that important checks, like verifying concrete strength, happen each morning.
Standardized processes and quality requirements ensure all team members, from Superintendents to subcontractors, align with the same goals.
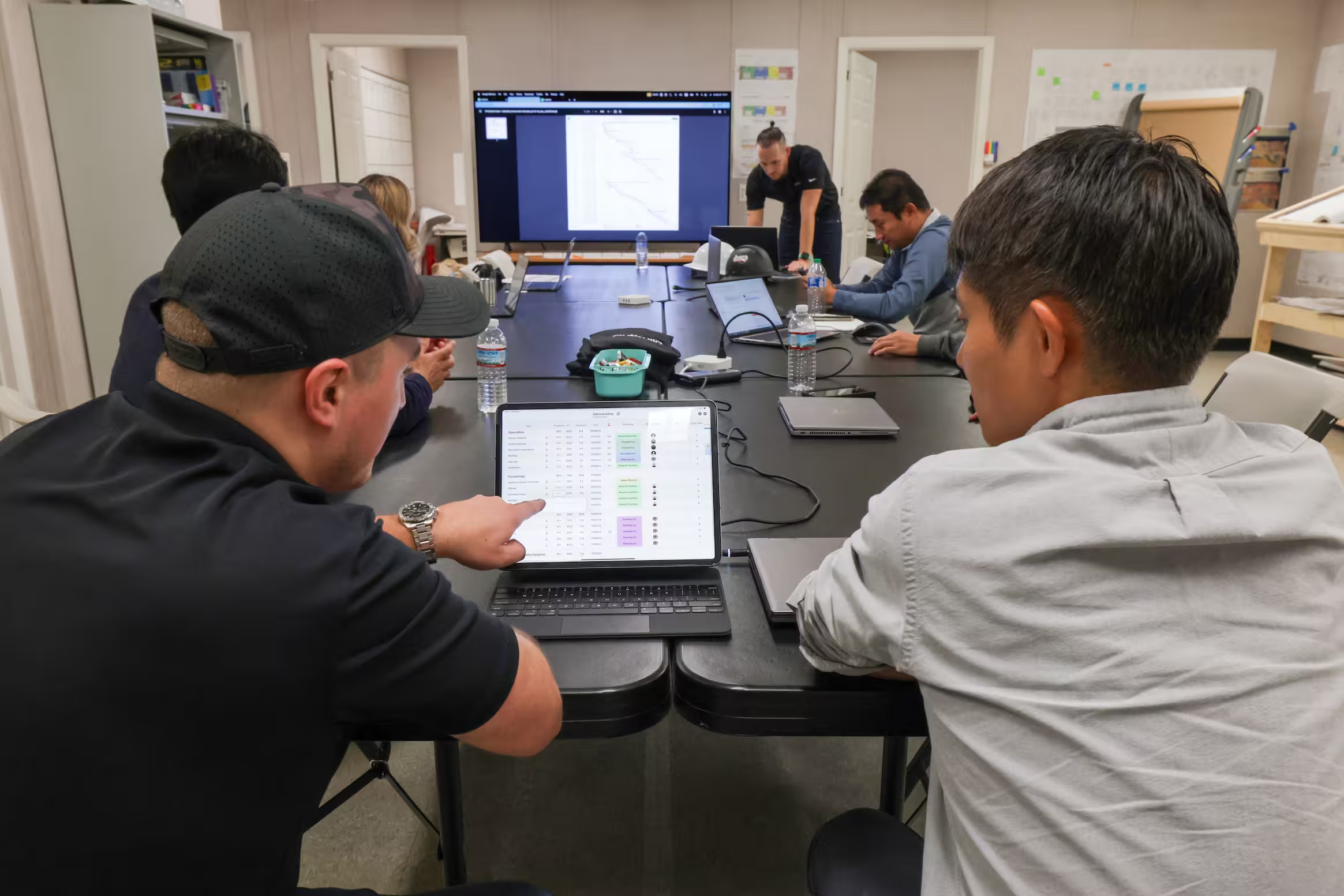
Implementing quality assurance procedures in construction is where theory meets practice. These procedures transform a project’s QA plan into daily actions on the jobsite.
Key Procedures Include:
- Site Documentation: Maintain accurate logs of deliveries, crew attendance, and test results.
- Material Testing: Conduct scheduled tests on concrete, steel, or asphalt to confirm compliance with project requirements.
- Subcontractor Coordination: Ensure all partners follow consistent QA guidelines.
- Method Statements: Provide clear steps for complex tasks. This includes forming and pouring concrete or laying utility lines.
Quality assurance in construction projects also involves audits to verify that processes remain effective. Safety standards and quality assurance in construction closely tie together. This means that identifying hazards is an ongoing task, not just a one-time job.
Beyond preventing defects, these procedures manage risk. Identifying potential issues early prevents them from snowballing into bigger problems.
Being able to deliver quality projects gives a competitive edge. This is important when potential clients look at past work, references, and records.
Quality assurance in construction management begins at the leadership level. Leadership sets the tone by establishing clear priorities, allocating resources, and monitoring results.
A culture where everyone takes responsibility for quality often does better than one where quality is a separate job.
The days of relying solely on paper checklists and three-ring binders are fading. Modern technology has changed the way we do quality assurance. It has turned a difficult task into a simple, data-driven process. Leveraging the right digital tools is no longer a luxury—it’s a competitive necessity.
A Few Examples of Tools:
- Project Management & QA/QC Software: Platforms like Procore and Autodesk are central hubs for QA. Teams can create standard digital checklists. They can attach photos with timestamps and locations.
They can assign tasks to people and track issues from start to finish. This creates a transparent digital record that is accessible to everyone from the office to the field.

- Building Information Modeling (BIM): BIM is a powerful proactive QA tool. By creating a detailed 3D model of the project, teams can conduct "clash detection" virtually.
This process finds where different systems, like HVAC ducts, plumbing, and structural steel, clash with each other. This occurs before anyone orders or installs any material. Resolving these clashes in the model prevents costly and schedule-killing rework on site.
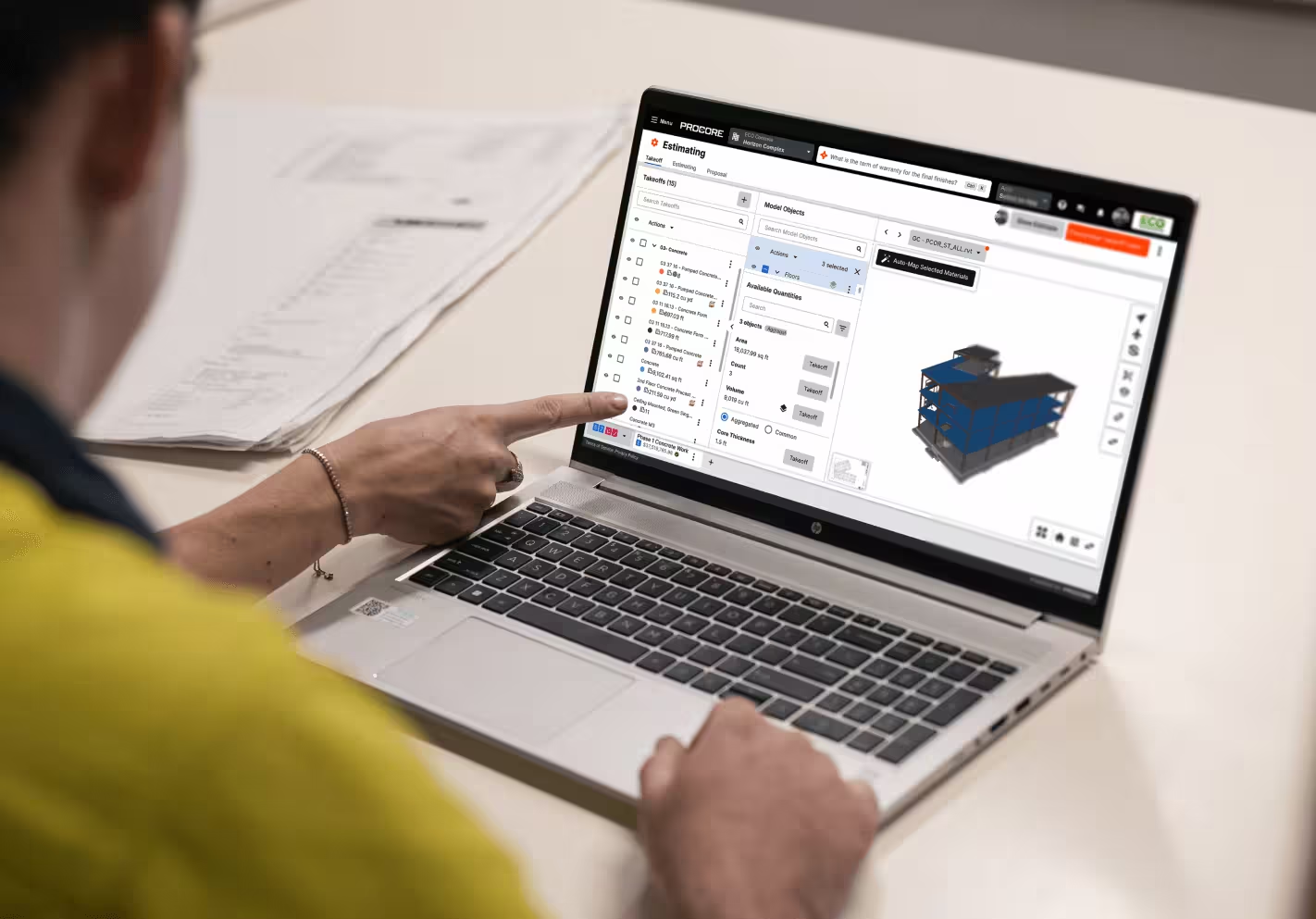
- Construction Scheduling and Planning Platforms: Proactive quality assurance starts with a solid plan. Platforms like Outbuild enable teams to build highly detailed, realistic schedules from the very beginning.
To ensure quality, add QA milestones to the master schedule. These milestones include pre-installation meetings, material testing, and inspection hold points.
This way, it is not just an afterthought. This stops teams from rushing important tasks. It gives enough time for checking work. It also helps spot possible problems before they affect quality on site.
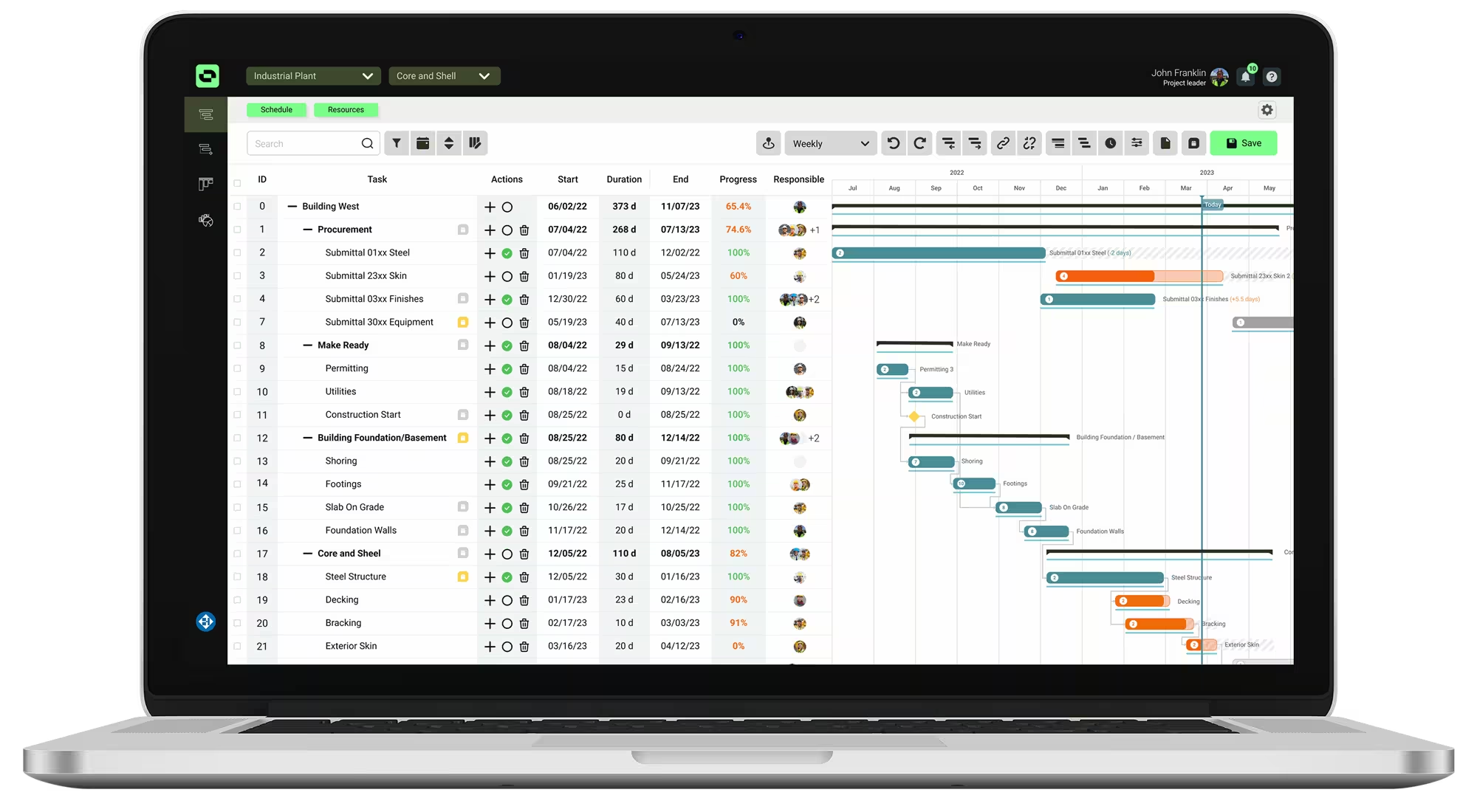
Plans, procedures, and technology are important parts of a QA system. However, they only work well if the team using them is committed to quality.
The best construction companies create a culture of quality. Every person at the job site has a role. This includes the Project Executive and the newest laborer. They all feel a sense of ownership over the final product.
A leader should be prepared for the following:
- Budget allocation for training, digital tools, and additional resources.
- Regularly scheduled QA meetings to review benchmarks and address concerns.
- Encouragement of open communication so that on-site teams quickly report issues.
Training is an important strategy in maintaining consistent QA standards. Whether in a formal meeting or during on-site mentorship, trained employees can find potential errors early. This helps prevent major issues. This ensures quality assured construction, rather than simply relying on reactive fixes.
Digital technologies offer real-time reporting, defect-tracking, and standardized checklists. Many general contractors find that smart device apps and project management software help with QA tasks. These tools make it easier to document work and plan construction schedules.
Translating theory into practice is easiest when you see how others have succeeded. Below is a quality assurance construction example that illustrates how a diligent QA approach can pay off.
Quality Assurance in Construction Example #1
Scenario: A commercial general contractor won the bid for a high-rise office building project.
QA Framework: The team created a construction quality assurance plan. This plan requires trade partners to attend pre-installation meetings. They must also submit mock-ups for important parts, like exterior glazing assemblies. Additionally, they need to follow standardized checklists. Floor leads will verify these checklists before each build phase.
Outcome: This proactive approach identified design and detailing issues early. It found misalignment in glazing frame anchors during the mock-up review. This helped prevent costly rework and delays in installation. The project stayed on schedule, and field teams reported stronger alignment and confidence thanks to clear QA processes.
Quality Assurance in Construction Example #2
Scenario: A general contractor led a highway expansion project requiring tight quality control across soil, asphalt, and striping work.
QA Framework: The team created a proactive QA plan. This plan includes pre-task meetings, standardized checklists, and in-process checks. These checks focus on compaction, material temperatures, and alignment. All of this is part of the daily crew workflows.
Outcome: This approach flagged issues early, like a cooling asphalt batch, before installation. The project saw minimal rework, passed inspections smoothly, and earned DOT recognition for consistent quality.
By focusing on QA, you will keep projects on time. This helps keep budgets healthy and clients happy. It also creates a safer working environment for everyone.
From streamlined planning to real-time collaboration, Outbuild empowers teams to stay aligned, minimize rework, and build with confidence. Book a demo or start your free trial today. See how Outbuild can help you finish your next project on time, within budget, and with great quality.
The days of relying solely on paper checklists and three-ring binders are fading. Modern technology has changed the way we do quality assurance. It has turned a difficult task into a simple, data-driven process. Leveraging the right digital tools is no longer a luxury—it’s a competitive necessity.
A Few Examples of Tools:
- Project Management & QA/QC Software: Platforms like Procore and Autodesk are central hubs for QA. Teams can create standard digital checklists. They can attach photos with timestamps and locations.
They can assign tasks to people and track issues from start to finish. This creates a transparent digital record that is accessible to everyone from the office to the field.

- Building Information Modeling (BIM): BIM is a powerful proactive QA tool. By creating a detailed 3D model of the project, teams can conduct "clash detection" virtually.
This process finds where different systems, like HVAC ducts, plumbing, and structural steel, clash with each other. This occurs before anyone orders or installs any material. Resolving these clashes in the model prevents costly and schedule-killing rework on site.
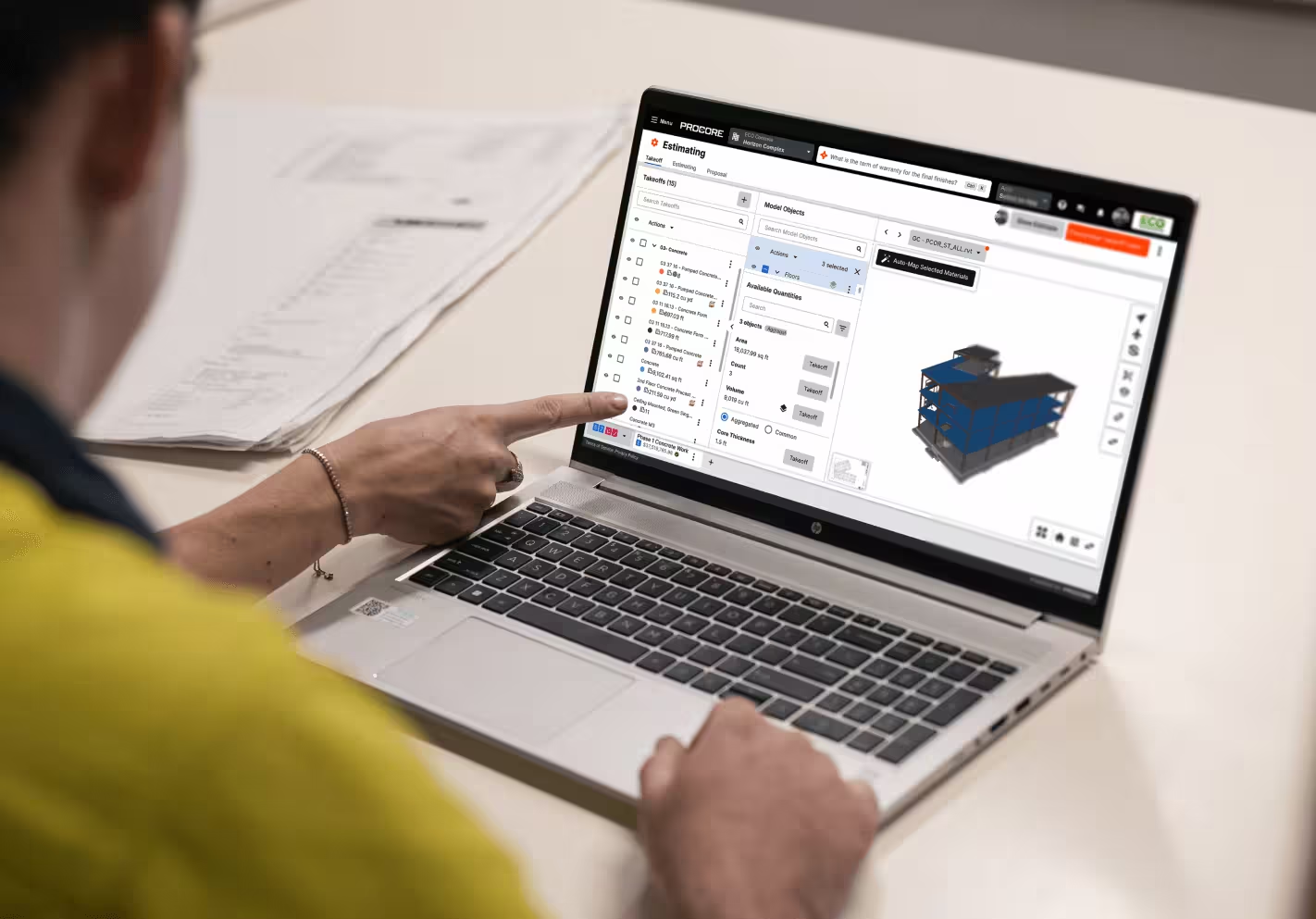
- Construction Scheduling and Planning Platforms: Proactive quality assurance starts with a solid plan. Platforms like Outbuild enable teams to build highly detailed, realistic schedules from the very beginning.
To ensure quality, add QA milestones to the master schedule. These milestones include pre-installation meetings, material testing, and inspection hold points.
This way, it is not just an afterthought. This stops teams from rushing important tasks. It gives enough time for checking work. It also helps spot possible problems before they affect quality on site.
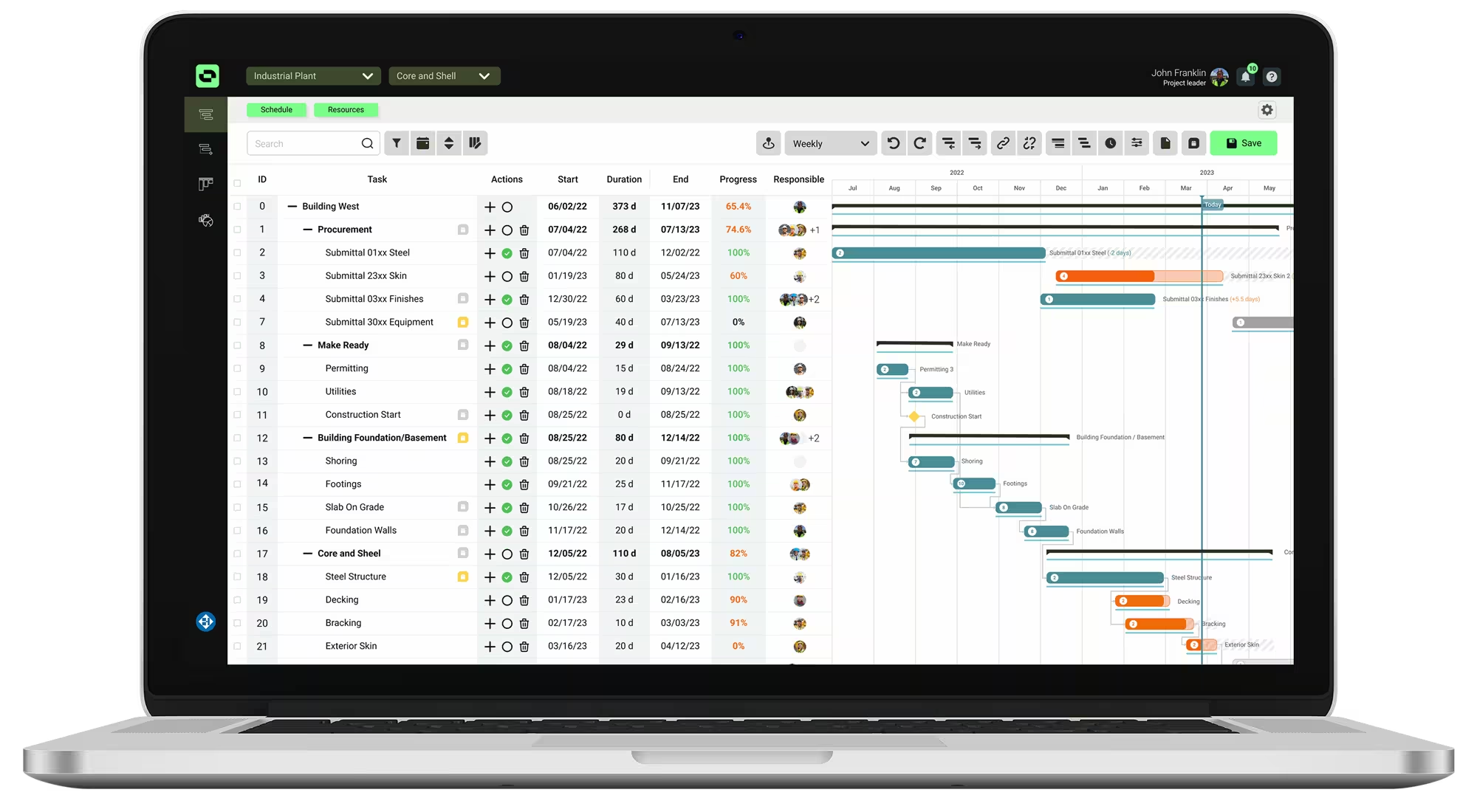
Plans, procedures, and technology are important parts of a QA system. However, they only work well if the team using them is committed to quality.
The best construction companies create a culture of quality. Every person at the job site has a role. This includes the Project Executive and the newest laborer. They all feel a sense of ownership over the final product.
A leader should be prepared for the following:
- Budget allocation for training, digital tools, and additional resources.
- Regularly scheduled QA meetings to review benchmarks and address concerns.
- Encouragement of open communication so that on-site teams quickly report issues.
Training is an important strategy in maintaining consistent QA standards. Whether in a formal meeting or during on-site mentorship, trained employees can find potential errors early. This helps prevent major issues. This ensures quality assured construction, rather than simply relying on reactive fixes.
Digital technologies offer real-time reporting, defect-tracking, and standardized checklists. Many general contractors find that smart device apps and project management software help with QA tasks. These tools make it easier to document work and plan construction schedules.
Translating theory into practice is easiest when you see how others have succeeded. Below is a quality assurance construction example that illustrates how a diligent QA approach can pay off.
Quality Assurance in Construction Example #1
Scenario: A commercial general contractor won the bid for a high-rise office building project.
QA Framework: The team created a construction quality assurance plan. This plan requires trade partners to attend pre-installation meetings. They must also submit mock-ups for important parts, like exterior glazing assemblies. Additionally, they need to follow standardized checklists. Floor leads will verify these checklists before each build phase.
Outcome: This proactive approach identified design and detailing issues early. It found misalignment in glazing frame anchors during the mock-up review. This helped prevent costly rework and delays in installation. The project stayed on schedule, and field teams reported stronger alignment and confidence thanks to clear QA processes.
Quality Assurance in Construction Example #2
Scenario: A general contractor led a highway expansion project requiring tight quality control across soil, asphalt, and striping work.
QA Framework: The team created a proactive QA plan. This plan includes pre-task meetings, standardized checklists, and in-process checks. These checks focus on compaction, material temperatures, and alignment. All of this is part of the daily crew workflows.
Outcome: This approach flagged issues early, like a cooling asphalt batch, before installation. The project saw minimal rework, passed inspections smoothly, and earned DOT recognition for consistent quality.
By focusing on QA, you will keep projects on time. This helps keep budgets healthy and clients happy. It also creates a safer working environment for everyone.
From streamlined planning to real-time collaboration, Outbuild empowers teams to stay aligned, minimize rework, and build with confidence. Book a demo or start your free trial today. See how Outbuild can help you finish your next project on time, within budget, and with great quality.
Frequently Asked Questions
The quality assurance process plan is important in construction because it helps save time, save money, improve safety and enhance reputation.
The quality assurance in construction industry best practices include top-down commitment, pre-installation meetings, leveraging technology and empowering the field.
Quality assurance focuses on improving quality before a project starts. It takes a proactive approach to process improvement. Quality control is identifying and correcting issues during construction. Quality assurance isn’t just about avoiding mistakes—it’s about delivering excellence and customer satisfaction from day one. We like to think of it as construction assurance. If you’re ready to elevate your QA processes and drive better project outcomes, explore how Outbuild can help.
Related Articles
Ready to see Outbuild?
Join hundreds of contractors from 10+ countries that are saving money by scheduling better