Outbuild is online scheduling software to work together on connected project schedules and look-aheads, enabling everyone to move faster.
Key Takeaways
Table of contents
- Defining QA and QC in Construction
- Quality Assurance vs. Quality Control in Construction
- Importance of QA/QC Plans in Construction Projects
- QA/QC Program Construction Framework
- Best Practices & Common Pitfalls of QA QC in Construction
- The role of Scheduling in QA/QC
Both Quality assurance (QA) and quality control (QC) play a critical role in construction projects. QA focuses on preventing errors before work begins, and QC is about identifying and fixing issues during construction.
In this blog, we will explore QA and QC in construction, the differences, similarities and importance of both.
If you’ve ever wondered about the qa qc meaning in construction, you’re not alone. People often use these terms interchangeably, but mastering both—individually and together—remains critical for consistent project success.
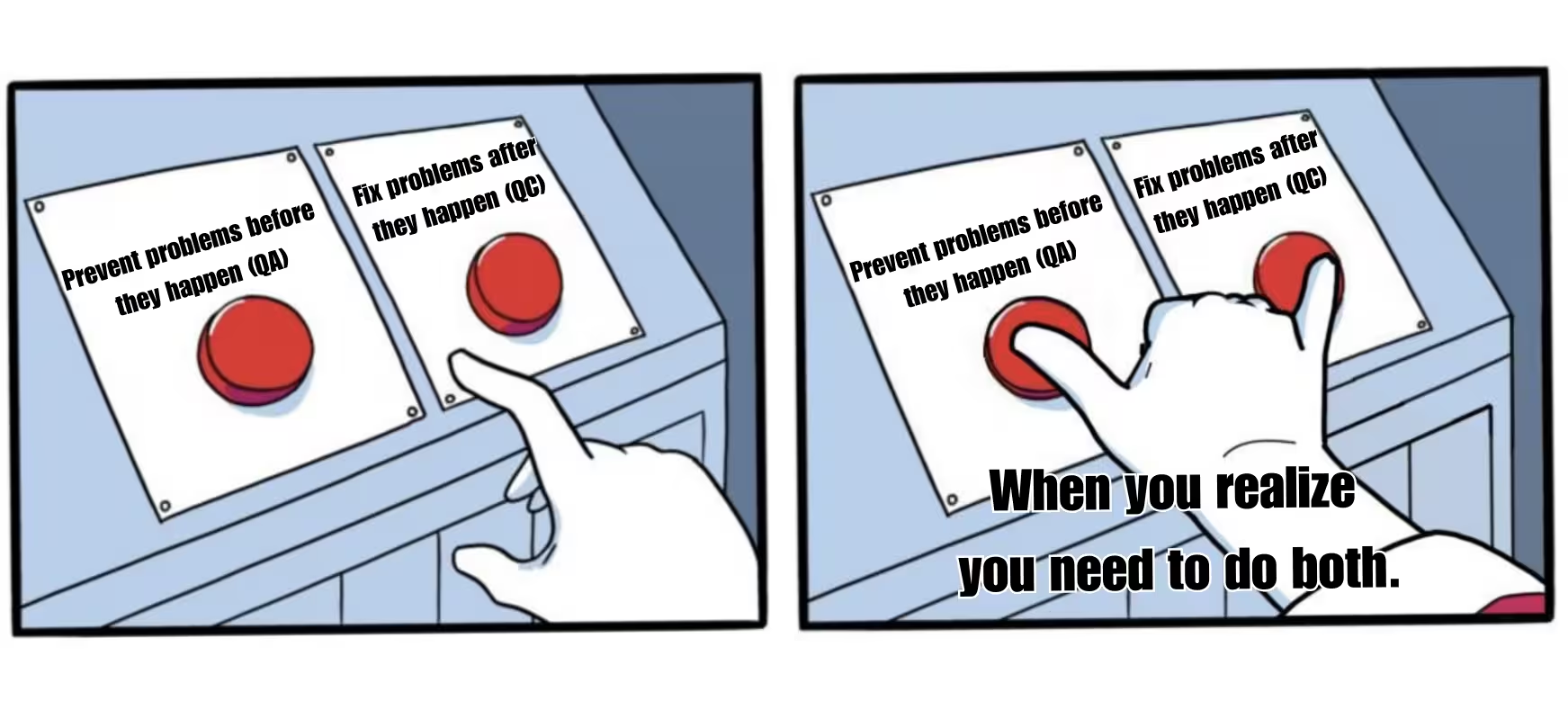
QA sets the foundation through standards, training, and documentation before a project starts. A team puts it into place to ensure every phase meets predetermined quality requirements.
A great example of this is a three-phase quality plan, which includes a plan outlining preparatory, initial, and follow-up phases to proactively prevent issues and verify quality at every step of construction.
QC ensures that the team completes the work correctly. It involves inspections, testing, and corrective actions to verify compliance with plans.
For example, a project manager might notice the rebar in a concrete slab isn’t spaced the way the plans show, and she flags it before the concrete is poured. Catching this issue prevents potential structural problems and costly rework later and is a great example of quality control.
Managing quality helps teams meet regulations, avoid costly rework, and maintain a reputation for excellence. Having a quality control and quality assurance plan for construction projects is imperative for success.
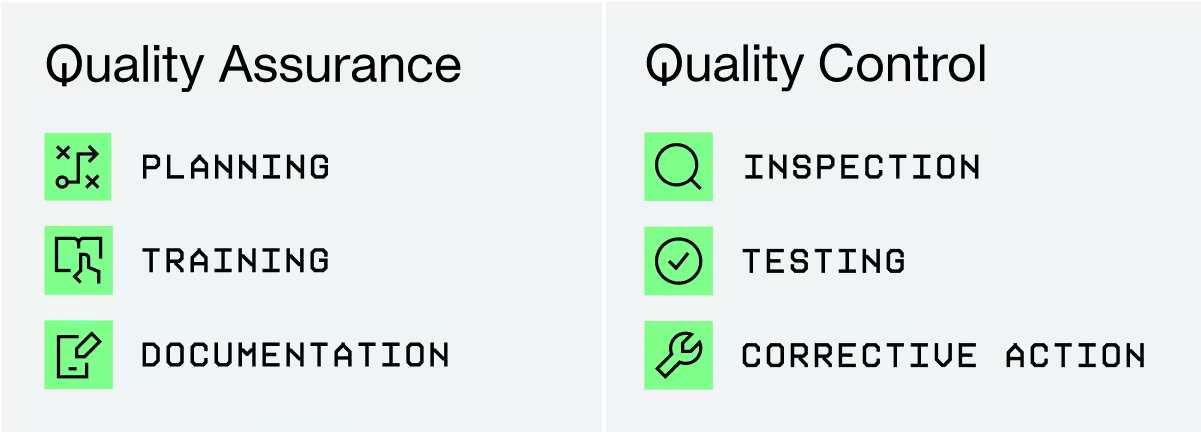
What is the difference between quality assurance and quality control in construction?
Quality Assurance (QA) and Quality Control (QC) focus on different parts of a construction project. QA is about prevention, while QC is about detection.
Quality Assurance (QA)
- Purpose: QA focuses on preventing errors before construction begins.
- Processes: Develops standards and procedures for handling materials, scheduling tasks, and communication among teams.
- Planning: Create a detailed plan outlining inspection points, testing methods, and acceptance criteria.
- Documentation: Creates extensive documentation, including inspection schedules and checklists, to guide the team throughout the project.
- Continuous Improvement: Regularly reviews and updates procedures to reduce risks and improve project outcomes.
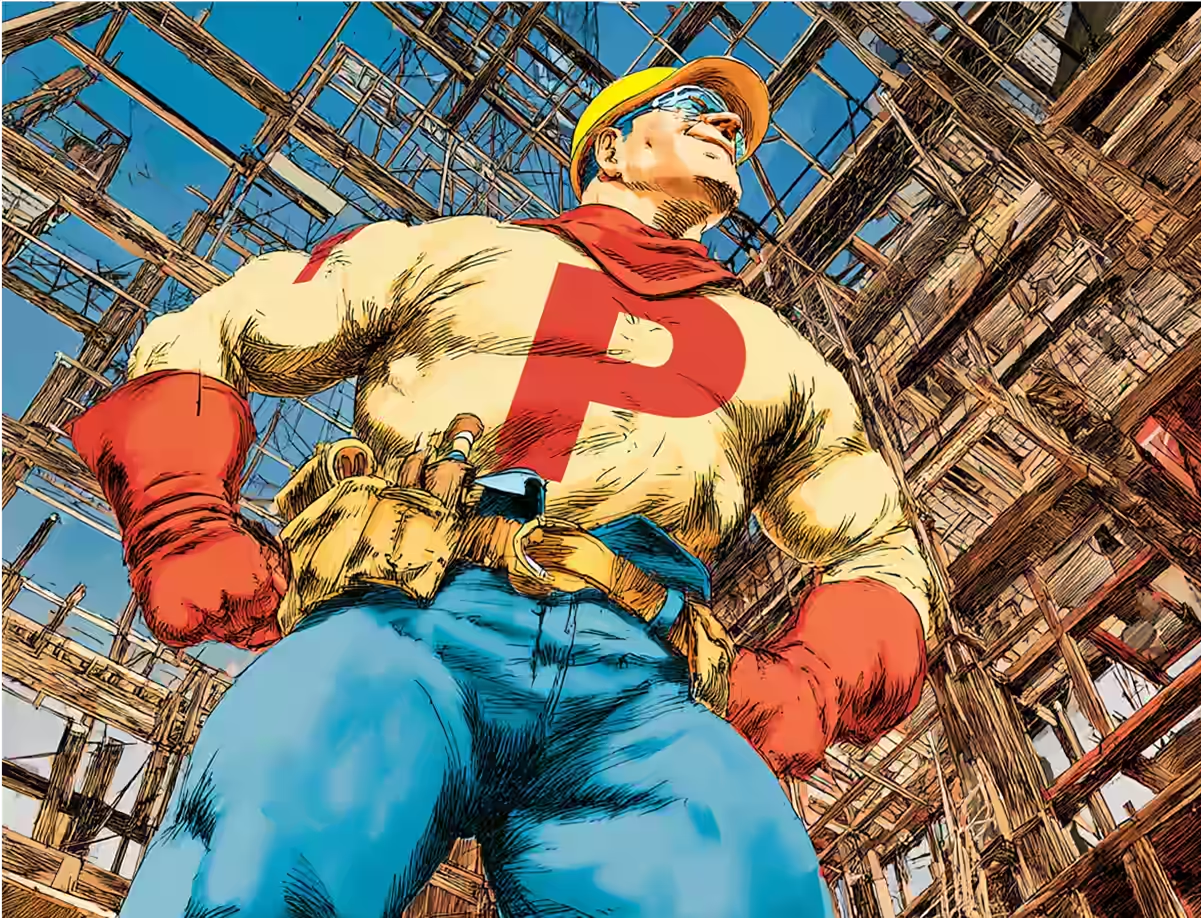
Quality Control (QC)
- Purpose: QC focuses on detecting and correcting defects during construction.
- Execution: Perform inspections, tests, and final quality checks. Checks materials, workmanship, and installation accuracy according to project plans and standards.
- Defect Management: The team records findings, reports issues, and ensures they complete corrective actions.
- Verification: Re-inspect the corrected work to confirm that the team has resolved the problems.
- Documentation: Maintain detailed records of inspections, tests, and fixes for accountability.
- Continuous Monitoring: Conducts regular inspections throughout the project to maintain quality until completion.
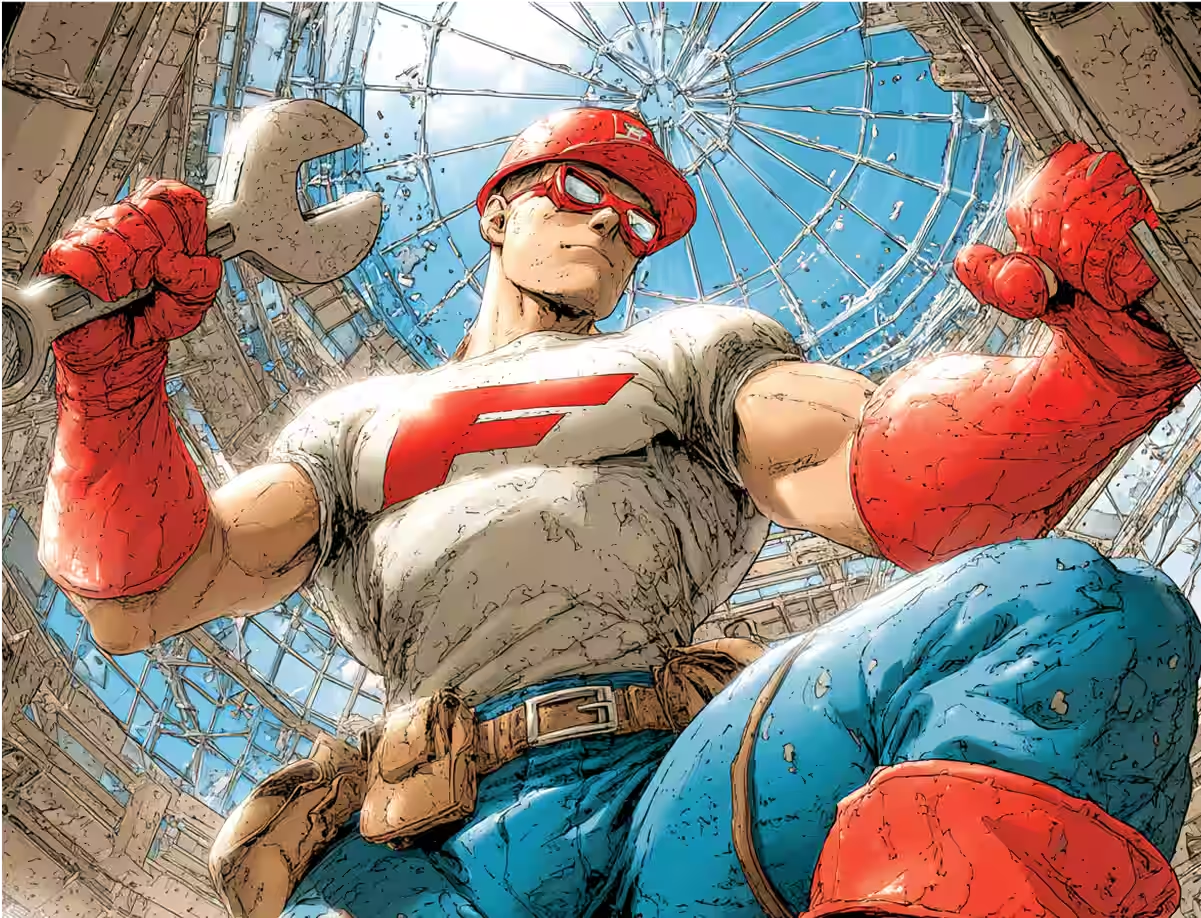
A formal qa qc plan for construction project success is essential—no matter the size or scope. A strong plan outlines who’s responsible, which standards apply, and how inspections will occur. Core components include:
- Defined Objectives – Clear, measurable quality and safety goals
- Assigned Roles – Responsibilities for documentation, inspection, and approvals
- Set Schedules – Regular audits and reviews
If you’re looking to introduce or refine a QA/QC framework, a qa qc program template for construction can be a game-changer. It typically includes:
- Objectives and Scope – What’s covered and how quality will be measured
- Roles and Responsibilities – Who’s in charge of what
- Documentation Protocols – Where and how records are stored
- Training and Compliance – Scheduling formal instruction
- Continuous Improvement – Ongoing evaluations and adjustments
Many companies now digitize QA QC procedures in construction through software such as Procore's Action Plans.
Quality control and quality assurance in construction demand diligence, teamwork, and a commitment to continuous improvement. Below are some best practices—and a few pitfalls to avoid:
Best Practices of QA QC in Construction
- Consistent Training: Hold regular workshops to teach staff the latest QA/QC procedures. Encourage questions and hands-on practice to ensure everyone understands.
- Inspections: Crew members must do thorough inspections. They should log these inspections in real-time. After that, they need to take corrective action.
- Technology: Keep records updated through a digital construction software hub. There are many software tools that help with good QA/QC for construction projects. Strong project management software and effective scheduling software are important.
- Team Communication: Encourage a culture that welcomes reporting errors or potential issues instead of punishing it. This fosters transparency and quick problem-solving.
- Routine Audits: Conduct scheduled and surprise inspections to keep teams vigilant and maintain high standards.
Common Pitfalls of QA QC in Construction
- Inconsistent Inspections: Sometimes, teams skip steps or rush through checks, assuming everything is fine. This can lead to overlooked defects that become costly later.
- Poor Staff Training: If your staff doesn't know how to fill out forms or read plans properly, your QA/QC framework loses its effectiveness.
- Ignoring Minor Defects: Even small deviations can cause big problems in structural integrity or project scheduling.
- Failing to Update Plans: Construction methods and regulations evolve and documentation must mirror this.
Putting qa qc construction protocols into everyday practice helps minimize these risks. Each step, from daily site checks to final project sign-off, is an important piece of the construction process.
A good quality control and assurance plan for construction projects is more than a checklist. It is a strategic tool. This helps keep your project on schedule, meet regulations, and satisfy stakeholders.
By creating clear standards in a construction QA QC plan template, you provide every team member with a clear path to follow. And by routinely inspecting work, you catch issues before they escalate into expensive, time-consuming problems.
If you’ve been searching for ways to strengthen your qa qc plan for construction project goals, now is the time to act.
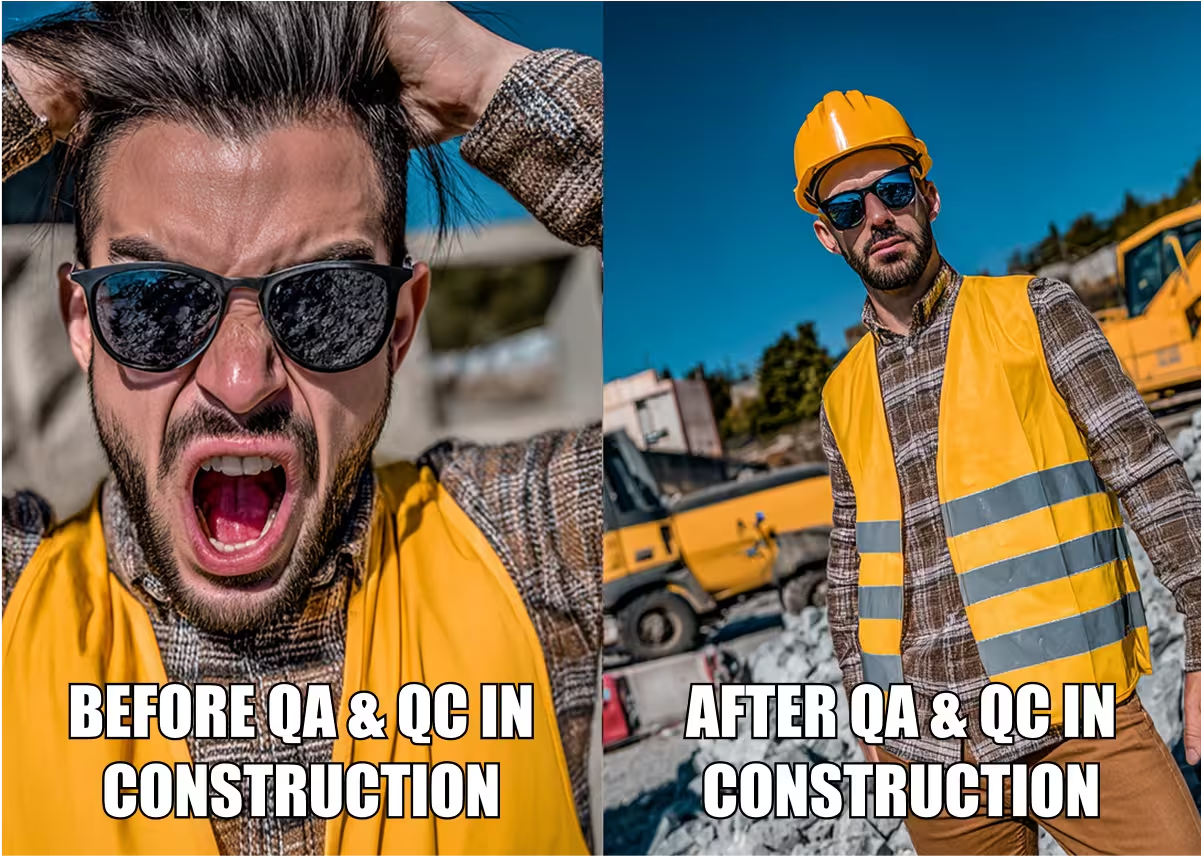
Time, cost, and quality form the project management triangle. These three elements play a key role in every construction project, and they connect closely. If you shorten the timeline, for instance, you may need to increase costs or compromise on quality. Shift one point of the triangle, and the others must adjust to keep the project balanced.
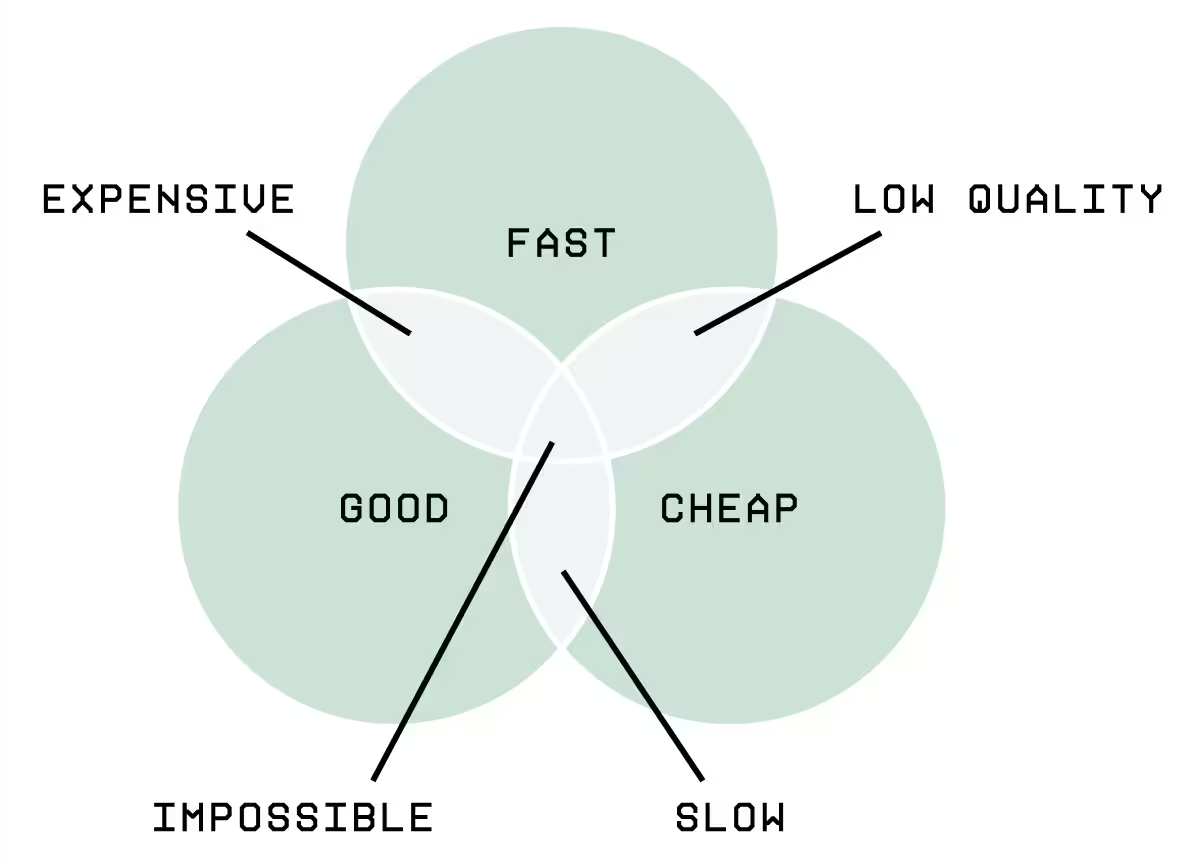
So, how does this affect QA/QC?
A realistic, well-structured project schedule lays the groundwork for quality. It gives teams the time and structure they need. They can follow QA protocols, conduct inspections, and fix issues before they get worse.
A rushed schedule often means skipped steps—whether it’s inadequate curing time, missed inspections, or rushed documentation. These shortcuts can directly impact the quality of the final build.
When teams see the schedule as a tool for quality, they can improve their work. This approach allows for careful planning and ongoing progress.
Outbuild supports this approach by making it easier to plan and adjust your construction schedule. You can visualize your progress in real-time, so you stay on track without losing quality.
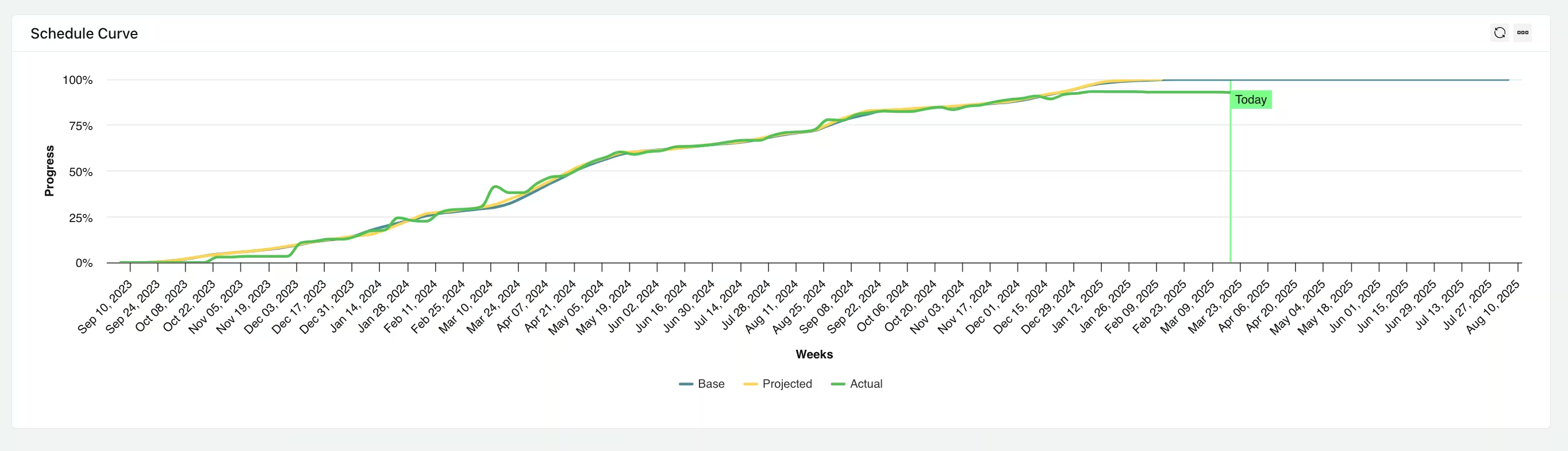
By investing in a strong QA/QC framework today, you are building a solid foundation. This will lead to reliable projects and a great reputation in the construction industry. Try Outbuild free for 14 days—no credit card required. Or, schedule a demo to learn more.
Common Pitfalls of QA QC in Construction
- Inconsistent Inspections: Sometimes, teams skip steps or rush through checks, assuming everything is fine. This can lead to overlooked defects that become costly later.
- Poor Staff Training: If your staff doesn't know how to fill out forms or read plans properly, your QA/QC framework loses its effectiveness.
- Ignoring Minor Defects: Even small deviations can cause big problems in structural integrity or project scheduling.
- Failing to Update Plans: Construction methods and regulations evolve and documentation must mirror this.
Putting qa qc construction protocols into everyday practice helps minimize these risks. Each step, from daily site checks to final project sign-off, is an important piece of the construction process.
A good quality control and assurance plan for construction projects is more than a checklist. It is a strategic tool. This helps keep your project on schedule, meet regulations, and satisfy stakeholders.
By creating clear standards in a construction QA QC plan template, you provide every team member with a clear path to follow. And by routinely inspecting work, you catch issues before they escalate into expensive, time-consuming problems.
If you’ve been searching for ways to strengthen your qa qc plan for construction project goals, now is the time to act.
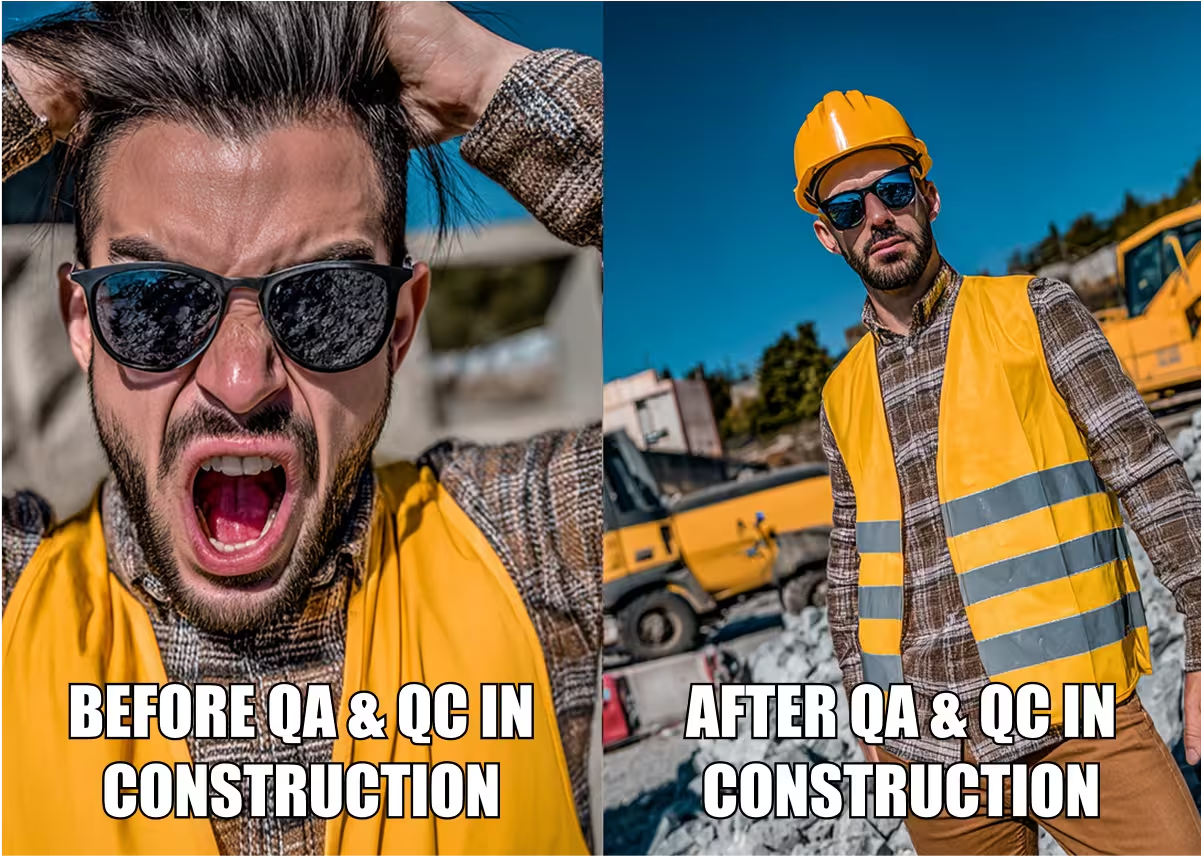
Time, cost, and quality form the project management triangle. These three elements play a key role in every construction project, and they connect closely. If you shorten the timeline, for instance, you may need to increase costs or compromise on quality. Shift one point of the triangle, and the others must adjust to keep the project balanced.
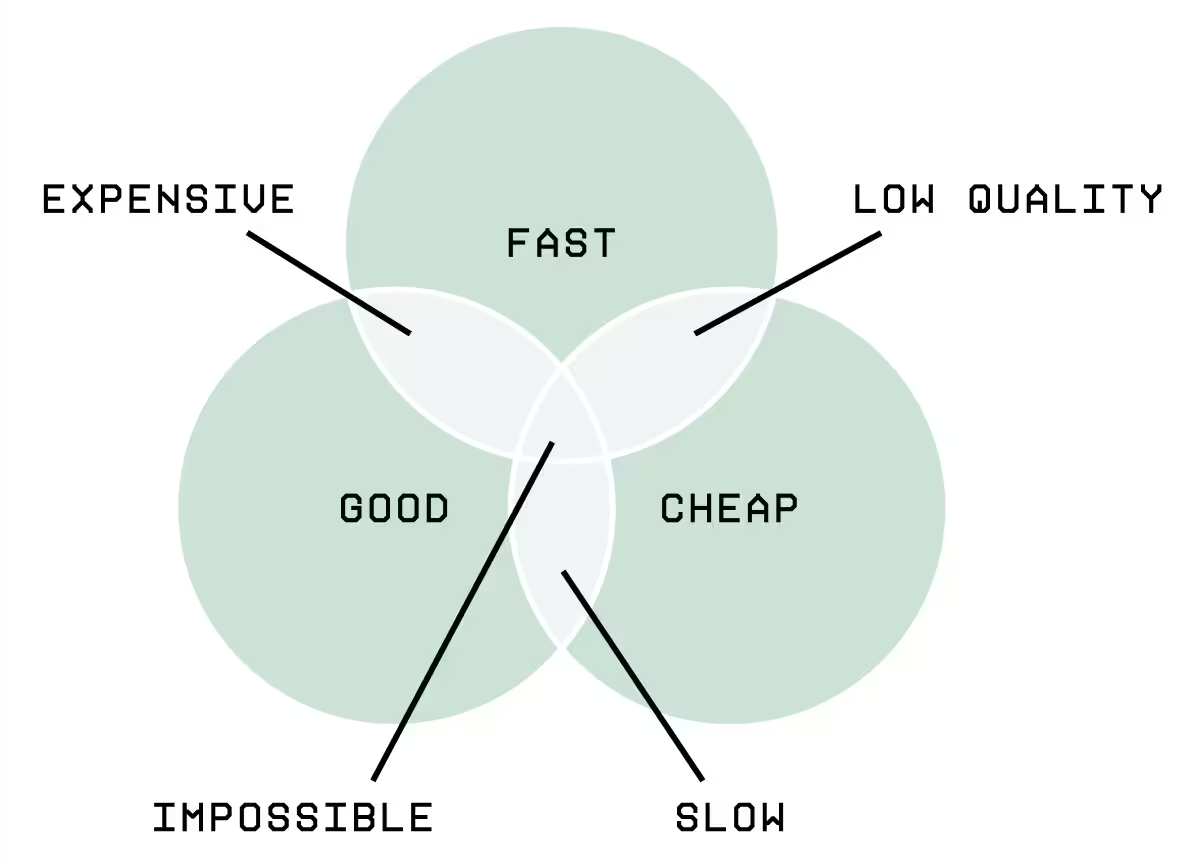
So, how does this affect QA/QC?
A realistic, well-structured project schedule lays the groundwork for quality. It gives teams the time and structure they need. They can follow QA protocols, conduct inspections, and fix issues before they get worse.
A rushed schedule often means skipped steps—whether it’s inadequate curing time, missed inspections, or rushed documentation. These shortcuts can directly impact the quality of the final build.
When teams see the schedule as a tool for quality, they can improve their work. This approach allows for careful planning and ongoing progress.
Outbuild supports this approach by making it easier to plan and adjust your construction schedule. You can visualize your progress in real-time, so you stay on track without losing quality.
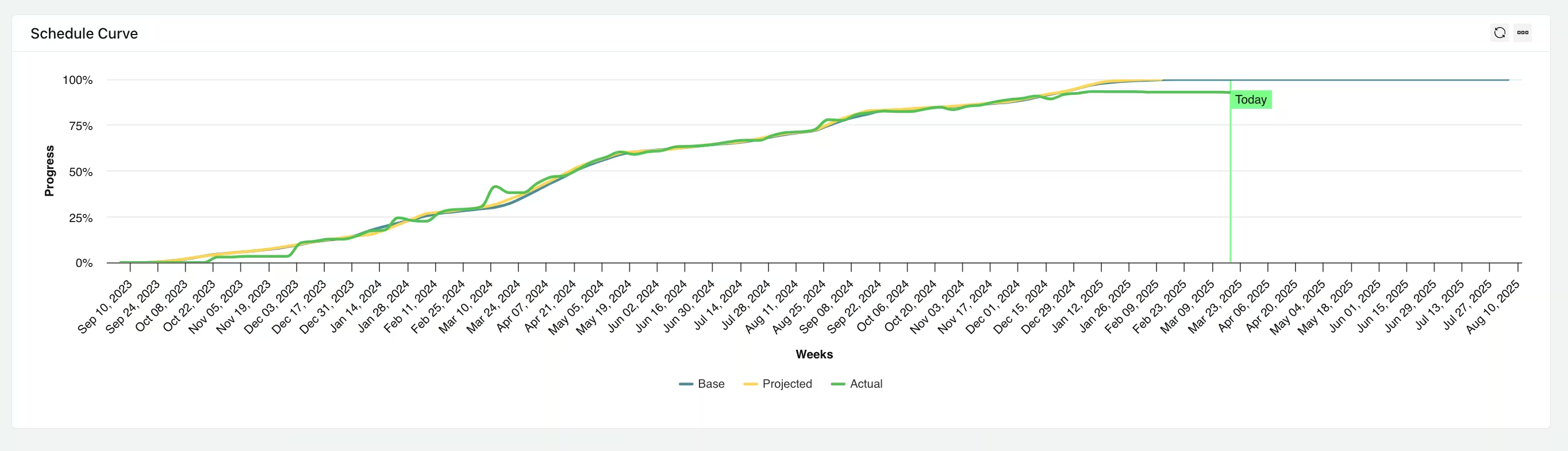
By investing in a strong QA/QC framework today, you are building a solid foundation. This will lead to reliable projects and a great reputation in the construction industry. Try Outbuild free for 14 days—no credit card required. Or, schedule a demo to learn more.
Frequently Asked Questions
There are many quality-related jobs in construction. These include quality assurance specialists, quality control superintendents, and quality managers.
A quality assurance specialist develops and maintains systems to ensure quality throughout the project. Their goal is to prevent issues before they happen.
A QC superintendent inspects work, logs findings, ensures compliance, and helps resolve problems on site.
A quality manager in construction oversees quality assurance and quality control for a project. This includes planning, audits, and ongoing improvement.
Related Articles
Ready to see Outbuild?
Join hundreds of contractors from 10+ countries that are saving money by scheduling better